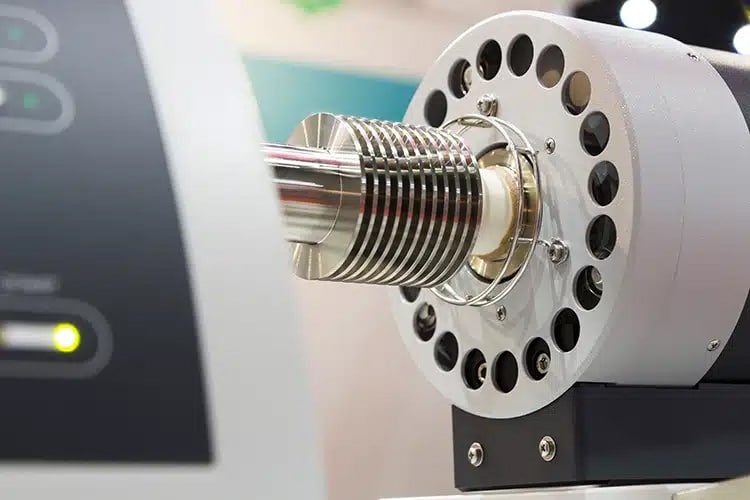
Thermal expansion is an important — and complicated — phenomenon to consider when designing or modifying industrial applications. A physical property observed in solids, liquids, and gases, thermal expansion occurs when the volume of the material changes in response to a change in temperature. When a substance is heated, its particles gain energy and move more rapidly. During this increased movement, particles push against each other, causing the material to expand. Conversely, when most materials cool, they contract.
Of course, there are exceptions to this rule. For example, the behavior of water near its freezing point: between 0°C and 4°C, water contracts as it gets warmer. As a result, ice floats on water, as ice density is less than that of liquid water. Counterintuitively, some materials exhibit negative thermal expansion (NTE); this means the materials contract when heated over a specific temperature range. Zirconium tungstate is one of the more well-known materials with NTE properties. Combining Zirconium tungstate with materials that exhibit positive thermal expansion means creating composites with tailored or near-zero thermal expansion coefficients is possible.
When discussing thermal expansion, the Coefficient of Linear Expansion measures how much a solid expands or contracts per unit length for a unit change in temperature. For liquids and gases, the measurement is the Coefficient of Volume Expansion.
Engineers and material scientists will typically choose materials and coatings based on a combination of their thermal expansion properties, strength, durability, corrosion resistance, and other pertinent factors to ensure long-lasting and efficient performance.
Effects of Thermal Expansion in Industry
Materials across various industries, from aerospace and automotive to medical and manufacturing, are subjected to thermal expansion. Structural deficits, thermal fatigue, and compromised appearance are some issues that arise in applications using materials with different thermal expansion coefficients.
Aerospace
From the intense heat of atmospheric re-entry to the cold vacuum of space, materials used in the aerospace industry — spacecraft, satellites, airplane engine components, launch vehicles, and other applications — must withstand significant temperature fluctuations.
Injection Molding
Plastic molding, a widespread manufacturing process used to produce myriad plastic parts and products, is intrinsically linked to thermal expansion. The mold itself, typically made of metal, also undergoes thermal expansion.
Components
Machined components must fit with other components (for example, a bearing in a housing). Discrepancies in thermal expansion coefficients between the parts can lead to fit issues, especially if the assembly undergoes temperature fluctuations during service. Furthermore, a component may also experience temperature fluctuations when in service — in engine parts, for example, temperatures can vary significantly, causing expansion and contraction.
Oil and Gas
The oil and gas industry deals with temperature fluctuations regularly, whether during the extraction, transportation, storage, or processing phases. From seals and components inside valves and pumps to pipes laid on the ocean floor, thermal expansion affects various equipment in the industry.
Nuclear Industry
In nuclear power plants, components such as reactor vessels, fuel rods, and cooling systems operate under extreme conditions, including high temperatures and radiation exposure. These conditions can lead to deformation and failure, compromising a reactor’s structural integrity.
Medical Devices
Protecting against thermal expansion is critical to ensuring the biocompatibility and functionality of medical devices, including orthopedic tooling, endoscopic cutters, dental reamers, and other surgical instruments.
Stainless steel flexible connector hose or expansion joint with flange and various hose shank adapter coupling with other for high and medium temperature or pressure resistant in industrial
Protect Against Thermal Expansion with Thin Dense Chromium Coatings
When selecting and applying chrome coatings, you must know the operating environment, including temperature fluctuations and the substrate material’s properties, to ensure that the coating is effective and protective over its intended lifespan.
Chrome plating is often applied to different substrates, such as steel, aluminum, and copper, for purposes like corrosion resistance, wear resistance, or aesthetics. If the substrate and the chrome have different rates of thermal expansion and the component undergoes temperature changes in its application, the difference in expansion rates can cause internal stresses.
Thin dense chrome coatings have a more refined deposit structure, which is advantageous in applications subject to thermal expansion. Electrolizing® thin dense chrome provides precise, thin depositions (tolerances of 0.00005″ to 0.001″ per side). As a result, the coating is less prone to delamination or spalling caused by the stresses from a mismatch in the Coefficient of Thermal Expansion (CTE) between the substrate and the chrome layer; Electrolizing® coatings “follow” the base metal’s expansion and contraction more closely.
Coefficient of Linear Expansion:
Thin Dense Chrome Coatings
- Electrolizing® Thin Dense Chrome: 2.7 – 4.6 (10⁶/°F)
- ALCOAT®: 2.7 – 4.6 (10⁶/°F)
Common Base Metals
- Aluminum: 21 – 24 (10⁶/°F)
- Brass: 18 – 19 (10⁶/°F)
- Copper: 16 – 16.7 (10⁶/°F)
- Steel: 10.8 – 12.5 (10⁶/°F)
- Steel Stainless Austenitic (304): 17.3 (10⁶/°F)
- Steel Stainless Austenitic (310): 14.4 (10⁶/°F)
- Steel Stainless Austenitic (316): 16.0 (10⁶/°F)
- Steel Stainless Ferritic (410): 9.9 (10⁶/°F)
Furthermore, Electrolizing® provides improved adhesion, the most critical focus of the coating technology. Coatings must meet the ASTM-B-489-85 standard and repeated bend testing to 180 degrees without showing signs of chipping, spalling, or separation — especially advantageous in applications with significant temperature fluctuations, as the coating is less likely to delaminate.
In addition to its protective benefits around thermal expansion, Electrolizing® thin dense chrome offers:
- High Hardness and Wear Resistance: Electrolizing® provides metals with a surface hardness of Rc 72 Rockwell. Compared to conventional chrome plating, the density of Electrolizing® coatings results in fewer cracks, inclusions, and other surface irregularities. This combination of density and hardness makes Electrolizing® thin dense chrome highly protective against abrasive, adhesive, and corrosive wear — even under fluctuating temperatures.
- Low Coefficient of Friction: Thin dense chrome offers a low resistance to sliding, which is beneficial in moving parts subjected to thermal expansion. Utilizing Electrolizing® coatings can reduce wear and improve the overall efficiency of mechanical systems.
- Uniform Thickness: The process used for Electrolizing® provides consistent, uniform thickness, ensuring that complex component shapes are equally protected, even as they expand or contract with temperature changes. Furthermore, thin dense chrome coatings introduce only a minimal dimensional change to the part, which is crucial in precision applications where tight tolerances are necessary, and parts might undergo temperature changes.
Proactive Testing, Precise Performance
At the Armoloy Innovation Lab, our engineers continually test and measure performance to understand how Electrolizing thin dense chrome coatings respond to thermal expansion. As technology advances and our understanding of materials deepens, further insights into thermal expansion mechanisms will undoubtedly pave the way for even more innovative and resilient coating solutions.
Ready to discuss your next project?