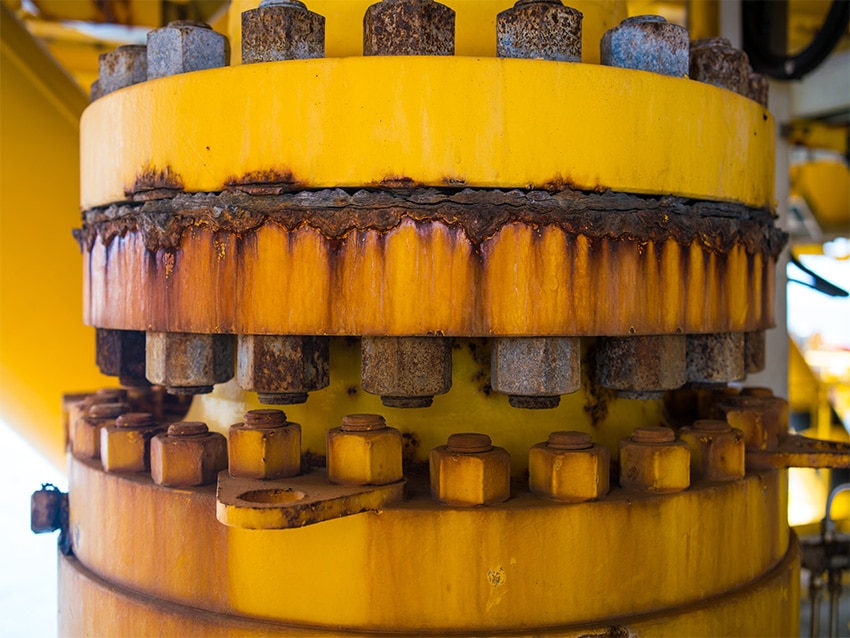
Understanding what causes metal to break down is crucial for anyone who designs, manufactures, or depends on metal parts, tools, or equipment. Two of the most common culprits behind metal failure are erosion and corrosion. Though their names sound similar and their effects can be equally destructive, erosion and corrosion are fundamentally different processes
Erosion removes material from a surface through physical forces like fast-moving flows or abrasive particles, while corrosion is a chemical reaction that weakens metal through processes like oxidation. Diagnosing whether the damage is caused by erosion, corrosion, or both is the first step to finding the right solution.
At Armoloy, we specialize in protecting metal surfaces from both erosive and corrosive forces. In this article, we’ll explain the key differences between erosion and corrosion, explore real-world examples, and show how Armoloy’s advanced surface treatments can safeguard your critical components.
What is Metal Erosion? (Definition, Causes, and Examples)
Erosion is a physical process that removes material from a surface through mechanical forces. Unlike corrosion, a chemical reaction, erosive wear happens when external forces like fast-moving flows, abrasive particles, or cavitation wear away the surface. Over time, this can thin metal, weaken structures, and cause equipment to fail.
Key Causes of Erosion
- High-Velocity Flows: Rapidly moving liquids or gases can create significant wear on metal surfaces, especially in pipelines and hydraulic systems.
- Abrasive Particles: Solid particles suspended in a liquid or gas flow can scrape against metal surfaces, causing material loss over time.
- Cavitation: The formation and collapse of vapor bubbles in liquids can generate intense localized forces that erode metal surfaces, particularly in pumps, turbines, and propellers.
- Environmental Conditions: Weather-related factors, such as wind, water, temperature fluctuations, and other natural forces, can erode exposed metal surfaces over time, particularly in outdoor applications like bridges and construction equipment.
Examples of Erosion in Metals
- Pipeline Erosion: Solid particles or turbulent flow within pipelines can wear down internal surfaces, eventually leading to leaks or bursts.
- Turbine and Hydraulic Systems: Hydraulic systems and turbine blades in high-velocity environments, such as those found in jet engines or industrial processes, experience gradual erosion that reduces efficiency and operational lifespan.
- The Hoover Dam Spillways: During heavy floods, the spillways at the Hoover Dam experienced severe erosion caused by the intense force of water flowing through them. The metal reinforcements suffered damage as the water displaced particles, requiring extensive repairs.
At Armoloy, our surface treatments significantly improve resistance to erosive forces by enhancing the hardness and smoothness of metal surfaces. By reducing friction and wear, Armoloy coatings extend the lifespan of critical components in environments prone to erosion.
What is Metal Corrosion? (Definition, Causes, and Examples)
Corrosion is a chemical process that weakens metal over time by reacting with elements in the environment. Most commonly, corrosion occurs when metals interact with oxygen, moisture, or chemicals, forming substances like rust. If not addressed, corrosion can damage the structure of metal components and lead to expensive failures
Key Causes of Corrosion
- Oxidation: When metals are exposed to oxygen over time, they form oxides that degrade their surface. For example, iron forms rust (iron oxide) when it reacts with oxygen and water.
- Chemical Exposure: Acids, salts, and industrial chemicals can accelerate the corrosion process, particularly in harsh environments like factories or chemical plants.
- Environmental Conditions: High humidity, temperature fluctuations, and pollutants in the air can exacerbate corrosion in untreated metals.
Examples of Corrosion in Metals
- Pipelines: Over time, internal and external corrosion in pipelines can lead to leaks, contamination, or complete failure.
- Industrial Equipment: Machinery exposed to harsh chemicals or high humidity often suffers from corrosion, reducing its operational lifespan.
- Marine Applications: Ships, docks, and offshore platforms are highly susceptible to corrosion due to constant exposure to saltwater.
- The Statue of Liberty: Originally copper-colored, the Statue of Liberty underwent oxidation, forming a green patina (copper oxide). While this corrosion has become iconic, it demonstrates the chemical changes metals undergo when exposed to environmental conditions.
Corrosion often involves an electrochemical reaction where metal serves as an anode in the presence of an electrolyte, facilitating the loss of material.The figure below illustrates a basic electrochemical cell, displaying the components required for corrosion. This visual representation helps explain how metals break down in such reactions.
Basic electrochemical cell illustration displaying components necessary for corrosion to occur
At Armoloy, we offer advanced surface treatments that shield metals from corrosive agents. Our proprietary coatings act as a barrier, protecting metal surfaces from the chemical reactions that lead to corrosion, ensuring greater durability and reliability for your equipment.
Corrosion vs. Erosion: Key Differences
Understanding the differences between corrosion and erosion is critical for diagnosing the root cause of metal failure and implementing effective solutions. While both processes degrade materials, they do so in fundamentally different ways. Here’s a streamlined comparison:
Comparison Table: What is the Difference Between Erosion and Corrosion?
Corrosion | Erosion |
A chemical reaction degrades material | Physical forces remove surface material |
Caused by oxidation, acids, or chemicals | Caused by wind, water, gravity, or cavitation |
Weakens structural integrity through chemical decay | Alters shape or thickness through material loss |
Detected using corrosion coupons, ultrasonic testing, or radiography | Detected using surface profiling, 3D imaging, or flow analysis |
Prevented with Armoloy’s anti-corrosion treatments and protective coatings | Prevented with Armoloy’s wear-resistant surface treatments and optimized flow design |
If left unchecked, corrosion and erosion can severely compromise the functionality and safety of metal components. Understanding their causes and effects is essential for effective prevention and extending the lifespan of critical systems in industries ranging from manufacturing to transportation.
Examples of Corrosion and Erosion in Pipes and Other Metals
Corrosion and erosion directly impact the performance and safety of critical metal systems across industries. Due to their exposure to challenging environments, pipelines, machinery, and structural components are particularly vulnerable. Here, we’ll explore specific real-world examples to demonstrate the effects of these processes.
Corrosion in Pipes and Other Metals
- Corroding Underground Pipelines: Pipelines buried underground are often exposed to moisture, varying pH levels in soil, and stray electrical currents, which can lead to external corrosion. Over time, this can weaken the pipe walls, increasing the risk of leaks or catastrophic failures.
- Marine Corrosion on Ship Hulls: Saltwater is a powerful accelerant of corrosion. Ship hulls from steel frequently develop rust and pitting corrosion, necessitating regular maintenance to prevent long-term damage.
Industries Affected: Oil and gas pipelines, marine transportation, and chemical processing facilities are highly susceptible to corrosion caused by aggressive agents such as salt, acids, or industrial chemicals.
Erosion in Pipes and Other Metals
- Erosion in Power Plant Piping: High-velocity steam or water flows within power plant piping can erode the internal surfaces, leading to thinning and eventual failure. This type of erosion can significantly reduce operational efficiency and require costly shutdowns for repairs.
- Turbine Blade Erosion in Hydroelectric Plants: Turbine blades are frequently subjected to high-speed water flows containing abrasive particles. Over time, this causes material loss that reduces efficiency and increases maintenance requirements.
Industries Affected: Hydroelectric power, jet propulsion, and industrial manufacturing rely heavily on components that face erosive forces in high-velocity environments.
Understanding these real-world applications makes it easier to grasp the critical need for effectively diagnosing and addressing corrosion and erosion. Proper material selection, system design, and surface treatments tailored to the operating environment can significantly extend the life of these metal systems.
How to Diagnose Erosive vs. Corrosive Metal Failure
Determining whether metal damage is caused by erosion, corrosion, or a combination of both is essential for choosing the proper prevention and repair strategies. By understanding the signs of each type of damage and using diagnostic tools, you can identify the cause and take steps to protect your equipment.
Signs of Metal Erosion
Erosion removes material from a surface through physical forces, causing visible and structural changes. The type of damage depends on the force involved:
- Gas Flow Erosion: High-speed gas flow can create broad, shallow indentations.
- Liquid Impact Erosion occurs when streams of liquid hit a surface. Depending on the angle and velocity of the impact, the liquid may form grooves or holes.
- Material Characteristics: While erosion changes a material’s shape and thickness, the affected areas often retain their original color and other properties.
Signs of Metal Corrosion
Corrosion, which occurs through chemical or electrochemical reactions, alters both the appearance and structure of a material:
- Color Changes: Corrosion often leads to discoloration, such as the reddish-brown hue of rust on iron or the green patina on copper.
- Surface Alteration: Unlike erosion, corrosion can penetrate deeper into the material, causing pitting, cracks, or even complete structural failure.
Combined Damage: Erosion Corrosion
Erosion and corrosion often work together, worsening the damage to metal surfaces. For example, the underlying material is exposed and more vulnerable to corrosion when erosion removes a protective surface layer. This can lead to a mix of misshapen areas and chemically altered surfaces.
Diagnostic Techniques
Several tools and methods can help identify whether damage is caused by erosion, corrosion, or both:
-
- Surface Profiling: Analyzes the surface for signs of erosion, such as grooves, indentations, or thinning.
- Corrosion Coupons: Places metal samples in the operating environment to measure how quickly corrosion occurs.
- Ultrasonic Testing: Measures the thickness of the material to detect internal corrosion or thinning.
- Radiography: Uses X-rays to reveal hidden damage beneath the surface, caused by either process.
- 3D Imaging: Creates detailed models to visualize and measure the extent of erosion on complex surfaces.
By combining visual inspections with these diagnostic methods, you can pinpoint the type of damage affecting your metal components. This knowledge is essential for choosing the proper protection to extend the life of your equipment and avoid costly failures.
How to Prevent Metal Erosion and Corrosion
Preventing erosion and corrosion starts with understanding the conditions your metal components face. With the right strategies, you can protect surfaces from damage and extend the lifespan of your equipment. One of the most effective ways to achieve this is by coating metal surfaces with durable materials like chromium.
Preventing Corrosion
Corrosion can be minimized by creating barriers that shield metal from environmental elements or by using materials that resist chemical reactions:
- Protective Coatings: Anti-corrosion coatings, such as Armoloy’s chromium-based surface solutions, block moisture, oxygen, and chemicals from reaching the metal. Chromium, one of the hardest metals, offers superior protection against corrosion.
- Material Selection: Choosing corrosion-resistant metals or alloys, like stainless steel or aluminum, reduces the risk of chemical reactions.
- Environmental Controls: Reducing humidity, controlling temperature, or minimizing exposure to corrosive substances can limit corrosion.
- Cathodic Protection: Using electrical currents or sacrificial anodes to prevent metal oxidation is a proven method in pipelines and marine structures.
Preventing Erosion
Erosion damage is reduced by reinforcing surfaces and optimizing design to handle high-speed flows and abrasive conditions:
- Wear-Resistant Coatings: Armoloy’s TDC (Thin Dense Chrome) coatings enhance surface durability, reducing material loss from abrasion or impact.
- Optimized Flow Design: Controlling the speed and angle of flows in pipes and turbines can minimize erosive forces.
- Material Hardening: Using harder metals or surface treatments increases resistance to wear and impact.
- Particle Filtration: Removing abrasive particles from liquid or gas flows prevents surface damage in pipelines and machinery.
By applying tailored prevention strategies, you can significantly reduce the risks of erosion and corrosion. Armoloy’s advanced coatings are designed to handle these forces’ unique challenges, providing long-lasting protection and reliability in even the most demanding environments.
Additional Comparisons and Related Concepts
Erosion and corrosion are often discussed alongside other processes that affect materials, such as abrasion, weathering, and erosion corrosion. Understanding these related concepts helps provide a more complete picture of how metals degrade and how to protect them effectively.
Abrasion
Abrasion occurs when two surfaces come into contact and wear down each other through friction. Unlike erosion, which is caused by external forces like flowing liquids or gases, abrasion typically involves direct surface contact.
- Example: Conveyor belts in industrial settings often experience abrasion as materials move across their surfaces.
- Prevention: Harder materials, smoother finishes, or Armoloy’s wear-resistant coatings can reduce abrasion damage.
Erosion Corrosion
Erosion corrosion happens when erosion and corrosion occur together, creating compounded damage. The Erosion mechanism removes protective coatings or material layers, exposing the surface to corrosive agents.
- Example: In pipelines, high-velocity flows can erode the protective coating, allowing corrosion to attack the exposed metal underneath.
- Prevention: Dual-purpose treatments, like Armoloy’s advanced coatings, can simultaneously protect against mechanical and chemical damage. They also require regular maintenance and design improvements to reduce high-impact zones.
Erosion vs. Weathering
Weathering is a natural process where rocks and metals break down due to long-term exposure to environmental factors like wind, rain, and temperature changes. While erosion involves movement (e.g., water carrying particles away), weathering primarily weakens material in place.
- Example: Outdoor metal structures, like fences, can weaken over time due to weathering.
- Prevention: Weather-resistant coatings and regular maintenance help reduce the effects of weathering.
Corrosion vs. Rusting
Rusting is a specific type of corrosion that happens when iron reacts with oxygen and moisture, forming iron oxide (rust). While all rusting is corrosion, not all corrosion results in rust.
- Example: Steel bridges often develop rust if not correctly maintained.
- Prevention: Anti-corrosion coatings, like Armoloy’s treatments, prevent rust by blocking moisture and oxygen.
Understanding these related processes can help you better protect metal components from damage. Whether it’s abrasion, erosion, or corrosion, Armoloy’s surface treatments provide a versatile and effective solution to extend the life of your equipment.
Protect Metal Components with Diverse Surface Treatments
Erosion and corrosion are two of the most common forces that degrade metal components, but they operate differently. Erosion removes material through physical forces, while corrosion chemically alters and weakens the metal itself. Understanding the differences between these processes—and how they often work together—helps you better diagnose and prevent damage to critical systems.
You can protect your metal components from these damaging forces by choosing the right strategies, such as Armoloy’s protective coating technologies. From wear-resistant chromium platings that combat erosion to anti-corrosion solutions that shield metals from chemical attacks, Armoloy offers tailored solutions to keep your equipment running longer and performing at its best.
Proper protection extends the life of your components and improves safety, reliability, and cost-efficiency. Don’t let erosion or corrosion compromise your operations—trust Armoloy to safeguard your investments.