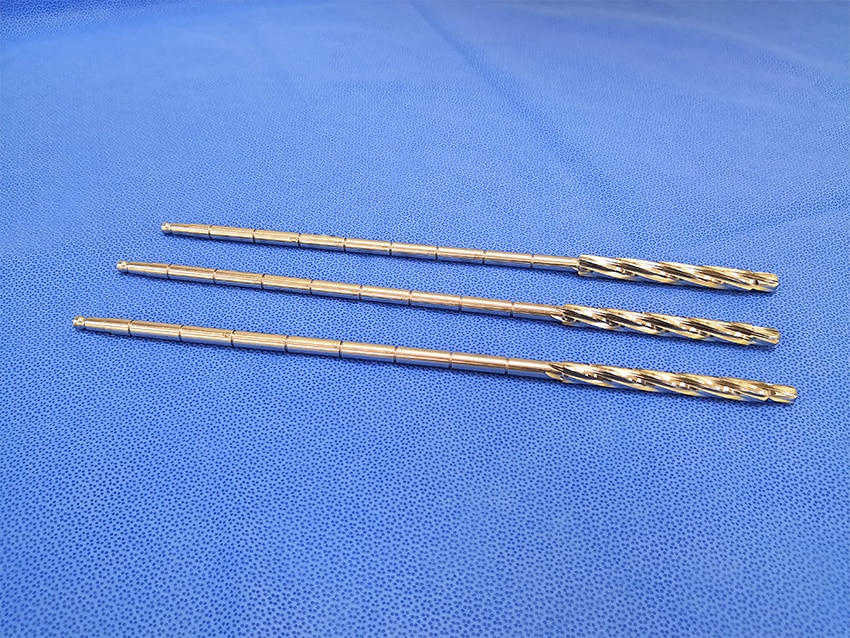
Introduction
The application of chromium composite coating greatly improved the performance of stainless steel orthopedic instruments, particularly bone cutting devices. Novel coating prevented bone cutting drills from becoming dull and from degrading between consecutive cuts. Uncoated drills, made of precipitation hardening (455 PH) stainless steel, began to decrease in their performance after the initial cut. In contrast, coated bits performed consistently throughout the cutting of 11.25 inches of bovine bone.
Procedures
ME-92 Operations, Inc., Providence, RI, tested Zimmer® 455 PH drill bits (Catalog #6260-03-01, 3.2mm) with and without coating. ME-92 Operations, Inc. also funded the project and applied a 1-2 micron thick chromium composition coating (ME-92®). The bits cut fifteen, 3/4-inch deep holes into bovine bone cortex from Arena & Sons, Hopkinton, MA. Throughout the testing, they continuously recorded bit depths, cutting rates, and drilling loads, and downloaded the data onto a spreadsheet for analysis. Rhode Island Hospital (RIH), Orthopedic Research Laboratories conducted the mechanical testing.
Two orthopedic surgeons from Rhode Island Hospital established the constant drilling force for the testing protocol. Each surgeon used a handheld Synthes® Small Air Drill (Catalog #511.11) to drill into bone, which was attached to a load cell. From this investigation, they selected a constant dead load of 86 Newtons (8.7 lb.) for the tests. They fixtured the drills in a modified Sears® drill press operating at 735 rpm.
Materials Science Associates (MSA) inspected and photographed the cutting bits at 35x and 150x magnifications before and after coating and at the end of testing. MSA used a JEOL T300 scanning electron microscope (SEM) equipped with a TN 5500 energy dispersive spectroscopic system (EDS) for evaluation and documentation.
Results and Discussion
The drilling behavior of both coated and bare bits was biphasic. There was an initial constant cutting rate, until a break point was reached. The break point was generally indicated by smoking at the cutting site. After this, the bits cut at a second constant, but slower rate. The break point occurred at approximately the same depth of cut for both types of drill. New drill designs, that extend this break point, may reduce heating damage to bones during operations.
Graph Overview
Coated 455 PH bits had a better overall cutting rate than uncoated bits. Coating the bits resulted in an improvement of 11.3% over bare stainless steel. These results are presented on Graph 1.
The cutting rate of the uncoated 455 PH bits decreased as the testing proceeded. The application of the coating prevented this degradation and provided more consistent cutting performance. Bare, uncoated bits lost 29% of their initial cutting performance by the end of 15 cuts. A graph indicating the change in cutting rate for the bare and coated drill bits is presented as Graph 2.
Plots of the regression rates for each of the 455 PH drills, also demonstrate that the coating improved cutting consistency. The average cutting performance of the uncoated bits decreased after the initial cut, as indicated by the downward trend in Graph 3. The average performance of coated bits was consistent throughout the 15 cuts as indicated by the level lines on Graph 4.
Scanning electron microscopy confirmed that the coating was still present on the cutting surfaces after the testing. Wear and material loss were observed on the cutting edges of the uncoated 455 PH bits. The appearance of wear on the uncoated bits indicates that some metallic wear debris may have been introduced to the bone drilling sites. No wear was observed on the cutting surfaces of coated bits.
Conclusion on Orthopedic Instruments
The laboratory testing indicated several advantages of coating orthopedic instruments with Armoloy’s biocompatible thin dense chrome:
- Coated drill bits cut bone faster and more consistently than bare bits.
- Coated 455 PH cutters remained sharp during all tests.
- Bare bits had a 29% lower cutting rate by the end of 15 cuts.
- No coating loss was observed at the end of testing.
- Coating the bit, reduced wear, material loss and debris generation.
It was also noticed that the cutting behavior of both coated and bare bits were biphasic.
Graph 1. Coating the drill bits with ME-92® improved the average cutting rate by 11.3%
Graph 2.Total change in cutting rate over 15 cuts into bone from orthopedic instruments
Graph 3. Uncoated cutting bits show a steady loss of performance (29%), while drilling 15 holes in bone
Graph 4. ME-92® coated bits afforded consistent performance throughout the cutting tests.