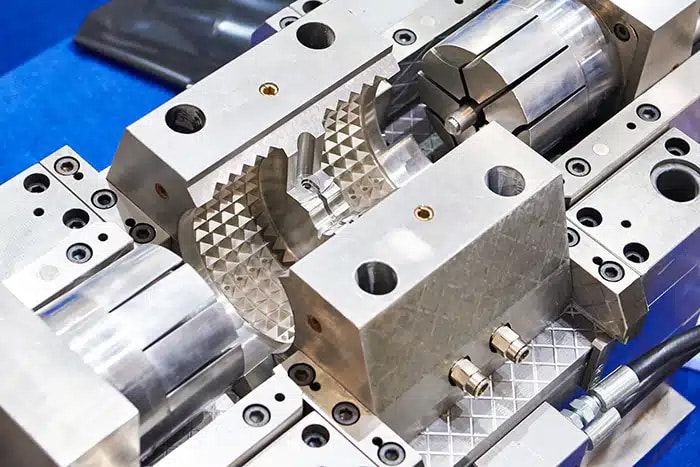
The shape of a component is far more than mere aesthetics; it serves as the foundation upon which functionality, performance, and overall system efficiency are built. Component shapes directly influence behavior, interactions with other parts, and ability to meet specific functional requirements. From core bearings, gears, and shafts to more advanced automated lines and specialized machinery, every component is carefully crafted with precision and purpose for component shape preservation.
Choosing the right surface coating to enhance the performance and durability of components is another essential decision in the initial design and maintenance process. However, some organizations may still forgo this crucial step — increasingly, to financial, legal, environmental, and reputational detriment.
Here, we’ll discuss how the shape of a component influences successful product design, and why utilizing protective coatings like thin dense chrome on machined components during the design phase leads to the most beneficial outcomes of component shape preservation.
Designing Components for Form and Function
First and foremost, a component’s shape directly influences its functionality and performance. The correct shape ensures proper fit, alignment, and interaction with other components — as well as how it handles a variety of elements, including:
Liquids and gases
In components where liquids or gases are meant to pass through, such as in medical devices, pipes, and turbines, the shape is critical. The cross-sectional area, length, curvature, and other factors can greatly affect the flow rate, pressure, turbulence, and other properties of the fluid. This, in turn, impacts the performance of the entire system.
Mechanical stress
The shape of a component also affects how it can handle different types of mechanical stress. For example, the landing gear is an essential component of any aircraft, tasked with supporting the entire weight of the aircraft during landing and takeoff and also playing a crucial role during taxiing and parking. The shape and design of landing gear components must be able to handle different forms of mechanical stress, including contact fatigue due to cyclical loading and unloading.
Heat
How a component handles heat is also tied to shape. The shape of injection molding tools, for example, has a direct impact on their thermal properties and the overall success of the molding process. First, if a mold’s shape is uniform, with evenly distributed mass, it can help ensure consistent thermal expansion across the tool. However, more complex shapes can be more challenging in terms of thermal expansion. Intricate details or thin, extended parts of the mold may cool and contract faster than thicker parts. This can lead to stresses within the tool, which can cause warping or even cracking over time. Finally, the design and layout of the cooling channels within the tool can significantly affect how it cools and contracts after the injection phase. These channels need to be designed and positioned to ensure even cooling throughout the tool, preventing uneven contraction that could cause stress and damage.
However, the component shape is only one factor to consider. For optimal functionality that stands the test of time, consider including thin dense chrome coatings during the component design phase to combat metal fatigue, wear, and corrosion.
Thin Dense Chrome Protects Components
From reduced maintenance to increased production due to improved cycle times, the performance and functionality Electrolizing® thin dense chrome provides are unmatched. At the Armoloy Innovation Center, our team can engineer a unique coating solution for machined components that provides the following benefits:
Thin, Even Deposit Doesn’t Affect Part Tolerances, Weights, or Balances
Electrolizing® specializes in high-precision applications. We work within close tolerances, applying as little as 0.00005″ to the component surface, with a typical range of 0.0001” to 0.0003”. Furthermore, utilizing thin dense chrome doesn’t add significant mass to the component. This is especially critical in industries such as aerospace, where even small weight additions can affect the performance or safety of an aircraft. Finally, where balance is critical — for example, in rotating machinery or parts — a uniform thin dense chrome application is key to high performance.
Low Coefficient of Friction (CoF)
A low CoF helps reduce wear and extends the life of components, especially those subject to a sliding or rolling motion against each other. Electrolizing® thin dense chrome coatings improve the surface properties of components, providing improved resistance to corrosion and abrasion while reducing heat, maintenance, and downtime.
Cold Process Doesn’t Affect Component Shape Geometry
Unlike some coating or treatment processes, the Electrolizing® thin dense chrome process doesn’t use high temperatures to deposit chrome onto the substrate. Many treatments or coatings require elevated temperatures, which can induce thermal stresses, cause distortion, or lead to changes in the metallurgical properties of the part. By using a cold electroplating process, Electrolizing® avoids these potential issues.
Ability to Withstand High Operating Temperatures
Electrolizing® thin dense chrome coating retains its key properties and performs effectively without degradation, even when exposed to temperatures as high as 1,600°F (about 871°C). This makes the coating particularly valuable in industries and applications where components face both abrasive wear and high thermal stresses. Specifically, Electrolizing® TDC:
- Won’t break down, oxidize rapidly, or deteriorate at high temperatures. This is crucial in applications where the component may have exposure to intense heat, such as in jet engines, industrial machinery, or certain high-temperature chemical processes.
- Won’t blister, peel, or delaminate from the component material due to the high temperatures. This ensures that the coated component remains protected, and functions as intended.
- Won’t have adverse effects on the component.
- Will retain its key properties. Even at such high temperatures, the Electrolizing® coating will continue to offer its characteristic benefits like wear resistance, reduced friction, and corrosion protection.
Electrolizing® for Every Component
Extremely versatile, Electrolizing® thin dense chrome is certifiable to AMS 2460 — and customer-driven specifications. At the Armoloy Innovation Center, our coating and plating-specific metallurgical consultants work with clients to develop applications and procurement solutions to meet your components’ specific needs for component shape preservation.