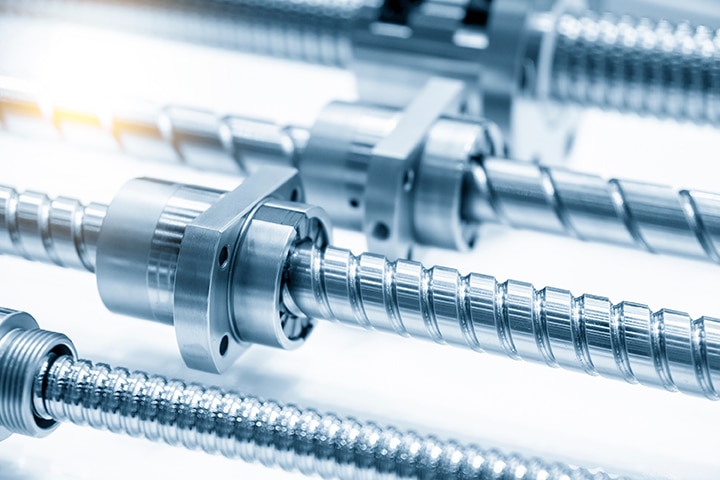
Known for their efficiency, precision, and durability, high load ball screws convert torque to linear force with minimal energy loss, making them ideal for applications requiring precise positioning, such as in CNC machines, robotics, aircraft flight control systems, and many types of industrial equipment. Furthermore, high load ball screws are highly efficient and enjoy a long lifespan due to their low friction, which uses less energy to achieve the same motion as compared to other mechanisms.
However, ball screws aren’t immune to failure. Here, we’ll provide an overview of how high load ball screws work, the various industries that rely on ball screws for their products and components, and strategies for mitigating failure and extending product life.
What are High Load Ball Screws, and How Do They Work?
A ball screw is a mechanical linear actuator that translates rotational motion to linear motion with very little friction. It consists of a screw (also known as a spindle) with a spiral groove and a ball nut with a series of channels inside it that the steel balls roll through. As the screw or the nut rotates, the return tube deflects the balls so they can travel through the ball nut’s thread and the screw’s groove. As a result, the ball assembly rolls between the screw shaft and nut threads, providing smooth and efficient movement.
Image source: IQS Directory
Ball screws are categorized based on various design and performance characteristics, which include their method of fabrication, precision level, and load-handling capabilities. Here are some common types of ball screws, organized by everyday manufacturing needs:
Precision Level
- Precision Ground Ball Screws: These ball screws are manufactured by grinding, allowing for very tight tolerances and smooth surface finishes. They offer high precision and are ideal for applications requiring exact positioning, such as CNC machine tools, aerospace applications, and high-speed machinery.
- Rolled Ball Screws: Less expensive than ground screws, rolled ball screws are made by cold rolling the screw thread. They provide good precision and are more cost-effective for applications without ultra-high precision requirements, such as industrial and automotive applications.
Configuration Type
- Single Start Ball Screw: This type has a single thread running along its length, which means the nut advances one pitch distance per one complete turn of the screw. Single start ball screws are the most common type used in a wide range of general applications.
- Multi Start Ball Screw: These have multiple threads on the screw shaft, allowing the nut to move faster along the screw for each turn, thus increasing the travel speed. Multi-start ball screws are used in applications requiring rapid movements.
Nut Design
- Single Nut Ball Screws: They have a single nut and are more straightforward in design but can experience more backlash and less load distribution.
- Double Nut Ball Screws: These designs use two nuts preloaded against each other to minimize backlash, increase stiffness, and improve load distribution. They are preferred in high-precision applications.
Load Handling
- Standard Ball Screws: Suitable for a wide range of general-purpose applications with moderate load and speed requirements.
- High Load Ball Screws: Explicitly designed to handle higher loads, this type of ball screw has a larger diameter or a more robust thread form to distribute the loads more effectively.
Special Features
- Coolant-Through Ball Screws: These feature internal channels for coolant flow, which helps in managing heat during high-speed operations.
- Corrosion-Resistant Ball Screws: Made from materials like stainless steel or coated with materials to resist corrosive environments.
Industries and Applications that Utilize High Load Ball Screws
High load ball screws are essential in several industries where machinery must handle heavy loads with precision and efficiency. These industries often demand robust performance characteristics to ensure reliability, durability, and accuracy under demanding conditions. Here are some key industries that specifically require high load ball screws in their applications:
Automotive
In automotive manufacturing, high load ball screws are used in assembly lines, press machines, and in the automation of production processes such as robotic arms. They are crucial for producing automotive parts and assemblies precisely and efficiently.
Aerospace
Aerospace applications require extremely high precision and reliability. High load ball screws see use in the actuation systems of aircraft, including control surfaces, landing gear, and engine components. They are also used in the manufacturing and maintenance of aircraft equipment.
Industrial Machinery
This broad category includes industries like metalworking, plastics, and textiles, where high load ball screws are used in lathes, milling machines, and injection molding machines. They enable these machines to operate under high stress and precision requirements.
Energy
In the energy industry, especially in renewable energy like wind turbines, high load ball screws are used to adjust blade angles and manage the orientation of solar panels. They must withstand environmental stresses and operational loads.
Heavy Machinery and Construction Equipment
Ball screws are used in construction equipment such as cranes and excavators and mining machinery. Their ability to handle high loads is crucial for this equipment’s efficient and safe operation.
Defense and Military
Military applications, which often involve demanding environmental conditions and the need for extreme reliability, use high load ball screws in vehicles, weaponry systems, and other military hardware.
Medical Equipment
Medical technology, particularly for devices like MRI machines, CT scanners, and other diagnostic equipment, utilizes high load ball screws to move heavy platforms precisely and smoothly.
Robotics and Automation
In robotic systems, especially those handling heavy items or performing high-precision tasks, high load ball screws provide the necessary movement control and load capacity.
High Load Ball Screw Failure: Causes and Mitigation Strategies
High load ball screw failures usually stem from a combination of factors related to design, operation, and maintenance—and can significantly impact production and safety in various industries. Here are some of the most common causes of high load ball screw failures:
Excessive Load
Overloading the ball screw beyond its designed static or dynamic load capacity can cause premature wear, deformation, or even catastrophic failure. To avoid overloading, select a ball screw with a suitable dynamic load capacity for the application.
Improper Lubrication
Inadequate lubrication can lead to increased heat generation and accelerated wear, while excessive lubrication can attract dirt and other contaminants, contributing to wear. Regularly lubricating the ball screw with the correct type of lubricant recommended by the manufacturer reduces friction, wear, and heat generation, extending the life of the ball screw. Automated lubrication systems can also ensure consistent lubrication without manual intervention.
Contamination
Dirt, dust, metal shavings, and other particulates can enter the ball nut and track, causing abrasive wear or jamming of the ball bearings. Contaminants can also degrade the lubricant, reducing its effectiveness. Implementing protective covers or bellows will help shield the ball screw from contaminants like dust, dirt, chips, and fluids. These covers’ design fit the machine’s specific movement and environment, prevent debris from entering the ball nut, and cause wear.
Misalignment
Improper installation or alignment of the ball screw assembly can lead to uneven load distribution, increased stress, and excessive wear. Misalignment may also occur over time due to settling or shifting of machine components. Proper alignment and using the appropriate end supports can prevent deflection and reduce stresses on the ball screw.
Fatigue
Under high load and continuous operation, the material of the ball screw can experience fatigue. Repeated stress cycles can lead to the formation of cracks and eventual failure of the ball screw.
Inadequate Design or Material Selection
Choosing a ball screw that is not suitable for the application’s load, speed, or environmental conditions can lead to failures. Material flaws or inadequate heat treatment can also weaken the ball screw.
Environmental Factors
Exposure to corrosive substances, extreme temperatures, or moisture can lead to corrosion and material degradation, compromising the structural integrity of the ball screw. If possible, control the environment where the ball screw operates—temperature, humidity, and exposure to corrosive agents—to reduce exposure to harmful conditions. For applications in particularly harsh environments, use ball screws with integrated sealing systems. Seals can prevent the ingress of contaminants into the critical moving parts of the ball screw assembly.
Improper Handling and Maintenance
Mishandling during installation, transportation, or maintenance can damage the delicate surfaces of the ball screw and nut. Lack of regular maintenance, such as inspection and lubricant replenishment, can also lead to failures.
The Role of Coatings in Protecting High Load Ball Screws
Protective coatings can play a crucial role in extending the lifespan and enhancing the performance of high load ball screws, especially in challenging operating environments. These coatings can protect against wear, corrosion, and environmental factors:
- Thin dense chrome plating enhances surface hardness, significantly improving wear resistance. It also provides excellent corrosion resistance, making it suitable for high-load applications and environments with corrosive substances.
- Nickel coatings offer excellent corrosion resistance and wear resistance, making them suitable for use in harsh environments. Nickel plating can also improve surface hardness, further protecting the ball screw from wear.
- Teflon (PTFE) coatings reduce friction between moving parts, decreasing wear and extending the life of the ball screw. This coating is particularly beneficial in applications requiring smooth motion and minimal lubrication.
- While less common for ball screws, anodizing has good use for aluminum parts to increase corrosion and wear resistance. It also provides a hard surface that can protect against scratches and environmental damage.
- Titanium Nitride (TiN) coating is known for its hardness and wear resistance. It can significantly extend the service life of ball screws by protecting against wear and galling. It’s suitable for high-precision applications where durability and performance are critical.
- Ceramic coatings offer excellent hardness, wear resistance, and thermal protection. They are suitable for applications where ball screw exposure is at high temperatures or in highly corrosive environments.
- Molybdenum Disulfide (MoS2) coating reduces friction and improves wear resistance, particularly in vacuum or space applications where traditional lubricants may evaporate.
- Black Oxide is a cost-effective treatment that provides mild corrosion resistance and reduces reflection. While it doesn’t significantly increase hardness, it does offer some protection against corrosion and improves lubricant adhesion, which can be beneficial in specific applications.
Multiple Coating Options, One Trusted Provider
When selecting a protective coating, it’s important to consider the specific application requirements, including the operating environment, load conditions, and required lifespan of the high load ball screw. The right coating can significantly enhance performance, reduce maintenance requirements, and prevent premature failure. Talk to one of our experienced engineers and learn about your options.