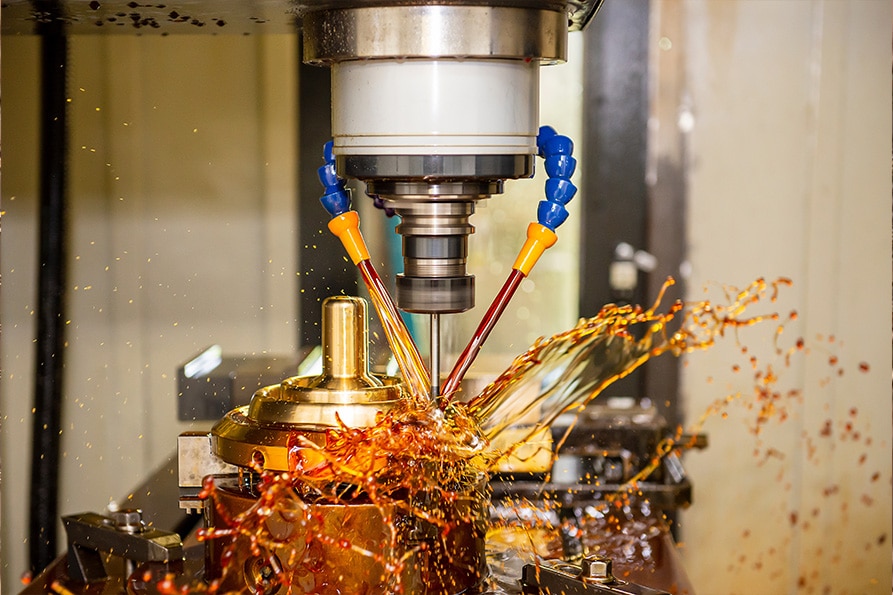
Industrial lubricants are essential for the optimal operation of machinery in manufacturing and industrial processes. Understanding the different types and their applications can significantly enhance machine performance and longevity.
In this guide on industrial lubricants, we’ll discuss:
- Types of Industrial Lubricants
- Enhancing Lubrication with Coatings
- Industrial Lubricants for Bearings
- How TDC’s Structure Benefits Bearing Lubrication
There are four main types of industrial lubricants:
Greases
Greases are made from oil, such as mineral oil, to which thickening soaps and other substances are added to produce the desired tackiness and other properties. This form of industrial lubricant is particularly valuable in applications where a durable and long-lasting lubricant is required. Greases excel in environments where parts are exposed to harsh conditions like dust, dirt, or water because they can remain in place without being easily displaced. Common applications for industrial greases include bearings, gears, and linkages in machinery.
Common industrial grease for lubricating various manufacturing applications.
Oils
Oils can also be effective industrial lubricants in their natural, non-thickened state. Lubricant makers blend additives into oils to prevent oxidation, inhibit corrosion, and enhance performance under varying temperatures and pressures. Industrial oils are widely used in systems requiring fluid movement, such as hydraulic systems, engines, and compressors. Their low viscosity allows them to flow easily between moving parts, reducing friction and wear while also providing cooling properties.
Industrial oil lubricant housed in an automated lubrication canister.
Dry Lubricants
Dry lubricants, also called dry film lubricants, are materials like graphite, molybdenum, and silicon that are mixed with binders and applied to surfaces. They are most useful when extreme temperatures or pressures make liquid lubricants ineffective. These lubricants create a slippery layer on surfaces, reducing friction without the need for liquid. They are ideal for applications such as high-temperature ovens, aerospace mechanisms, and environments where liquid lubricants would evaporate or degrade rapidly.
Graphite powder lubricant
Penetrating Lubricants
Penetrating lubricants are low-viscosity oils that are more for removing rust than creating smooth-gliding surfaces. These lubricants seep into small crevices, loosening rust and freeing stuck components. They have common usage in maintenance and repair settings to free bolts, nuts, and other parts that corrode over time. While they provide temporary lubrication, their primary function is to facilitate disassembly and initial movement.
Benefits of Chromium Coatings in Industrial Lubrication
The benefits of these industrial lubricants—especially the first three—can be magnified by coating the surfaces they protect with chromium.
An Example of Synergy Between a Lubricant and a Chromium Coating
A Common Synergy for Bearings
Roller bearings provide a helpful illustration of how the combination of adequate lubrication and chromium coatings is highly effective at improving device performance. The ability of this “dynamic duo” to prevent corrosion is particularly valuable. Chromium coatings like Armoloy Thin Dense Chrome (TDC) offer exceptional protection for system components by providing a hard, dense layer that resists wear and corrosion. This synergy extends the lifespan of bearings and other critical parts, enhancing overall machinery reliability and performance.
Equipment owners and users observe multiple benefits from TDC, including:
- Reduced corrosion
- Decreased wear
- Extended service periods
- Energy savings
- More efficient use of materials
All of these factors can, of course, reduce operating costs, thereby increasing net revenue and profitability. And because the coating application process temperature is below 176°F (80°C), there is no structural change to the material or the dimensional stability of the coated roller bearings and linear components.
Roller bearing assembly coated with Armoloy. Armoloy coatings are effective are thin deposits, preserving tight tolerances all while eliminating post-plating processes.
Preventative Measure as a Benefit
Another benefit of chromium coatings in bearing components is improving emergency run properties. If a machine’s lubrication system stops working, for example, the device can continue running under partial load for a short time. Operators will have to shut the machine down promptly in this scenario, but an intentional shutdown versus the “seizing up” of components helps minimize or prevent costly secondary damage.
Regarding corrosion reduction specifically, coating a surface with TDC protects it against water, steam, caustic solutions, and even acid to some degree. Remarkable results were noted in a salt spray test carried out according to ASTM B 117 that largely conformed to DIN 50 021.
Within 24 hours, an uncoated standard bearing developed corrosion over 95% of its surface. Bearings made of corrosion-resistant steel fared better, showing deterioration on 25% of their surface. But the clear “winner” was TDC-coated bearings. They developed corrosion on just 1% of their surface area.
The Bottom Line on Bearings and Industrial Lubricants
Whether a particular system or component can accommodate lubrication and chromium coatings or only chromium coatings, the addition of that protective layer can significantly improve performance and protection. If you have not used TDC or related coatings in the past, the proven benefits certainly justify the time it takes to learn more and potentially move forward with a protection strategy.
Lubrication is one of the most critical factors in the performance of systems with metal surfaces that operate near or in contact with one another. Consequently, it is vital for everyone, from machine operators to business decision-makers, to understand the requirements to minimize friction and maximize the effectiveness and lifespan of mechanical systems.
Full-Film Lubrication and Boundary Lubrication
It is common for machine manufacturers to design machines such that medium- and high-speed rotating components never contact one another. This scenario is called full-film lubrication or elastohydrodynamic lubrication (EHL). When wear occurs in this type of assembly, a company can safely assume the cause is lubricant contamination, lubrication system failure, poor design, or improper operation.
Boundary Lubrication
Boundary lubrication is where an oil film is present, but it cannot support the applied loads. As a result, there is a degree of contact between metal surfaces when the system surpasses critical operating stress. This stress can be as low as a few MPa, with some materials. Systems that have full-film lubrication can experience brief instances of boundary lubrication. That tends to happen as an operator starts the system or shuts it down.
Mixed Film Lubrication
A third lubrication scenario is called mixed film. Systems that use this approach can support higher loads but experience adhesive wear under certain conditions. Companies and their service providers must understand the characteristics of these three lubrication scenarios when addressing system problems related to lubrication.
How TDC’s Structure Benefits Lubrication and Bearings in Mechanical Systems
Armoloy Nodular Thin Dense Chrome (NTDC), which can be applied to lubrication and bearings, and other machine components, has a nodular structure. A nodular surface structure is beneficial in multiple ways. First, the spaces between the nodes serve as a “reservoir” for lubricant. The gaps retain material that might otherwise be lost as the system runs, making lubricant available for a longer period than on surfaces that are not nodular.
The second benefit of this structure has to do with wear debris. As metal wears, the castoff material can accumulate throughout the system, including in the contact zone. This accumulation adversely affects the system’s performance. The space between nodes tends to “capture” wear material, keeping it away from the contact zone longer.
In addition, a chromium coating can reduce the operating temperature of bearing systems.
Heat reduction is beneficial in several ways. For example, cooler temperatures help keep oil viscous longer, and viscous oil provides more effective lubrication. They also reduce oil oxidation. As a result, companies can go for longer periods before servicing their machines. Plus, less friction means more efficient operations and less energy consumption.
All of these factors contribute to lower operating costs and higher profitability.
Research on Structured Surfaces and Load-Carrying Film Formation
As noted above, boundary lubrication allows surfaces to contact one another. Consequently, spending less time in that state benefits mechanical systems.
Studies on using lasers to create structured surfaces point to an interesting potential added benefit of TDC’s nodular surface. The results seem to indicate that a structured surface promotes faster formation of a load-carrying film. Researchers are working to confirm that hypothesis. But if true, we will have a deeper understanding of how chromium coatings protect metal surfaces.
For example, if a structured surface helps a system achieve full-film lubrication 25% faster than a non-structured surface, one can reasonably assume that it reduces wear by a similar amount.
This type of discovery is one of the reasons Armoloy continually works to advance its chromium coatings. Rather than simply taking pride in the tremendous performance improvements coatings and lubricants can produce today, we are accepting the challenge to deliver even better results down the road.
Share on LinkedIn Share on Facebook
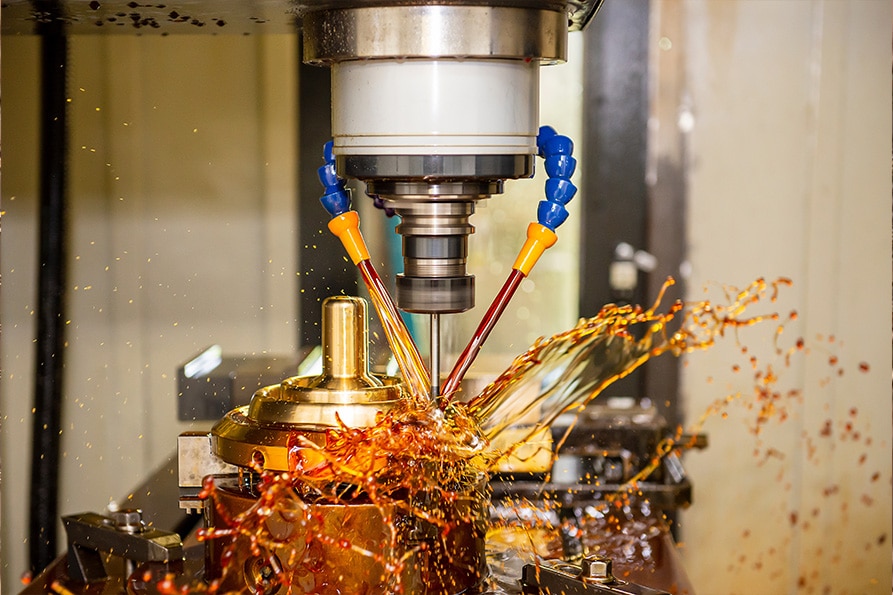