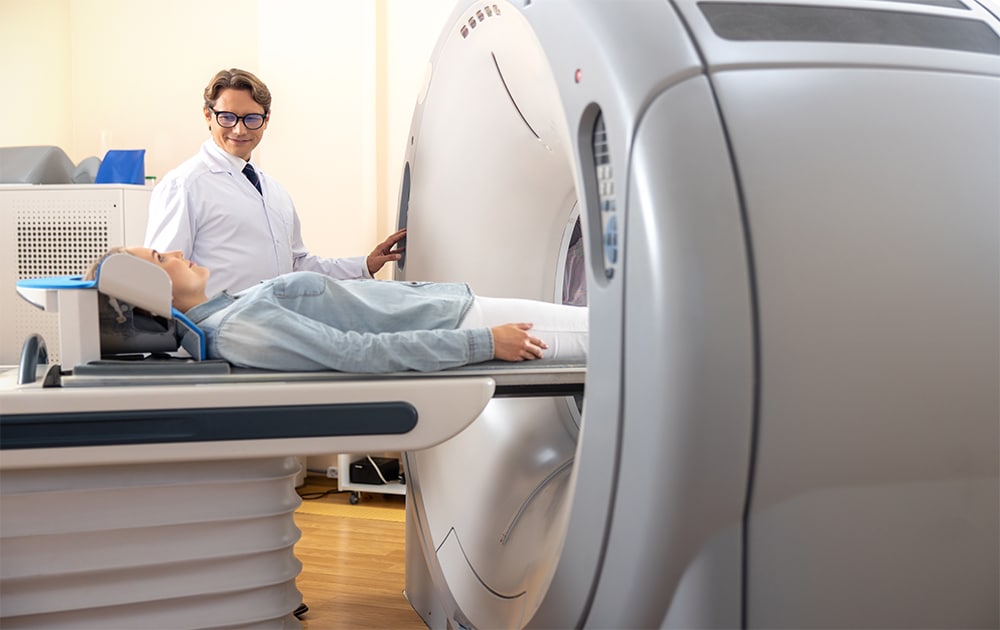
Over the years, computer tomography (CT) technology has evolved rapidly. From the initial scanners that took hours to acquire a single slice and days to process the image, modern CT scanners can now capture multiple slices in a fraction of a second with real-time image processing. This evolution has expanded the use of CT scanning beyond the brain to virtually all parts of the body, therefore transforming it into an indispensable tool in various medical fields such as oncology, cardiology, and trauma.
These sophisticated healthcare machines provide invaluable insights into the human body, aiding in diagnosis and treatment planning. However, the high-speed rotation and heavy loads they endure pose significant engineering challenges, particularly in minimizing metal bearing friction and wear. Markedly, this is where precision chromium coatings on CT scanner slewing bearings come into play, offering a solution that is as ingenious as it is effective.
The Engineering Challenge: High Speeds and Heavy Loads
CT scanners operate by rotating a gantry, housing an X-ray source and photon detectors, around the patient at high speeds. Modern multi-detector CT scanners often have gantry rotation speeds ranging from 0.33 to 0.5 seconds per revolution. However, this high-speed rotation, while essential for detailed cross-sectional images, subjects the slewing bearings to extreme stress. The bearings must support the weight of the gantry system and withstand the forces generated by rapid rotation, all while maintaining precision and stability.
The Importance of Reducing Bearing Friction
Friction is the nemesis of mechanical efficiency. In modern CT scanners, excessive bearing friction can lead to premature wear and tear, increased heat generation, and energy inefficiencies, potentially compromising image quality and scanner longevity. Hence, reducing bearing friction is not just a matter of operational efficiency but also of clinical efficacy and equipment durability.
View of the gantry component in a modern computed tomography machine.
The Solution: Thin Dense Chrome Coatings
Enter Armoloy Nodular Thin Dense Chrome (TDC), a technological marvel in the world of bearings. Nodular Thin Dense Chrome is a specialized electroplating process designed for metal components of all shapes and sizes, and operating conditions. It creates a micronodular, crack-free surface texture and imparts a hard, uniform chromium layer. This coating ensures maintained tolerances and balance without needing further machining, even with complex geometries where intricate cavities and spaces are difficult to coat with conventional coatings that produce thicker deposits. The performance characteristics of TDC offer significant benefits for precision-critical bearings in medical devices.
Performance Characteristics of TDC
- Hardness and Durability: TDC coatings are incredibly hard, generously harder than traditional hard chrome plating. This hardness translates to exceptional wear resistance, a critical feature in the high-stress operation of a CT scanner gantry slewing bearing.
- Smoothness and Low Friction: The smooth and naturally dry-lubricating surface of thin dense chrome coatings results in a low coefficient of friction. This smoothness is not just about touch; it’s about interaction. When bearings are coated with TDC, their interaction with other components becomes smoother, leading to less resistance and wear. When two contacting components are both coated with thin dense chrome, the friction coefficient is reduced even further.
- Uniformity and Precision: The application of TDC allows for a uniform coating, essential for maintaining the precision required in CT scanner bearings. Any irregularity, no matter how minute, can lead to imbalances and operational inefficiencies.
Anatomy of a TDC-coated slewing bearing used in CT scanners.
The Impact of TDC on Computed Tomography Performance
Enhanced Image Quality
By reducing bearing friction, TDC-coated bearings contribute to smoother gantry rotation, which is directly linked to image quality. The steadier the movement, the clearer and more precise the images. This clarity is not just about better pictures; it’s about better patient diagnoses and outcomes.
Extended Equipment Life
The durability of thin dense chrome coatings extends the life of bearings, and by extension, the CT scanner itself. Thus, longevity is not just a cost-saving measure but also a matter of healthcare sustainability.
Operational Efficiency
With less wear and tear and reduced heat generation, TDC coatings contribute to the overall efficiency of CT scanners. This efficiency means faster scan times, reduced downtime for maintenance, and, ultimately, more patients served.
A Small Component with a Huge Impact
The use of thin dense chrome coatings in the gantry bearings of computed tomography machines is a testament to the power of material science and engineering in advancing medical technology. By addressing the fundamental challenge of bearing friction, TDC coatings enhance the performance, durability, and efficiency of scanners. This advancement, seemingly minute in the grand scheme of a CT scanner, underscores a profound truth in engineering and medicine: sometimes, the smallest components can have the most significant impact.
As we continue to push the boundaries of medical technology, the role of innovations like thin dense chrome coatings serves as a reminder of the intricate interplay between different fields of science and technology. It’s a dance of electrons and elements, physics and physiology, all coming together to improve human health and well-being.
Partner With Armoloy
Mitigate unexpected downtime caused by metal friction and improve machine performance for your operations. Meet our group of curious, innovative surface engineers and learn how we can help improve your industry with the science of precision coatings.