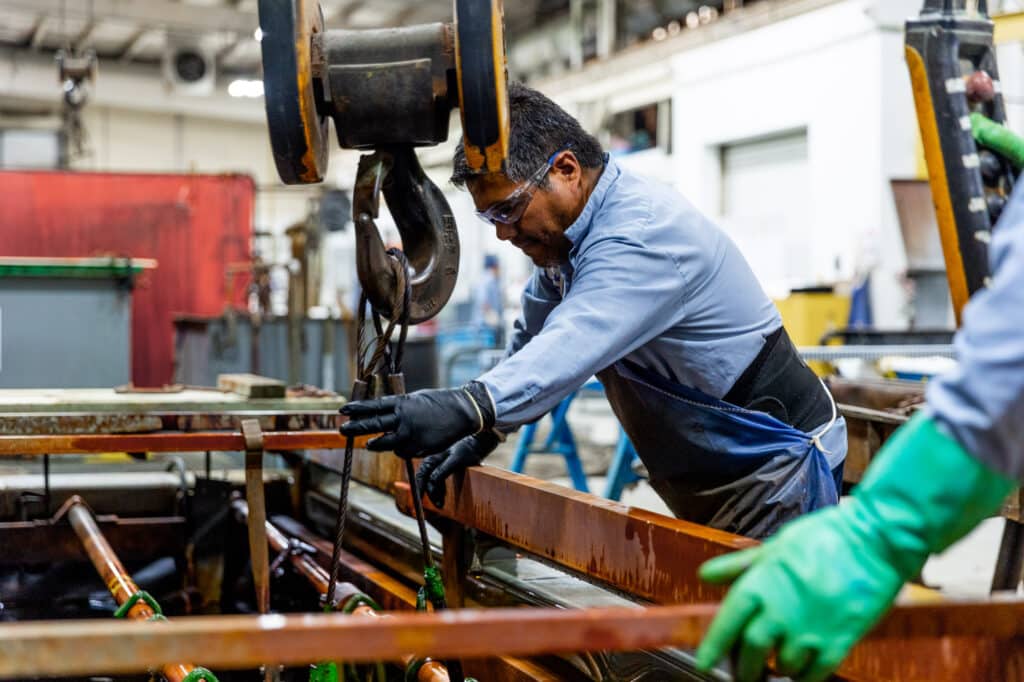
What is Electroplating?
Electroplating is a process that involves depositing a metal or alloy onto a substrate by passing an electric current through an electrolytic solution where the workpiece serves as a cathode. The electroplating method involves two electrodes: the anode, made of the depositing metal, and the cathode, the workpiece. When you apply the electric current, metal cations dissolve from the anode into the solution and deposit onto the cathode, creating a thin metal layer on the workpiece. In some processes, the metal to be deposited exists as metallic ions dissolved directly in the bath. For those cases, manufacturers use anodes made from non-reactive metals like lead or titanium.
In this guide on electroplating, we’ll discuss:
- How Electroless Plating Differs
- Types of Electroplating
- Electroplating in Applications and Industries
- The Electroplating Process
- Environmental Impact of Electroplating
The purposes of electroplating are varied and include enhancing the appearance, protection against corrosion and wear, and providing special surface properties. Owing to its ability to improve both functional and decorative aspects of objects, this process is wide utilization across various industries, including aerospace, nuclear, electronics, and jewelry.
How Does Electroless Plating Differ?
Electroless plating, by contrast, does not require an electric current. Instead, it uses a chemical reduction process to deposit metal onto the substrate. This process involves a plating solution that contains metal ions, a reducing agent, and other chemicals that initiate and regulate the plating reaction. Electroless plating is particularly valued for its ability to produce a uniform metal layer, even on complex shapes and non-conductive surfaces, which is a limitation in some electroplating processes due to uneven current density effects. Examples of materials used in electroless plating include nickel, gold, and palladium.
Basic illustration comparing the electrolytic plating process (electroplating) to the electroless plating process
The main differences between these two plating techniques stem from their respective mechanisms and applications. Electroplating allows for greater control over the thickness and properties of the metal coating by adjusting parameters such as current density, agitation and plating time. It is typically used where specific conductivity or corrosion resistance characteristics are needed. Electroless plating, however, is chosen for applications requiring uniform coverage over complex geometries and excellent corrosion and wear resistance without the need for external power.
Types of Electroplating
Electroplating encompasses various methods and materials, each offering specific benefits depending on the application requirements. Here’s a summary of the most common types of electroplating and their specific uses and benefits:
Zinc Plating
Zinc plating provides excellent corrosion resistance, making it ideal for automotive and hardware applications, as well as an effective undercoat for paints. It is relatively cost-effective and offers good protection for steel parts against rust.
Zinc plating is used on fasteners to improve the lubricity and hardness of the threads
Gold Electroplating
Often used for decorative purposes, gold plating adds aesthetic appeal and significant corrosion resistance. It’s also valued in electronic applications for its excellent conductivity and resistance to oxidation. There are, however, both electrolytic and electroless gold plating processes.
Printed circuit board with gold plating
Silver Electroplating
Similar to gold, silver plating is used for both its conductivity and appearance. Manufacturers commonly apply silver plating to electrical components, jewelry, and cutlery, particularly valuing it for settings requiring high electrical and thermal conductivity.
Copper Plating
Engineers often use copper as a base layer to improve the adhesion of other metals. Copper plating is essential in the electronics industry because it significantly enhances the electrical conductivity of components. Copper plating is also in use for decorative purposes.
Image shows a copper plating bath for printed circuit boards
Nickel Electroplating
Known for its hardness and durability, nickel plating improves wear and corrosion resistance and adds a reflective and shiny finish. Nickel has common uses in the chemical, petroleum, and food processing industries.
Chromium Electroplating
Often referred to as chrome plating, it provides an extremely hard surface with high wear resistance. Chromium is in use across various industries due to its functional and protective properties.
Bearings plated in Armoloy nodular thin dense chrome
Choose each type of electroplating based on the desired properties of the final product, such as appearance, resistance to metal failure modes, or enhanced electrical conductivity. The choice of plating material greatly depends on the specific application requirements and the characteristics that are most valued for the end-use of the plated component.
Electroplating in Applications and Industries
Numerous industries widely utilize electroplating for its enhanced corrosion resistance, electrical conductivity, wear resistance, and aesthetic appeal. Here is a detailed summary of the primary applications and industries where electroplating is essential:
Aerospace Industry
- Corrosion Resistance and Durability: Components in aerospace applications are subjected to extreme environmental conditions. Use electrolytic plating, such as chromium and zinc-nickel plating, to protect vital parts against corrosion and wear, thereby enhancing their lifespan.
- Lightweight Properties: Plating lightweight materials such as aluminum maintains structural integrity and reduces overall aircraft weight, a critical factor in aerospace design.
Electronics
- Electrical Conductivity: Gold and silver plating are prevalent in electronic components like connectors and circuit boards due to their excellent electrical conductivity and resistance to corrosion.
- Thermal Management: Certain plating processes, like silver, can also help with better heat dissipation in high-performance electronic components.
Medical Devices
- Biocompatibility and Sterility: Use biocompatible thin dense chrome and nickel coatings in medical implants and surgical instruments to prevent corrosion, facilitate sterilization processes, and reduce the risk of allergic reactions and infections.
- Enhanced Functionalities: For tools and devices that require precise functionality, coatings can provide necessary surface properties such as smoothness and reduced friction.
Image of surgical hip replacement plated with biocompatible thin dense chrome
Oil and Gas
- Protection in Harsh Environments: Equipment used in oil and gas extraction and processing can be exposed to highly corrosive environments. Electrolytic nickel and chrome plating are vital for protecting valves, pipelines, and other machinery against corrosion and wear.
Electroplating of Armoloy performed on core sub for its anti-galling properties, wear and corrosion resistance.
Nuclear Energy
- Corrosion Resistance and Safety: In the nuclear industry, electroplating protects components from radiation and thermal degradation, ensuring long-term safe performance.
Nuclear components, like the nuclear fuel rod element shown above, use electroplating processes to safeguard components from potential critical failures.
Consumer Goods
- Decorative Applications: Electroplating adds aesthetic value to everyday items such as jewelry, watches, and other decorative items, enhancing appearance and resistance to tarnishing.
The Electroplating Process
The process of electroplating involves several key components and steps that ensure the successful deposition of a chosen material onto a substrate. Here, we provide an example with an overview of the electrolytic silver plating process:
Equipment and Components
- Cathodes and Anodes: In the setup for silver plating, the item to be plated serves as the cathode, while the anode is typically made of pure silver. This arrangement facilitates the migration of silver ions from the anode to the cathode under the influence of an electric current.
- Plating Solutions: The electrolyte solution used for silver plating often contains a silver salt dissolved in water. Non-cyanide solutions are increasingly popular due to environmental concerns. These solutions ensure the transfer of silver ions necessary for the coating process.
- Power Supply: A direct current power source is crucial as it drives the electrochemical reaction in the plating bath. Carefully control the voltage and current settings to ensure a consistent quality of plating.
- Rack and Barrel Systems: For industrial applications, silver plating is often done using either rack plating or barrel plating setups. Rack plating is suitable for larger or more delicate items, ensuring an even coat without damage. Use barrel plating for smaller, more durable items, allowing for bulk plating, which is more cost-effective.
Process Overview
The process begins with the preparation of the substrate, which includes cleaning and sometimes a base layer deposition if necessary to improve the adhesion of silver. The next step is to immerse the substrate into the plating solution where it acts as the cathode. The anode, made of silver, dissolves under the application of an electric current, and silver ions deposit onto the cathode, forming a thin, even layer of silver.
Illustration of standard electroplating circuit
Controlling temperature, agitation, and anode-cathode distance is essential for achieving the desired silver layer thickness and quality. Adjustments to these parameters can help manage the rate of deposition and the properties of the silver layer, such as its brightness and adherence. This controlled process yields a durable, conductive, and attractive silver layer, valued in electronics and decorative industrial applications.
Environmental Impact of Electroplating
Electroplating processes can have environmental impacts from using hazardous chemicals, which leads to air and water pollution if mismanaged. Common pollutants from electroplating operations include heavy metals such as cadmium and lead, as well as cyanides, all known for their toxicity. However, responsible plating organizations can conduct electroplating safely when they manage it adequately. Reputable plating companies use strict protocols and advanced systems to reduce environmental contamination and ensure safe chemical handling.
Regulations and Compliance
In the United States, various EPA guidelines regulate electroplating facilities to minimize environmental impact and ensure worker safety. These regulations include the National Emission Standards for Hazardous Air Pollutants (NESHAP) for plating and polishing operations, which mandate controls on air emissions and prescribe specific management practices to reduce exposure to hazardous air pollutants.
The EPA’s Electroplating Effluent Guidelines also play a critical role, setting standards for wastewater discharges to protect water quality. These guidelines are part of the broader framework under the Clean Water Act, aiming to reduce direct and indirect pollutant discharges into water bodies.
Recordkeeping and Reporting
Compliance with these regulations requires meticulous recordkeeping and reporting of emissions, waste management practices, and any incidences of non-compliance. Facilities must maintain detailed records of all operations, emissions, and waste treatment processes. They must also comply with regular reporting requirements to demonstrate adherence to environmental standards.
Positive Outlook for Electroplating
Despite its complexities, advancements in technology and stricter regulatory frameworks are paving the way for greener and safer electroplating practices. Adopting non-toxic plating alternatives and improved waste management systems reduces the environmental footprint of this essential industrial process. These improvements will enhance electroplating sustainability, ensuring it remains crucial in manufacturing and aligns with global environmental standards.
Work with a Reputable Plating Partner
Armoloy provides both electrolytic and electroless surface solutions that tackle metal challenges while exceeding strict industry standards and regulations. Chat with an applications engineer today for more information on our start-to-finish surface solutions for your next project.
Share on LinkedIn Share on Facebook