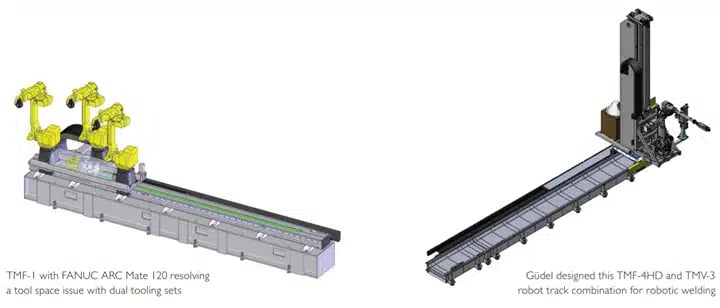
Before shop managers install a robot welding and joining system, they should understand its components, their functions and
how they relate to welding applications as well as general robotic automation tasks.
Advanced intelligence
Controls, communication instruments and operator interface components are interrelated, critical components in automation systems. System controls include both the robot controller and other system controllers such as PLCs and PCs. Generally, robot controllers are tasked with directing robot tooling and providing robot motion, while system controllers provide logic through inputs and outputs for events such as parts movement, communication to the production environment, system data acquisition and human interface.
The article below provides an overview of the essential components and considerations for installing a robotic welding system. It covers the significance of system controls, operator interfaces, safety measures, and the various components that constitute a robotic welding work cell. Additionally, it discusses the specific components required for welding applications, including the welding power source, interface, and wire feeder, among others. The piece also highlights the importance of choosing the right robot based on reach, payload, and speed, and how track motion modules can extend a robot’s work envelope. The final section emphasizes the critical role of human involvement in tasks that cannot be automated, underscoring the collaborative nature of robot welding systems.
Read more on Robotic Welding 101