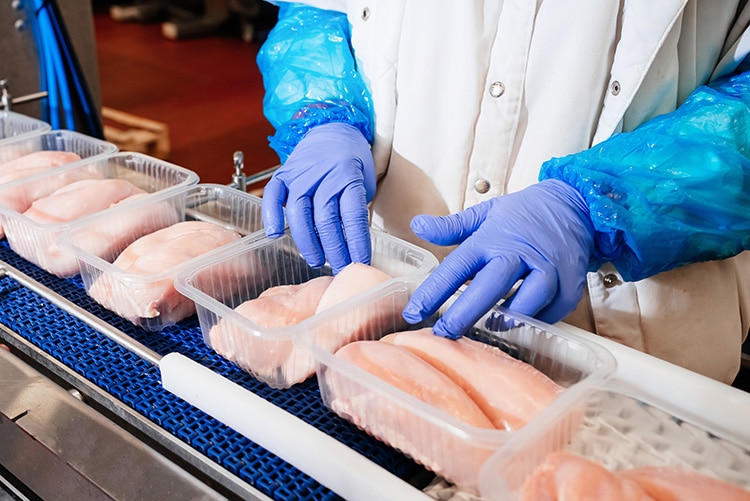
Thin dense chrome (TDC), a uniquely specialized functional coating, is celebrated for its unrivaled hardness, impressive wear resistance, and exceptional corrosion protection properties. Its robust attributes make it an ideal selection for various components and applications. This article delves into the merits of two distinct types of thin dense chrome coatings – Armoloy nodular TDC and Electrolizing micro crack TDC – and their potential roles in bolstering the performance and reliability of critical components in the food processing and packaging sector.
Beyond Conventional Coatings
The food processing and packaging industry grapples with distinct challenges when preserving the effectiveness and integrity of its machinery and equipment. Machine components, bereft of any functional coatings, often fail to endure the rigorous conditions witnessed during food processing, such as extreme temperatures, corrosive cleaning agents, and continuous mechanical stress.
Thin dense chrome, a distinctive functional surface coating, presents a compelling remedy by delivering superior protection and performance for essential food processing and packaging applications.
At the heart of this exploration is the Armoloy Innovation Center, a hub with a staff metallurgical department and R&D lab to test for objective results and to provide comprehensive consultation. By working to surface engineer the right coating, the center plays a pivotal role in determining the most suitable thin dense chrome for any specific application.
Deeper Understanding of Thin Dense Chrome (TDC)
Thin dense chrome is a process where a thin, dense layer of chromium is electroplated onto a component surface. Surfaces are typically made of steel, stainless steel, aluminum, or other metals. The plating process involves immersing the component in a proprietary electrolytic bath, where applying direct current causes chromium ions to deposit on the surface. The result is a dense, chromium layer with an effective deposit range as low as 0.000050 inches (1.2 μm).
Armoloy’s nodular thin dense chrome has many advantages, such as excellent adhesion, corrosion resistance, impressive hardness, outstanding wear resistance, low friction coefficient, and high uniformity and consistency, making it ideal for various applications in the food production industry.
However, when comparing Armoloy’s nodular TDC to Electrolizing’s micro cracked TDC, the latter can offer its own unique advantages. Microcracked thin dense chrome typically displays higher levels of surface coverage, which can enhance corrosion resistance. While the nodular TDC exhibits a micro-nodular structure that significantly improves wear resistance and reduces friction, the micro cracked TDC can also effectively resist wear and friction. This is mainly because the micro cracking facilitates lubrication retention, further reducing friction between component interfaces.
View of the two different coating surface structures provided by The Armoloy Corporation laboratory
The application of either Armoloy or Electrolizing depends largely on the unique benefits of each coating. There are a variety of factors, including expected operating conditions, desired degree of wear resistance, and acceptable levels of friction, that influence coating choice. Therefore, it’s essential to consult with experts, like the engineers at Armoloy’s Innovation Center, to make an informed decision.
Primary Advantages of Thin Dense Chrome
Outstanding Adhesion
Both TDC coatings create an absolute bond to the base material. This gives you an absolute bond without subjecting your parts to high heat or chemical etching. This adhesion ensures neither coating will delaminate and contaminate the food product.
Corrosion Protection
The nodular surface of the TDC coating is free from residual tensile stresses, creating a virtually crack-free surface that protects your substrate from corrosive elements. The micro cracks in Electrolizing thin dense chrome improve corrosion as well by allowing for the formation of a protective oxide film in the cracks. This characteristic makes both coatings suitable for daily corrosive washdowns used in standard raw food processing components.
High Hardness
Armoloy TDC boasts an impressive hardness level of 1000-1200 HV (up to 78 Rc), whereas Electrolizing TDC produces a respectable 72 Rc on average, surpassing most conventional materials used in food processing equipment. These remarkable hardness levels ensure coated components resist scratches, abrasion, and deformation, maintaining their integrity and prolonging their expected operating lifespan.
Wear Resistance
The nodular structure of Armoloy thin dense chrome provides outstanding wear resistance, making it ideal for applications involving sliding, rolling, or abrasive wear, such as bearings and linear guides commonly found in most processing and conveyor equipment. This property reduces the frequency of component replacement, resulting in cost savings and reduced downtime due to maintenance.
While Electrolizing’s TDC offers similar improvements in wear resistance, it’s best suited for applications requiring slightly thicker deposits. Heavier deposits can be advantageous when an extra level of corrosion protection or increased interval between recoating or replacement is needed. In addition to these standard wear issues, the unique surface structure of Armoloy is highly effective in preventing galling between similar material components, especially stainless steel.
Low Coefficient of Friction
Both TDC coatings’ low coefficient of friction reduces wear and prevents galling between sliding surfaces, enabling smooth operation and reducing the need for lubrication in some applications. The nodularity of Armoloy thin dense chrome acts as a dry lubricant; running two TDC plated components against themselves lowers the friction coefficient even further, resulting in a significantly extended service life.
Uniformity and Consistency
TDC coatings are highly precise and uniform, ensuring consistent performance across components and minimizing variability in the food processing and packaging processes. The coating forms an absolute bond to the base material, meaning no chipping, flaking, or peeling will occur.
Critical Components and Applications in the Food Industry
Rollers and Shafts
TDC-coated rollers and shafts are widely used in conveyor systems, bottling lines, and other food processing equipment. The excellent hardness and wear resistance of TDC ensure reliable and continuous product transportation while minimizing maintenance requirements.
TDC-plated steel rollers on a meat packaging conveyor line
Molds and Dies
TDC coatings on molds and dies prevent adhesion of food products, reduce friction, and resist wear, leading to improved production efficiency and product quality. Molds coated with thin dense chrome also require significantly less cleaning.
Cutting and Slicing Blades
The exceptional hardness and wear resistance of TDC coatings makes them ideal for cutting and slicing blades. TDC ensures sharp edge retention, enabling precision cutting and reducing product waste. Unlike traditional hard chrome, TDC will not create edge buildup during plating, eliminating post-machining requirements.
Valves and Fittings
TDC-coated valves and fittings resist corrosive elements found in various food products, extending their service life, preventing contamination, and reducing maintenance costs.
Chutes and Hoppers
TDC coatings on chutes and hoppers reduce material buildup and clogging, improving flow of food products and minimizing production disruptions.
Applications of Thin Dense Chrome in Packaging
Packaging Machinery Components
TDC coatings on packaging machine parts, such as forming dies and guide rails, improve wear resistance and reduce friction, mitigating contact fatigue risk. This increases machine longevity, reduces downtime, and improves packaging efficiency.
Food-Grade Coatings
To ensure compliance with food safety standards and regulations, one can apply TDC to applications requiring food-grade coatings by following strict guidelines. The USDA approves Armoloy TDC, and it complies with FDA requirements for food contact. In addition, Armoloy thin dense chrome is certified biocompatible for medical and surgical devices.
Important Considerations
Coating Thickness
Armoloy and Electrolizing thin dense chrome have a standard deposit range of 0.0001” to 0.0003” per side. Achieving precise and consistent coating thickness is crucial for optimum performance. Quality control measures are implemented to ensure uniformity across coated components.
Maintenance and Reapplication
You can return parts for stripping and re-plating as a cost-effective alternative to buying new components. For guidance on whether your part still has its coating, consulting with an Armoloy facility is recommended.
Industry Innovation Starts Here
As research progresses, TDC plays an increasingly pivotal role in ensuring food processing and packaging operations’ efficiency, reliability, and safety. TDC leads to cost savings while improving productivity and quality, solidifying its position as a valuable coating for food sectors.