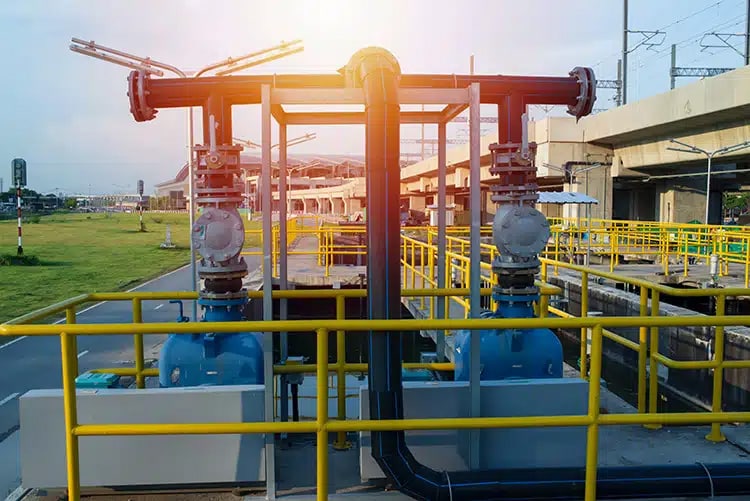
Pump Protection in Wastewater Treatment Plants
Designed to process and treat the water that flows through sewers, wastewater treatment plants make it safe to return water to the environment. Different types of pumps are used throughout the treatment process to move the wastewater, and sometimes the treated water, from one stage to the next.
Several factors can disrupt this process, and pump protection. Corrosion, abrasion, temperature variations, chemical exposure, and biofouling are challenges that negatively impact pump efficiency and reliability. Furthermore, a lack of regular maintenance, inadequate monitoring, and other human errors can result in pollution, regulatory violations, increased maintenance costs, and plant shutdowns.
But there is a way to get ahead of the risk and improve overall pump protection. Using a case study published in Pumps and Systems as a backdrop, we’ll discuss fluid mechanics’ role in pump design and how Armoloy thin dense chrome coatings and scheduled monitoring and maintenance can mitigate typical pump problems across various industries, reducing environmental and operational costs.
Fluid Mechanics and Wastewater Treatment Plants
Intricately designed systems, municipal wastewater treatment plants remove contaminants from water to make it safe for discharge back into the environment. From water flow through the plant to the behavior of particles and contaminants in the wastewater, understanding fluid dynamics is crucial for efficient and effective treatment, as well as prolonging wastewater pump protection.
A branch of physics known as fluid mechanics is present in the design, development, and testing of wastewater treatment plants. When wastewater arrives at the treatment plant, it’s often pumped from an inlet pumping station to the plant — especially necessary if the plant is at a higher elevation than the incoming sewer. Typically, submersible or dry well variety, these pumps can handle a large volume of water in the treatment process:
-
Primary Treatment
This stage allows for settling solids and floating lighter materials like oils and greases. Pumps move the wastewater at varying rates from the settling tanks to the next treatment step or to recirculate flows within the process. Fluid mechanics principles are used to design channels, weirs, and other structures to control and measure these flows.
-
Secondary Treatment
Here, biological processes break down organic matter in the water. Aeration is a standard process that requires blowers or air pumps to introduce oxygen, aiding the microorganisms in breaking down the organic matter. Proper air bubble distribution and adequate mixing in the tank are vital, therefore requiring an understanding of the dynamics of multiphase flows.
-
Tertiary Treatment
Now, the water goes through various processes such as filtration, disinfection, and sometimes nutrient removal. Again, pumps aid in water flow, and chemical dosing pumps may be used to introduce treatment chemicals.
-
Sludge Handling
The pumps, designed to handle high solid content, move sludge to digesters, drying beds, and other processing areas. Again, knowing the concepts of fluid flow, including pressure drops, flow rates, and potential for cavitation in pumps, is vital to pipeline efficiency.
-
Effluent Pumping
Once treated, the water, now referred to as effluent, may be pumped to a discharge point such as a river or possibly further treatment or re-use systems. Various pumps, including centrifugal pumps, are often used for this final pumping stage.
Besides the main treatment steps, there are various other pumping needs in a wastewater treatment plant, such as pumping chemicals, recirculating flows, or handling stormwater overflows.
Industry-wide Pump Predicaments
Given the importance of fluid mechanics in wastewater treatment, professionals in this area typically have a strong background in civil and environmental engineering, where fluid mechanics is a foundational topic.
The concepts of fluid mechanics are highly relevant in other industries — such as food processing, oil and gas extraction, and medical device manufacturing. These applications all rely on specialized pumps that meet specific requirements. Regardless of the application, some standards remain the same in terms of pump protection: all pumps must be corrosion-resistant, capable of handling solids, and controlled to match variable flow conditions. Common issues that prove detrimental to pump performance, regardless of industry, include:
Poorly Designed Systems
The overall design of the pumping system and its integration into the more extensive system is critical. Poor design can lead to inefficiencies, increased energy consumption, and reliability issues. For example, choosing the wrong type or size of pump for a particular application can lead to inefficient operation. Thermal expansion is also an important design consideration, especially when there are significant temperature variations in the pumping fluid or in the pump’s environment. When the metals and plastics used in pump construction expand or contract with temperature changes, misalignments or changes in tolerances within the pump assembly can occur — potentially leading to reduced performance, increased wear, or even failure.
Susceptibility to Corrosion and Abrasion
When losses in flow volume occur — along with reduced suction and discharge pressure and amperage draw — pump corrosion, abrasion, and wear are likely culprits. The nature of wastewater, for example, including biofouling, where some organisms produce corrosive by-products, can deteriorate the pump’s materials, reducing its lifespan. Pump components are also negatively affected by chemicals used in the treatment process or present in wastewater, which might cause corrosion or other forms of degradation.
Susceptibility to Thermal Expansion
Thermal expansion can be an issue, especially when there are significant temperature variations in the pumping fluid or in the environment where the pump operates. When the metals and plastics used in pump construction expand or contract with temperature changes, misalignments or changes in tolerances within the pump assembly can occur — potentially leading to reduced performance, increased wear, or even failure of the pump protection agent.
Inadequate Monitoring, Control, and Maintenance
Lack of effective monitoring and control systems can result in unnoticed performance degradation and potential damage over time. Therefore, regular maintenance is critical to pumps operating efficiently. Neglecting maintenance can lead to decreased performance and unexpected breakdowns.
Human Error
As with any systems breakdown, incorrect operation, lack of knowledge, or inadequate training can lead to mistakes that negatively impact pump performance.
Solving for Pump Predicaments with Protective Coatings
Many variables are at play regarding pump protection and performance; however, utilizing protective coatings, like those from Armoloy, is a proactive strategy for improving efficiency, mitigating risk, and reducing operational and financial costs. One example is published in Pumps and Systems:
The Problem
During a routine maintenance check at a wastewater treatment plant, a pump goes through observation for performance issues. It becomes clear, after disassembly, that there are areas of high wear and corrosion losses due to inadequate pump protection.
The Solution
Steam cleaning and grit blasting is step one to the solution. The sections where metal loss occurs go through rebuilding processes according to original tolerances via OEM specifications. Then, all exposed surfaces where corrosion could occur receive two coats of a low coefficient of friction coating.
The Result
The protective coating interrupts the corrosion/erosion process, improving pump protection, reliability, and performance by significantly reducing surface roughness over the base metal component and decreasing surface energy. The result is less wetting of the pump’s internal surfaces from the process flow, reducing overall friction losses.
Energy Consumption per Unit Flow and Efficiency Curves of Pump
Applications for Oil and Gas
Armoloy TDC® coatings perfectly tailor to components functioning in corrosive downhole settings. Thin dense chrome provides superior resistance to corrosion and wear, facilitating extended equipment run time and minimizing the need for costly repairs, thereby reducing downtime.
Armoloy coatings can be removed from the base material and reapplied almost endlessly, helping avert expensive component replacements. Exhibiting high chemical resistance, Armoloy Nodular TDC® and Armoloy XADC® also withstand most chemicals, except for sulfuric and hydrochloric acid.
Beyond safeguarding against corrosion and wear, Armoloy TDC® coatings can also enhance media flow rates, owing to diminished friction at the surface. Up to a 10% improvement in flow has been achievable in practical applications. Furthermore, by introducing a sub-layer of electroless nickel beneath the Armoloy coating, the Bi-Protec® coating dramatically amplifies corrosion resistance. Bi-Protec® has frequently use in pump protection for downhole pump applications in the oil and gas sector.
Applications for Food Processing
Armoloy TDC® and Armoloy XADC® are typical applications to food processing and packaging components for their unique wear and corrosion resistance combination. The coating’s absolute bond and stainless steel against stainless steel galling protection provide optimal processed product purity — the coating will not chip, flake, or peel.
Furthermore, Armoloy coatings have USDA approval and FDA compliance for food contact applications. The coatings can withstand temperatures above 1200˚F and carry no effect from thermal shock when cooled.
Finally, Armoloy TDC® coatings protect against corrosion caused by daily wash-downs, reducing maintenance downtime.
Applications for Medical Devices
Laparoscopes and endoscopes use fluid flows for various functions, like clearing the surgical area or inflating body cavities for better visibility. Drug delivery systems also rely on fluid dynamics principles to determine the flow rate of fluids in IV systems, specifically, understanding how changes in tube diameter, fluid viscosity, or pump speed can affect the delivery rate of medications to the patient. Artificial heart valves, stents, heart pumps, and other cardiovascular devices require the right design to handle the dynamic flow of blood and not disrupt the natural rhythm or cause any damage to blood cells.
Hydrophobic coatings from ME-92® and AL-COAT® repel fluids and provide smooth sliding surfaces, as well as reduce friction and improve corrosion resistance. Both have met ASTM Hemolysis (ISO 10993-4) requirements to evaluate the adverse effects of blood-contacting medical devices or biomaterials on blood or blood components. The effects evaluated include adverse reactions such as thrombosis and other blood-associated adverse events.
Partner with Armoloy
With your requirements in hand, engineers at the Armoloy Innovation Center can test, offer advice, and take steps to mitigate pump issues, regardless of industry. Let’s find a solution to your most pressing design and maintenance challenges together.