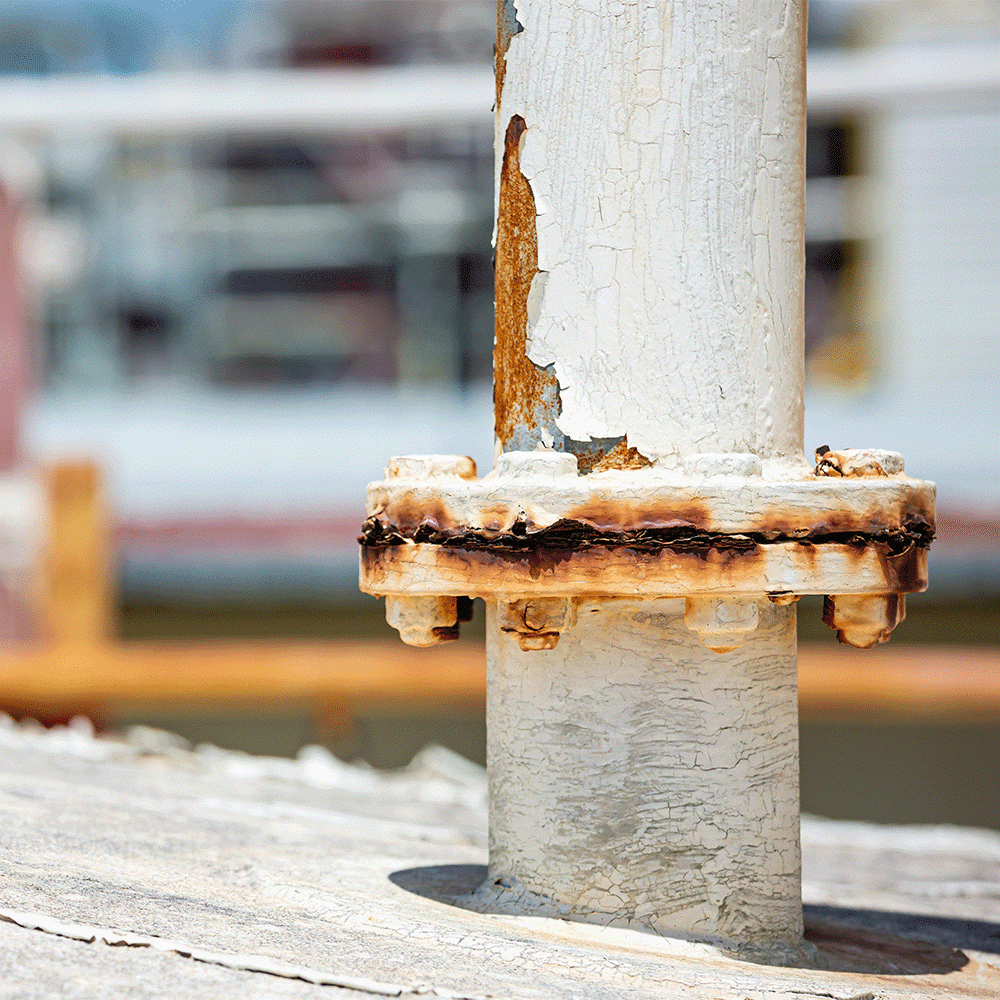
What is Crevice Corrosion?
Crevice corrosion is a localized form of corrosion occurring in confined spaces where access to the working fluid from the environment is limited. These confined spaces, or crevices, can trap stagnant solutions, leading to differential aeration cells that promote corrosion within the crevice.
This guide explores:
- Common locations of crevice corrosion
- The cause and stages of crevice corrosion
- Prevention strategies with corrosion inhibitors
- Protection for long-term reliability
Common Locations of Crevices
Gaps and contact areas between parts
The gap between this car trunk door provides corrosive elements a place to build up. It takes very little corrosion damage between painted crevices to progress into the damaging filiform corrosion seen above.
Under gaskets or seals
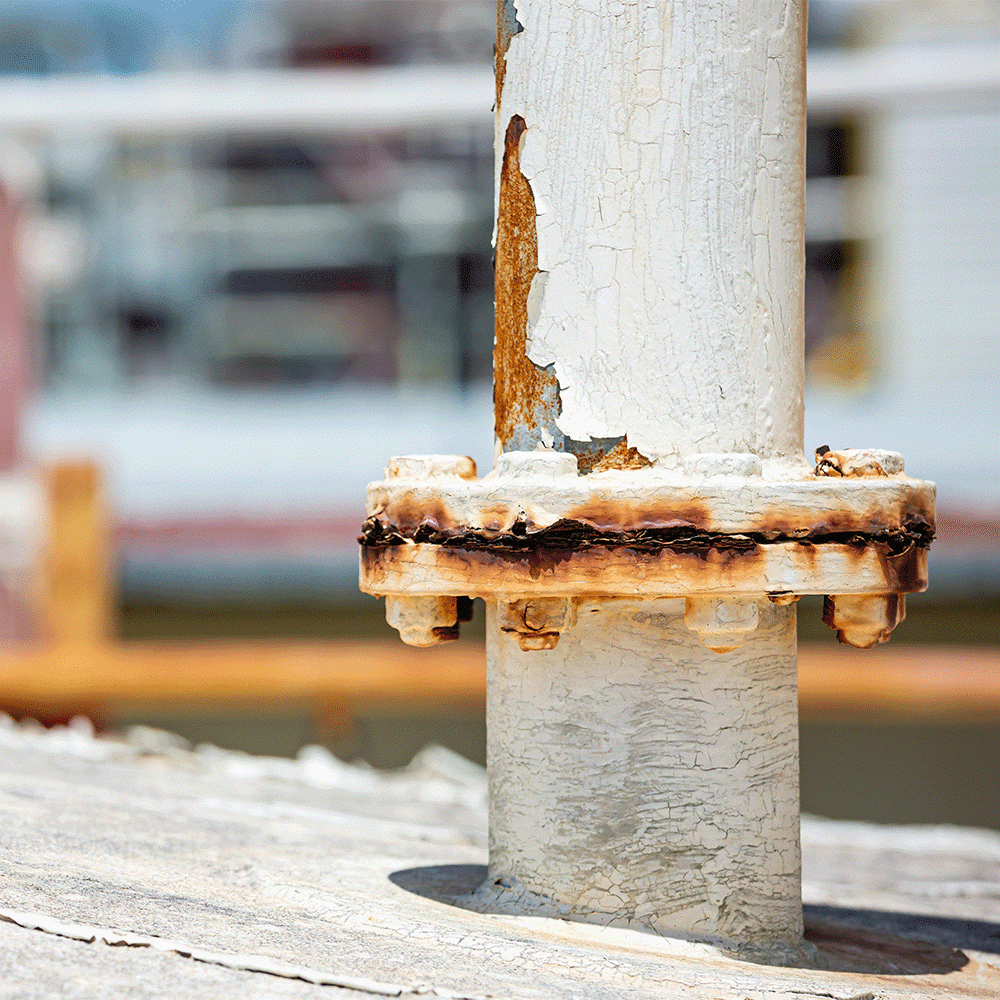
Even air tight seals between pipes will eventually require repair from corrosive elements that slip through the smallest of spaces.
Inside cracks and seams
A weld fragment has created a small crack in this pipeline, providing ample space for chloride ions to collect and begin degrading the material.
Spaces filled with deposits
Due to the inevitable deposit buildup around this heat exchanger latch door, an effective maintenance plan is essential for corrosion control.
Under piles of sludge
The oil sludge encasing the bolts above acts as a heat insulator and a source for corrosive media, further progressing crevice corrosion.
The Cause of Crevice Corrosion
Crevice corrosion arises when a localized, oxygen-restricted environment forms in tight gaps between metal surfaces or beneath deposits. These crevices prevent fluid circulation and oxygen replenishment, creating conditions that are distinct from the surrounding exposed metal. Over time, this imbalance fosters the formation of a differential aeration cell—a critical precursor to corrosion. The lack of oxygen inside the crevice disrupts the stability of the metal’s protective oxide layer, setting the stage for localized attack once electrochemical reactions begin.
Stages of Crevice Corrosion
Stage One – Initiation:
Crevice Formation and Oxygen Depletion
Crevice corrosion begins when a narrow gap forms between two metal surfaces, such as where the two metal plates pictured above meet. This confined space restricts the movement of fluids, leading to stagnant conditions where corrosive substances like seawater accumulate. As natural electrochemical reactions occur, oxygen within the crevice is rapidly consumed, while metal ion concentration rises. This imbalance establishes a galvanic cell, with the crevice acting as the anodic region and the surrounding metal surface becoming cathodic.
Ion Migration and Acidification
With the galvanic couple in place, corrosion intensifies as oxygen reduction continues at the cathode. The anodic area inside the crevice attracts negatively charged ions, such as hydroxide and chloride, which interact with the metal surface. These reactions lead to an increasingly acidic environment within the crevice, accelerating the breakdown of protective oxide layers and making the metal more vulnerable to further deterioration.
Stage Two – Propagation:
Rapid Corrosion and Structural Failure
Once the pH inside the crevice reaches a critically low level, the metal’s passive protective layer deteriorates completely. Without this defense, the corrosion process accelerates unchecked, leading to significant material loss and potential structural failure. If left unaddressed, this final stage of crevice corrosion can compromise the integrity of metal components, posing serious risks in marine, industrial, and structural applications.
Prevention Strategies with Corrosion Inhibitors
Preventing crevice corrosion requires a proactive, multi-layered approach that addresses both material vulnerabilities and environmental conditions. By combining corrosion-resistant materials, protective coatings, and electrochemical protection methods, engineers can significantly reduce the likelihood of localized attack. The following strategies outline practical measures to minimize risk and extend the service life of metal components.
Material Selection
Material selection plays a crucial role in preventing crevice corrosion. Choosing materials with inherent resistance to harsh environments can significantly enhance the longevity and integrity of components. Below are key considerations for material selection:
Opt for Alloys with High Molybdenum and Chromium Content
Alloys enriched with molybdenum and chromium exhibit enhanced resistance to crevice corrosion. These elements enhance the passive oxide layer’s stability, making it more resilient against corrosive agents. For instance, duplex stainless steels like SAF 2205 (22% chromium, 5% nickel, 3.2% molybdenum) are known for their high resistance to various forms of corrosion, including crevice corrosion.
Utilize Super Austenitic and Super Duplex Stainless Steels
Grades such as 904L and AL-6XN are designed to withstand aggressive environments due to their high nickel and molybdenum content. These super austenitic stainless steels offer enhanced protection against crevice corrosion, especially in chloride-rich settings. Similarly, super duplex stainless steels combine high strength with excellent corrosion resistance, making them suitable for challenging applications.
Consider Titanium and Its Alloys
Titanium exhibits exceptional resistance to crevice corrosion, particularly in seawater and other chloride-containing environments. Its ability to form a stable, protective oxide layer makes it a preferred choice for marine applications and chemical processing equipment. For example, using Grade 7 titanium (which includes palladium for enhanced corrosion resistance) in areas susceptible to crevice corrosion can be beneficial.
Aside from the bars shown above, titanium is also commonly offered in the form of plates, tubes, and wires.
Evaluate the Pitting Resistance Equivalent Number (PREN)
The PREN is a predictive measure of a stainless steel’s resistance to pitting and crevice corrosion. It is calculated using the formulas below, depending on whether or not tungsten content is present in the chosen steel:
A higher PREN indicates better resistance. Stainless steels with a PREN greater than 40 are typically specified for seawater service, where the risk of crevice corrosion is significant.
Design Considerations
Beyond material selection, thoughtful design can minimize crevice formation. Ensuring proper sealing, avoiding sharp corners, and eliminating unnecessary gaps can reduce the likelihood of crevice corrosion.
Protective Coatings
Protective coatings help prevent corrosion, including crevice corrosion, by shielding metal surfaces from environmental exposure. Common types include:
- Barrier Coatings: Epoxy and polyurethane form a protective seal to block moisture, oxygen, and chemicals.
- Sacrificial Coatings: Zinc (galvanization) corrodes preferentially to protect the underlying metal.
- Conversion Coatings: Phosphate coatings chemically modify surfaces to improve corrosion resistance.
- Metallic Coatings:
- Nickel (Sulfamate, Electroless): Provides excellent corrosion resistance but moderate wear resistance.
- Thin Dense Chrome (TDC): Offers good corrosion resistance with excellent wear protection.
Selecting the right coating ensures long-term corrosion prevention, reducing maintenance costs and extending equipment life in most operating environments.
Cathodic Protection
Cathodic protection (CP) is an effective technique used to suppress the electrochemical reactions that drive corrosion by converting the protected metal surface into a cathode, preventing it from losing electrons. There are two primary methods of cathodic protection: sacrificial anode protection and impressed current cathodic protection (ICCP).
1. Sacrificial Anode Cathodic Protection (SACP)
This method involves attaching a more electrically active metal (anode) to the structure needing protection. The sacrificial anode has a higher tendency to oxidize, meaning it corrodes instead of the protected metal. The corroding anode continuously supplies electrons to the protected structure, preventing oxidation (corrosion) of the metal surface.
Sacrificial anodes can be seen on this ship’s hull, used as a corrosion inhibitor to protect the structure of the ship.
Common sacrificial anode materials include zinc, magnesium, and aluminum.
Applications include ship hulls, offshore platforms, underground pipelines, and storage tanks.
2. Impressed Current Cathodic Protection (ICCP)
ICCP systems use an external power source (such as a rectifier) to supply a controlled electrical current to the protected metal. Unlike sacrificial anodes, ICCP systems use inert anodes (typically made of mixed metal oxides, titanium, or silicon iron) that do not degrade as quickly.
How ICCP works:
- A DC power source applies a current to the metal structure.
- Inert anodes distribute the protective current, ensuring the structure remains cathodic.
- This method is suitable for large infrastructure where sacrificial anodes alone may not provide sufficient protection.
Applications that utilize an ICCP system:
- Large pipelines and underground tanks
- Offshore oil rigs
- Reinforced concrete structures
- Ship hulls and water tanks
Key Differences Between SACP and ICCP
Feature | Sacrificial Anode (SACP) | Impressed Current (ICCP) |
---|---|---|
Power Source | No external power needed | Requires an external power source |
Anode Material | Zinc, magnesium, or aluminum | Inert anodes (titanium, MMO, etc.) |
Maintenance | Simple, requires periodic replacement | More complex, but longer-lasting |
Suitable Applications | Smaller structures (ships, tanks, pipelines) | Large infrastructure (bridges, offshore platforms) |
Cost | Lower initial cost, higher replacement cost due to frequency | Higher initial cost, lower maintenance |
Factors Influencing Cathodic Protection Effectiveness
- Environmental Conditions: Salinity, soil resistivity, and water conditions impact anode consumption and efficiency.
- Coating Synergy: CP works best when used in combination with protective coatings to reduce overall current demand.
- System Monitoring: Regular inspections and potential monitoring ensure long-term effectiveness.
By selecting the appropriate cathodic protection method based on the structure, environment, and cost considerations, operators can significantly extend the lifespan of metal components and mitigate the risks associated with corrosion.
Protecting Against Crevice Corrosion for Long-Term Reliability
Crevice corrosion poses relatively high risk to metal components in harsh environments, leading to structural degradation, safety concerns, and costly repairs. Understanding the causes and progression of crevice corrosion is essential for selecting the right prevention strategies.
By choosing corrosion-resistant materials, implementing protective coatings, and utilizing cathodic protection methods, operators can significantly reduce the risk of failure. Design considerations—such as minimizing crevice formations and ensuring proper sealing—further enhance longevity.
For businesses operating in marine, industrial, or chemical processing environments, proactive corrosion management is key to maintaining efficiency, safety, and cost-effectiveness. Investing in the right prevention techniques not only extends the lifespan of metal assets but also minimizes downtime and maintenance expenses.
Get Expert Advice from Armoloy
To explore advanced surface treatments and protective coatings that enhance metal performance, contact Armoloy today. Our expertise in Thin Dense Chrome (TDC) and other corrosion-resistant coatings provides long-lasting solutions tailored to your industry’s needs.
Share on LinkedIn Share on Facebook
Chat with Armoloy
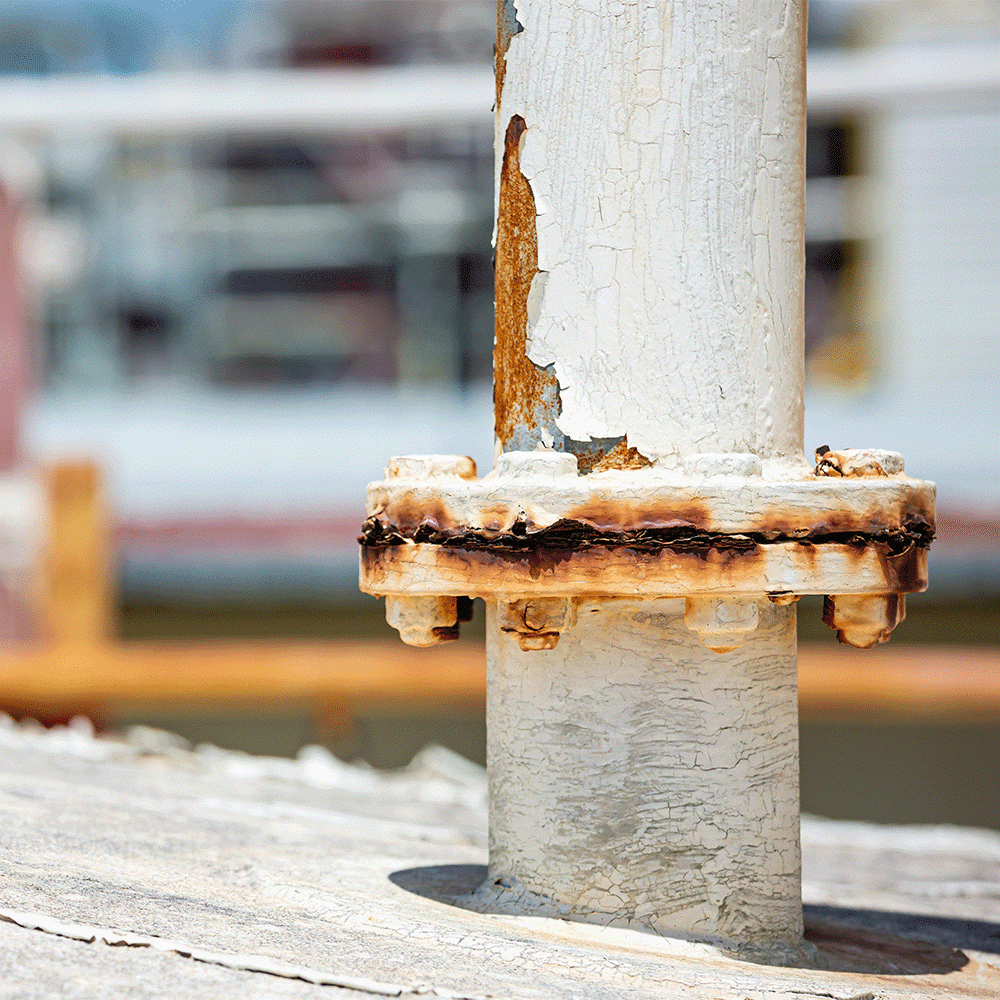