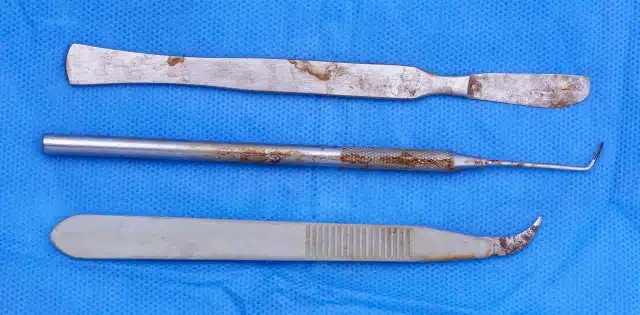
Stainless steel (SS) is a very versatile component material in a variety of industries for its corrosion resistance, strength, and durability. In the medical industry, the biocompatibility of stainless steel—and the fact that it is relatively inexpensive—makes it a strong choice for multiple applications, including surgical instruments and medical devices.
In this post, we’ll discuss the primary benefits of stainless steel, the main types of stainless steel used for medical applications, and discuss some of the benefits of using the ME-92® chromium composition coating technology over bare stainless steels.
The benefits of stainless steel for medical applications
Whether designing applications for food processing to pharmaceutical packaging, multiple industries, including medical, recognize the myriad benefits of stainless steel (SS), including:
- Corrosion resistance. Stainless steel has a high resistance to corrosion and is able to withstand harsh environments.
- Strength and durability. SS is able to withstand high loads and is resistant to wear and tear.
- Low maintenance. Stainless steel is resistant to staining and easy to clean.
- Hygienic. SS is a biocompatible material that does not harbor bacteria, making it suitable for use in any industry where hygiene and cleanliness are crucial.
- Recyclable. 100% recyclable, stainless steel can also be recycled indefinitely without losing its strength or quality.
- Aesthetic appeal. SS has a sleek and modern appearance, making it a popular choice for use in architecture and design.
- Versatility. Stainless steel is a versatile material for a wide range of applications, including construction, automotive, aerospace, medical, food and beverage, and chemical processing.
- Long service life. The long lifespan of SS makes it a cost-effective material over the long term.
- Low thermal expansion. Stainless steel has a low thermal expansion coefficient, making it suitable for use in high-temperature environments.
- Resistant to fire. SS is resistant to fire and does not release toxic fumes when exposed to high temperatures, making it a safe choice for use in buildings and other structures.
Top categories of stainless steel for medical applications
Choosing a type of stainless steel for a particular medical application will depend on a variety of factors, including the specific requirements of the application, the intended use, and the desired properties of the material. Some of the most common types of stainless steel used in the medical industry include:
Austenitic Stainless Steel
One of the five classes of stainless steel by crystalline structure, austenitic stainless steel is the most steel for use in the medical industry due to its high corrosion resistance and good formability. Containing high concentrations of nickel and chromium, austenitic stainless steels most commonly used in the medical industry are Type 316 and Type 304.
Ferritic Stainless Steel
Less corrosion-resistant than austenitic stainless steel, the ferritic type still has good formability and is often used in the medical industry for non-implantable medical devices. Containing very low levels of carbon, high amounts of chromium, and little or no nickel, ferritic stainless steels used in the medical industry typically include Type 430 and Type 434.
Martensitic Stainless Steel
This type of stainless steel contains added carbon and a body-centered tetragonal crystalline structure. It is harder and stronger than austenitic stainless steel, making it suitable for use in surgical instruments and other applications where high strength is required. Examples of martensitic stainless steels used in the medical industry include Type 410 and Type 420.
Precipitation Hardening (PH) Stainless Steel
Falling in between martensitic and austenitic types, precipitation hardening types are magnetic and have higher corrosion resistance than the martensitic types. This type of stainless steel is often used for orthopedic instruments.
Duplex stainless steel
This type of stainless steel has a combination of austenitic and ferritic microstructures, which gives it a combination of corrosion resistance and strength. Examples of duplex stainless steels used in the medical industry include Type 2205 and Type 2507.
Benefits of using biocompatible chromium coatings over bare stainless steel
Researchers have used various modifications to change the surface properties of stainless steels. They have sought coatings to reduce friction, lower wear rates, reduce galling and scoring, and provide easy release, easy cleaning, and nonstick properties.
For medical applications, it is also necessary that coatings be nonreactive to the body—a crucial feature of ME-92® biochrome coatings. Applied over bare stainless steels, ME-92® has many properties that make it especially suitable for medical applications, including:
High resistance to corrosion
ME-92® technology automatically activates, cleans, and removes superficial oxides before depositing a uniform, hard (Rc 80+), and corrosion resistant micro-coating. Other coating technologies that do not remove the surface oxide film before coating deposition may come off during service or testing. Testing demonstrated that ME-92® provides outstanding corrosion protection, even on type 440C after numerous exposures to saline solution and autoclave sterilization. Further research proved that the ME-92® technology resists corrosion during repeated exposures to bleach disinfectant, boiling, and room temperature deionized water.
Elimination of chemical passivation
The additional time and associated expenses of chemical passivation before coating can also be eliminated by the ME-92® technology without adversely affecting coating adhesion or final corrosion resistance.
Nonstick and easy release
ME-92® has a relatively nonwetting surface, which means that water and many other fluids bead on it, similar to rain beading up on a freshly waxed surface. The degree to which fluids wet or bead on a surface is measured as surface tension. The total surface tension of ME-92® has been measured in the range of 21.6 to 26.1 ergs/cm2, while bare 304 SS had a value of 39.3ergs/cm2. This low surface energy is believed to result from a special surface affinity possessed by the coating.
Both mono-polar and bi-polar electro-surgical devices have benefited from the application of ME-92. Furthermore, instruments with VIE-92 coating may undergo scrubbing without loss of coating or functional performance.
Increased wear resistance
ME-92® is a metallic coating with special ceramic-like surface properties. The metallic portion of the coating chemically bonds with the base metal and then forms a ceramic-like outer surface layer, which is self-replenishing if scratched. This gives the coating highly desirable friction, nonstick, and release characteristics in conjunction with superior wear and non-galling properties. Standardized independent testing demonstrates that ME-92® substantially reduces the wear and galling of stainless steels.
Also of note—ME-92® performs excellently against itself. In many applications, it is best to enhance all mating surfaces with ME-92 to realize the maximum benefits of the coating.
Friction reduction
ME-92® reduces the friction of stainless steels. In certain applications lubricity similar to Polytetrafluoroethylene (PTFE) may be obtainable. This coating has a combination of low friction and low wear rates. This combination of properties is unique and useful.
High maximum operating temperature
The metallic and ceramic-like natures of ME-92® give it an extended maximum operating temperature. Exceptional mechanical properties are effective up to 1000°F (540°C). This makes it well-suited to high-temperature applications. Even at temperatures above this, ME-92® remains integrated with the base metal’s surface. It also helps prevent the formation of heat oxides and scale, which are known to contaminate medical devices during manufacture.
Biocompatibility
The high wear resistance of ME-92® results in a substantially lower material loss compared to bare stainless steels. The coating also provides an effective barrier from the potentially carcinogenic nickel component of stainless alloys. European countries have regulated the use of nickel-bearing alloys, in order to reduce the occurrence of allergic skin sensitization.
ME-92® has satisfied all the biocompatibility requirements for the current ISO 10993 standard, plus the additional hemolysis, pyrogenicity, mutagenicity, polar and non-polar sensitization tests necessary to pass the Tripartite Guidelines Testing for Biocompatibility.
Go ahead, ask us anything.
As a metallurgical consulting, research, and testing firm, ME-92 is here to help OEMs and medical engineers, design and manufacturing engineers reach beyond the capabilities of bare stainless steels.