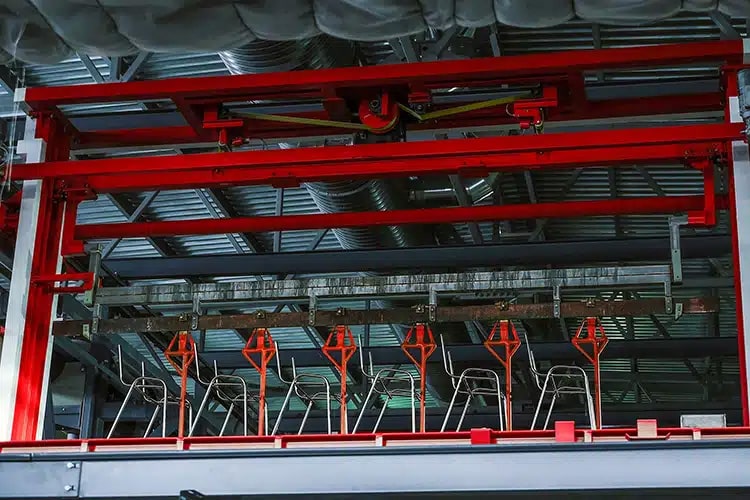
The hazardous waste, fumes, and health risks in association with hexavalent chrome plating are well-publicized. Rarely, however, do we hear about the macro-environmental benefits of thin dense chrome (TDC), specifically around reducing friction and energy consumption, when the chrome plating process has proper management.
While thin dense chrome has some environmental downsides, failure to recognize the big-picture positives is just as costly. Here, we’ll explain why thin dense chrome electroplating consumes less energy compared to hard chrome plating. Next, we’ll discuss why working with a reputable thin dense chrome provider — one who commits to correct process controls every time – is critical to ensuring environmental safety, regulatory compliance, and supply chain integrity.
Finally, in a follow-up post, we’ll provide a deep dive into the significant friction-reduction and energy-saving benefits thin dense chrome provides on a global scale in manufacturing, transportation, and renewable energy generation.
Thin dense chrome plating vs. hard chrome plating
Thin dense chrome plating and hard chrome plating are two types of electroplating processes used to coat metal objects with a layer of chromium. There are significant differences, not only in the properties of the resulting coatings but also in the levels of energy consumption both plating processes require.
Coating property differences
- Electrolizing® thin dense chrome, for example, produces a very thin layer of chromium on the surface of the substrate, typically ranging from 0.00005 to 0.0002 inches. The thickness of the coating is achievable by controlling the current density during the electroplating process. The resulting coating is extremely hard, with a surface hardness of up to 70 Rockwell C, and is highly resistant to wear, corrosion, and chemical attack.
- Hard chrome plating is an older electroplating process that produces a much thicker layer of chromium on the surface of the substrate, typically ranging from 0.0005 to 0.010 inches. The resulting coating, while also hard (68 Rockwell C) and wear-resistant, is less dense and porous, making it more susceptible to corrosion and chemical attack.
Energy consumption differences
While factors such as the plating component size and shape, the desirable thickness of the coating, and the specific equipment in use come into play, overall, thin dense chrome plating consumes less energy than hard chrome plating.
- A newer and more advanced technology, thin dense chrome plating utilizes specialized electrolytes and current density controls to achieve a highly efficient plating process. Because it requires lower plating voltages and currents compared to hard chrome plating, the result is lower energy consumption and reduced greenhouse gas emissions.
- In contrast, hard chrome plating is an older technology that typically requires higher current densities and longer plating times to produce a thicker coating — both factors which lead to higher energy consumption and a detrimental impact on the environment.
Wastewater, a ghost town, and beyond
Used in the chrome plating process, hexavalent chromium, also known as hex chrome, is a highly toxic, carcinogenic chemical that can cause serious health and environmental problems if not handled properly.
Perhaps the most well-known depiction of a case involving hexavalent chromium was in the movie “Erin Brockovich.” In the 1990s, Pacific Gas and Electric (PG&E) was found to have contaminated the groundwater in the town of Hinkley, California with hexavalent chromium. The contamination, which occurred in 1952, was linked to health problems throughout this desert community. PG&E eventually paid a $333 million settlement, but the damage was done — today, Hinkley is essentially a ghost town.
Fast forward to August 2022, when Tribar Technologies, a Michigan-based auto supplier that manufactures chrome-finished parts, released highly toxic hexavalent chromium into a sewer system that discharges into the Huron River.
According to violation notices from the Michigan Department of Environment, Great Lakes and Energy (EGLE), a Tribar Technologies employee overrode the company’s waste treatment alarms 460 times over the course of three hours. Furthermore, EGLE found that Tribar Technologies, “failed to immediately notify EGLE about the discharge, interfered with a city’s wastewater treatment, and failed to maintain a pollution prevention plan.”
Ecological disaster, contaminated water comes out of the sewage system – an ecologist takes a sample of water for research.
Process controls, regulatory compliance, and the environment
The California and Michigan violations are just two of the many worldwide that demonstrate why adherence to quality and compliance standards is paramount to protecting people and the environment. Some process controls and regulatory standards that can help to reduce the risk of hexavalent chromium exposure and contamination include:
Administrative and engineering controls
Administrative controls are important for ensuring that workers are aware of the hazards with hexavalent chromium and have proper training on how to handle it safely. These include measures such as:
Training
Proper training is essential for workers who may be exposed to hexavalent chromium. Training should cover the hazards of hexavalent chromium, safe work practices, and the use of personal protective equipment (PPE). Gloves, respirators, and protective clothing can help to protect workers from exposure to hexavalent chromium. They should be provided to workers based on the level of risk associated with their job duties.
Work Procedures
Written work procedures can be used to outline safe work practices and to ensure that workers follow established protocols to minimize their exposure to hexavalent chromium.
Job Rotation
This involves rotating workers between different tasks to limit their exposure. This can involve scheduling breaks or rotating workers between different tasks.
Hazard Communication
Employers should provide workers with information about the hazards of hexavalent chromium, including information about the chemical’s properties, health effects, and safe handling procedures.
Engineering controls include measures such as ventilation systems, fume hoods, and exhaust systems that have designs to capture and remove hexavalent chromium particles and fumes from the air.
Local Exhaust Ventilation
This captures and removes contaminants at the source before possible worker inhalation could occur. For hexavalent chromium, a local exhaust ventilation system can be used to remove fumes and particles from welding or other processes that generate the chemical.
Enclosures
Enclosures physically separate workers from the source of hexavalent chromium. Most enclosures, such as welding booths, should have a design that prevents the escape of fumes or particles. The enclosure design should also have proper ventilation to ensure safe removal of any contaminants.
In partnership with the Armoloy Corporation’s Innovation Center, Electrolizing® develops both administrative and engineering processes, procedures, and training programs to maintain tight quality controls, mitigate variabilities while optimizing efficiencies, and protect workers and the environment.
Monitoring, testing, and regulatory compliance
Regular monitoring and testing of air, water, and soil samples can help to detect the presence of hexavalent chromium and ensure that process controls are effective in controlling its release.
- In the United States, the Occupational Safety and Health Administration (OSHA) has set a permissible exposure limit (PEL) of 5 micrograms per cubic meter of air (5 μg/m3) for hexavalent chromium in the workplace. Employers must implement the engineering and administrative controls previously discussed, provide workers with PPE, and conduct regular monitoring and testing to ensure that workers are not exposed to levels above the PEL.
- In the E.U., manufacturers must register and obtain authorization to use hexavalent chromium under the REACH (Registration, Evaluation, Authorization, and Restriction of Chemicals) regulation and also passed the Restriction on Hazardous Substances Directive (RoHS) which bans the use of certain hazardous substances in electrical and electronic equipment.
Electrolizing® follows OSHA protocols, and documents processing steps, quality measures, and maintenance procedures that are available for review for each application. We’re certified to ISO quality standards and compliant with the Food and Drug Administration (FDA), United States Department of Agriculture (USDA), and RoHS regulations.
Additional coating options with less environmental impact
Along with thin dense chrome, there are other plating options that are better for the environment including:
- Electroless nickel plating (ENP). For applications involving moderate to severe corrosion, electroless nickel plating uses less hazardous chemicals, such as nickel salts, reducing the environmental impact. Electroless nickel plating also generates less waste compared to traditional plating processes, which reduces the need for the disposal and treatment of hazardous waste. Because it is more energy-efficient, electroless nickel plating reduces greenhouse gas emissions and energy costs.
- Citric passivation. This non-electrolytic finishing process removes free iron and other surface contaminants to maximize the corrosion-resistant nature of most stainless steels. Citric acid is a natural, organic acid that is biodegradable and poses less risk to human health and the environment compared to nitric acid or other hazardous chemicals. Naturally, citric passivation is ideal for food and beverage and medical applications but is gaining ground in aerospace, semiconductor, and military operations. Furthermore, citric acid passivation complies with local and federal regulations governing the use and disposal of chemicals and waste products.
When choosing a coatings supplier, it’s critical to ask about their commitment to employee, workplace, regulatory, and environmental safety. At Electrolizing® we care deeply about protecting the environment and operating in compliance with local regulatory standards, earning the trust of global OEMs as their supplier of choice.
Environmental excellence at Electrolizing®
The experts at our Innovation Center can help you determine the right protective coating for your application while minimizing the impact on the environment.\