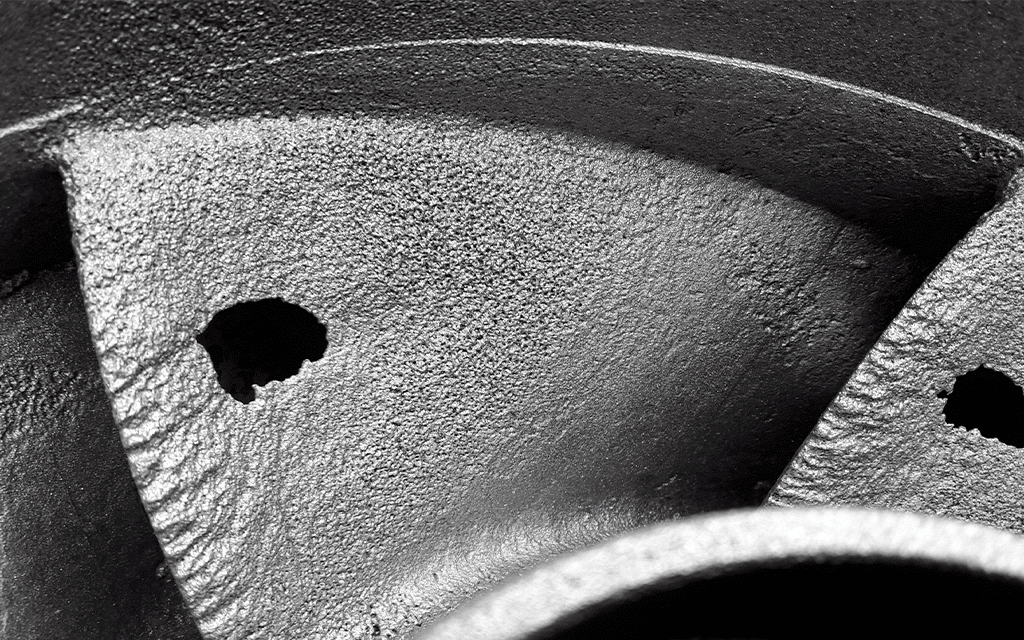
What is Cavitation?
Cavitation is a phenomenon that occurs when rapid changes in fluid pressure cause the formation and collapse of vapor-filled bubbles within a liquid. This process, often triggered in high-velocity or turbulent environments, can lead to intense shockwaves as the bubbles collapse, impacting nearby surfaces. Cavitation is particularly relevant in engineering and fluid dynamics, where it can severely impact the efficiency and lifespan of equipment exposed to liquid flow under varying pressures.
In industries such as marine, power generation, and petrochemical processing, cavitation is a critical factor in the wear and degradation of metal components. Structures like pump impellers, turbine blades, and propellers are especially susceptible. Over time, cavitating forces can cause metal fatigue, pitting, and erosion, leading to compromised performance, increased maintenance costs, and potential equipment failures. Understanding cavitation’s mechanisms and effects is essential for designing durable equipment, enhancing operational efficiency, and preventing costly downtime.
Explore any section of this article using the links below:
- Mechanisms
- Effects on Metals
- Components & Industries Affected
- Detection, Diagnosis, & Prevention
- References for Further Reading
Mechanisms of Cavitation
Cavitation is fundamentally driven by variations in fluid pressure that lead to the formation of vapor-filled bubbles within a liquid. When a liquid experiences a sudden drop in pressure, typically below the vapor pressure of any dissolved gases, small vapor bubbles will form. These bubbles grow in low-pressure zones and eventually collapse as they move into areas of higher pressure, releasing energy in the form of intense shockwaves. This rapid bubble formation and collapse generate powerful forces capable of eroding nearby surfaces.
Illustration shows collapse of vapor bubble and microjet initiation creating a cavitating process
There are two primary types of cavitation: inertial (transient) cavitation and stable (on-inertial cavitation), each defined by its distinct bubble behavior.
Inertial (Transient):
In inertial cavitation, bubbles undergo rapid, explosive growth followed by a sudden, forceful collapse. This type of cavitating event is common in high-energy environments such as pumps, propellers, and turbines. When bubbles collapse near a solid surface, they generate high-pressure microjets and shockwaves that cause localized damage to metals, resulting in pitting, erosion, and even material failure over time. This sudden and intense bubble behavior is particularly destructive and requires precise engineering strategies to mitigate its impact.
Illustration of stable vs. inertial cavitation
Acoustic and Ultrasonic
Inertial cavitation can take place within an acoustic field, where microscopic gas bubbles present in a liquid oscillate under the influence of sound waves. At higher acoustic intensities, these bubbles expand and then collapse rapidly. This process allows inertial cavitation to occur even when the rarefaction in the liquid is insufficient to form a Rayleigh-like void.
Ultrasonic cavitation begins when the ultrasound source generates enough acceleration to cause a pressure drop. The required pressure drop is influenced by the acceleration and the size of the area impacted by the pressure wave. The Garcia-Atance number—a dimensionless value—can predict ultrasonic cavitation. Ultrasonic horns with high power are capable of creating cavitating regions, which are utilized in various processes such as homogenization, dispersion, deagglomeration, erosion, cleaning, milling, emulsification, extraction, disintegration, and sonochemistry.
Ultrasonic cleaning machine for engine parts maintenance
Stable Cavitation
Stable (non-inertial) cavitation involves the formation of bubbles that do not undergo such violent collapse but instead oscillate in response to pressure changes. This type of cavitating mechanism is often seen in ultrasonic cleaning or certain medical applications where controlled cavitation aids in cleaning or cell disruption. While non-inertial cavitation produces less severe impacts on surfaces, it can still cause wear over extended periods, especially in delicate equipment.
Understanding these cavitating mechanisms is essential for designing fluid systems that minimize harmful cavitation effects, as well as for developing materials and coatings that can withstand the stresses induced by this phenomenon.
Aerodynamic
While cavitation is commonly associated with liquids, it can also occur in gasses due to high-speed fluid dynamics. For instance, a flat-tipped bullet moves faster underwater by generating cavitation compared to a sharp-tipped bullet. In aerodynamics, a dune-like shape serves as an ideal design to reduce air resistance. This shape minimizes drag by directing airflow upwards, beneath, and behind, lowering air pressure in those regions and reducing friction. Although a dune surface might increase frontal resistance, the overall reduction in friction outweighs this effect, much like how an underwater flat-tipped bullet functions. Consequently, applying a similar design to high-speed vehicles or aircraft can significantly enhance their speed by optimizing air resistance.
A flat bullet travels faster than a tip bullet underwater due to factors including drag, cavitation, and bubble dynamics
Effects of Cavitation on Metals
Cavitation exerts powerful forces on metal surfaces, often leading to significant wear and degradation. When a vapor bubble forms and low-pressure zones collapse near a metal surface, they generate intense localized shockwaves and microjets as the surrounding fluid rushes into the space the bubble was occupying. These sudden forces impact the metal, causing microscopic damage that accumulates over time, resulting in surface fatigue. The repetitive nature of cavitation-induced impacts weakens the metal’s structure, creating small cracks that spread and deepen with continuous exposure.
Click the video above to view a demonstration of cavitation occurring with the creation and implosion of vapor bubbles between two moving gears
Cavitation manifests in three primary forms of metal damage:
Surface Fatigue
Repeated impacts from collapsing bubbles cause stress cycles in the metal, leading to surface fatigue. This type of stress weakens the metal’s microstructure, making it more susceptible to further damage and accelerating the wear process.
Pitting
Cavitation produces small, concentrated impact zones where metal is forcefully removed, creating pits or craters. These pits compromise the integrity of the surface, reducing its ability to withstand operational demands and leading to premature failure in highly stressed components.
Pitting seen on centrifugal pump impeller caused by cavitation
Erosion
Over time, cumulative cavitating impacts result in significant material loss, known as erosion. This eroded surface not only reduces the component’s efficiency but also compromises its structural strength, making it more vulnerable to failure under load.
Total metal failure of pump impeller gear due to prolonged cavitation-induced erosion
Components Commonly Affected
Examples of components commonly affected by cavitation include pump impellers, turbine blades, and propellers. In high-velocity applications, such as fluid pumps and turbines, cavitation can severely shorten the lifespan of these parts, necessitating frequent repairs or replacements. In marine and hydropower environments, propellers and turbine blades are particularly vulnerable, as the cavitating forces gradually erode metal surfaces, diminishing performance and reliability.
Understanding cavitation’s effects on metals is crucial for industries where equipment reliability and efficiency are essential. By addressing metal failure early on through optimized designs and protective coatings, companies can reduce maintenance costs, extend equipment life, and ensure operational stability.
Marine Engineering
Cavitation is a persistent issue in marine applications, especially for ship propellers and rudders. Propellers, which operate in high-speed water environments, are highly susceptible to cavitation-induced pitting and erosion. This degradation not only reduces propulsion efficiency but also increases fuel consumption and operational costs. Additionally, cavitating events on rudders affects maneuverability and can lead to vibration issues, diminishing navigational control and passenger comfort.
Cavitation burn is a common occurrence on boat propellers
Hydropower
In hydropower facilities, turbine blades and penstocks (pressurized conduits) are directly exposed to cavitation risks due to fluctuating water pressures and high flow rates. Turbine blades, in particular, experience intense cavitation impacts that erode metal surfaces, gradually impairing energy efficiency and potentially requiring costly, frequent replacements. Prolonged cavitation damage to these components can compromise the entire power generation process, leading to downtime and reduced energy output.
Petrochemical Industry
In the petrochemical industry, pumps and compressors are vulnerable to cavitating damage, especially when handling high-viscosity fluids. Cavitation impacts can lead to leakage, pressure inconsistencies, and eventual pump failure, resulting in production halts and safety risks. With many petrochemical processes depending on the continuous, reliable function of pumps and compressors, preventing cavitation is essential for minimizing downtime and avoiding costly repairs.
Cavitation process example in pump
Other Critical Applications
Additional sectors affected by cavitation include wastewater treatment (where aeration systems can be impacted), nuclear power (where cooling pumps are susceptible), and automotive engineering (particularly in fuel injection systems). Across all of these, cavitation mitigation is vital for maintaining efficiency, safety, and component longevity.
Detection and Diagnosis
Effective detection and diagnosis of cavitation are critical for preventing extensive damage and maintaining operational efficiency. Proactive detection enables timely interventions, reducing the risk of costly repairs and unplanned downtime. Several methods are widely used to identify cavitation in its early stages:
Acoustic Monitoring
Cavitation produces distinctive sounds, often described as a “crackling” or “popping” noise, as vapor bubbles collapse. Acoustic monitoring systems are designed to detect these unique sound patterns and alert operators to cavitation activity. With acoustic sensors installed near vulnerable components, such as pumps and turbines, operators can continuously monitor for early signs of cavitation, enabling prompt corrective actions before damage escalates.
Visual Inspections
Regular visual inspections are essential, especially for equipment prone to cavitation damage. During inspections, maintenance teams look for surface pitting, erosion, and any unusual wear patterns that indicate cavitation. Although visual inspections are more labor-intensive, they offer invaluable insights into cavitation severity and can identify affected areas that require immediate attention.
Vibration Analysis
Cavitation often causes increased vibration in equipment due to the energy released from collapsing bubbles. Vibration analysis can help detect abnormal vibration frequencies, signaling potential cavitation issues. By using vibration sensors, operators can monitor changes in vibration patterns that may indicate cavitation onset, especially in rotating machinery like turbines and propellers.
Worker inspecting for cavitation damage of pump with a vibration sensor
Pressure Monitoring
Pressure sensors are valuable tools for identifying the low-pressure zones that facilitate cavitation. Monitoring pressure variations across fluid systems helps detect conditions that favor cavitation formation. By addressing low-pressure hotspots, operators can adjust operational parameters to reduce cavitation risks.
Importance of Early Detection
Early detection of cavitation is essential for preserving equipment integrity and operational efficiency. Identifying cavitation at its inception allows for immediate adjustments to flow rates, pressure settings, or fluid characteristics, minimizing further damage. For example, addressing early cavitation signs in a pump can prevent catastrophic failure, extend equipment lifespan, and avoid unexpected downtime.
With cavitation detection strategies in place, industries can move beyond reactive maintenance, ensuring that equipment remains in optimal condition and reducing the frequency of costly repairs. Proactive cavitation management is a cornerstone of reliable, high-performance operations across fluid-intensive sectors, ultimately leading to more sustainable and cost-effective operations.
Preventive Measures and Mitigation Strategies
Preventing cavitation and mitigating its effects require a comprehensive approach, incorporating design, material selection, and operational adjustments to reduce the conditions that trigger cavitation. By focusing on these preventive strategies, industries can safeguard critical equipment, improve efficiency, and minimize maintenance costs.
Design Considerations
Optimizing Fluid Flow
Proper flow design is essential in reducing cavitating risk. Engineers can optimize fluid pathways to minimize sharp turns, sudden expansions, or abrupt velocity changes that create pressure differentials and encourage metal failure modes. Streamlined flow paths help maintain stable pressure, preventing the formation of vapor bubbles.
Selecting Appropriate Materials
Certain materials are better suited to withstand cavitation-induced forces. Using metals and alloys with high hardness, resilience, and corrosion resistance can enhance the durability of components like pump impellers and turbine blades. Stainless steel, for example, offers both strength and resistance to erosion, making it a preferred material for cavitation-prone environments.
This centrifugal pump is made of stainless steel with a combination of protective coatings for improved resistance to metal failures
Operational Strategies
Controlling Pressure Variations and Temperature
Operators can manage cavitation by adjusting system pressures to avoid conditions where fluid pressure drops below its vapor pressure. Automated pressure controls and real-time monitoring enable precise pressure management, reducing cavitation onset in pumps, turbines, and other high-velocity fluid systems. Additionally, reducing system temperature is a critical control strategy. Higher temperatures increase the likelihood of gases forming bubbles, exacerbating cavitation risks. By optimizing temperature alongside pressure, operators can achieve more effective system performance and longevity.
Maintaining Proper Fluid Levels
Inconsistent or low fluid levels contribute to cavitation by increasing the likelihood of air ingestion, which can exacerbate vapor bubble formation. Ensuring optimal fluid levels and conducting regular inspections help maintain stable fluid dynamics, minimizing cavitation risks.
Implementing these design and operational strategies reduces cavitation potential, preserves equipment health, and promotes uninterrupted performance across fluid-based systems.
Advancements in Cavitation Research
Recent advancements in cavitation research are unveiling new ways to understand, prevent, and counteract cavitation-induced damage. As industries face increasing demand for efficient, high-performance equipment, the need for innovative solutions to combat cavitation is growing. Research is leading to cutting-edge materials, coatings, and diagnostic tools designed to withstand and mitigate the effects of cavitation.
Innovative Materials and Alloys
Researchers are developing specialized alloys that are more resistant to cavitation erosion and surface fatigue. Materials like titanium alloys and high-nickel alloys demonstrate enhanced resilience to cavitation forces, making them ideal for high-stress applications. These materials offer both durability and corrosion resistance, which is especially beneficial in marine and hydropower environments.
Advanced Coatings for Protection
Technological advancements in coating materials are creating new opportunities for cavitation prevention. Ceramic coatings and polymer-based coatings are being used to shield metal surfaces from cavitation damage, providing a barrier that absorbs shockwaves and resists erosion. Additionally, nanocoatings are gaining attention for their potential to create highly durable surfaces with exceptional resistance to cavitation-induced stress.
Diagnostic and Monitoring Technologies
New diagnostic tools, such as ultrasonic cavitation detectors and real-time pressure monitors, allow for more accurate detection and tracking of cavitation in fluid systems. These tools enable engineers to identify cavitation-prone zones and make immediate adjustments, minimizing cavitation damage before it escalates. By employing advanced monitoring solutions, operators can maintain optimal system performance while mitigating risks associated with cavitation.
Ultrasonic processor for detecting cavitation in fluid systems
Through continued research and technological advancements, industries can proactively address cavitation challenges, ensuring the reliability and longevity of equipment in demanding applications. Embracing these innovations is key to maintaining performance, reducing operational costs, and advancing industrial efficiency in fluid systems.
The Wrap on Cavitation
Cavitation remains one of the most challenging phenomena affecting metal components in high-velocity fluid systems. Its capacity to induce severe wear, from surface fatigue to pitting and erosion, has significant implications for industries like marine engineering, hydropower, and petrochemical processing, where equipment reliability and efficiency are paramount. Understanding the mechanics of cavitation—how it forms, damages surfaces, and can be mitigated—is essential for engineering durable solutions that keep vital equipment operational.
Implementing proactive measures to prevent and control cavitation is crucial for preserving system performance, reducing maintenance costs, and extending equipment life. Design optimizations, material selection, and precise operational control each play a vital role in minimizing cavitation risk. Additionally, advancements in cavitation-resistant materials, protective coatings, and monitoring technologies offer promising solutions for combating its damaging effects.
In an era of high-performance demands and tight operational margins, recognizing and addressing cavitation proactively is more important than ever. By investing in preventive strategies and adopting the latest advancements, industries can reduce downtime, ensure safety, and achieve long-term operational efficiency. Understanding cavitation and acting to mitigate its impact is not just about protecting metal components; it’s about fostering a resilient and efficient operational environment that supports sustained productivity and innovation.
References and Further Reading
For those seeking a deeper understanding of cavitation, including its mechanisms, impact, and mitigation strategies, the following resources offer authoritative insights and comprehensive information on the topic:
- Brennen, C. E. (2014). Cavitation and Bubble Dynamics. Cambridge University Press.
This book is an authoritative source on the fundamentals of cavitation and bubble dynamics, covering topics such as the physics behind cavitation, its effects on various materials, and methods for analyzing and controlling it. Ideal for those looking to explore cavitation in a highly technical context.
- Franc, J. P., & Michel, J. M. (2006). Fundamentals of Cavitation. Springer.
A foundational text that provides an in-depth analysis of cavitation’s physical principles, types, and implications across different applications. This book also explores experimental methods and offers valuable insights for engineers and researchers focused on metal failure prevention.
- Pumps & Systems Magazine. “What Is Cavitation?”
An industry-oriented resource that discusses the metal failure mode within the context of fluid systems, specifically in pumps and turbines. Available online at Pumps & Systems.
- Corrosionpedia. “Cavitation Corrosion”.
A detailed article explaining cavitation corrosion, its mechanisms, and strategies to prevent damage. This source is especially relevant for those working with metal components in corrosive environments. Available online at Corrosionpedia
- Engineering Toolbox. “Cavitation in Fluid Flow Systems”.
An accessible guide on the causes and effects of cavitation in engineering applications, with a focus on fluid dynamics. It includes practical examples and strategies for reducing metal failure in industrial systems. Available online at Engineering Toolbox.
- NASA Technical Reports Server (NTRS)
Provides access to various research papers and studies, especially in aerospace and marine applications. NASA’s studies on cavitation are comprehensive and highly detailed, offering insights that are relevant across multiple engineering fields. Available at NTRS
Additional Materials for Further Reading:
- American Society of Mechanical Engineers (ASME) Digital Collection: Contains numerous articles, case studies, and papers on cavitation effects, diagnostics, and control strategies in industrial systems.
- Journal of Fluids Engineering (ASME): Publishes peer-reviewed research on fluid dynamics, including advancements in cavitation detection and prevention.
- Proceedings of the Institution of Mechanical Engineers, Part C: Journal of Mechanical Engineering Science: Features articles on materials and design innovations aimed at mitigating cavitation in high-performance engineering applications.
These resources provide a solid foundation for readers interested in gaining a deeper, more technical understanding of cavitation and its management across various engineering disciplines.
Share on LinkedIn Share on Facebook