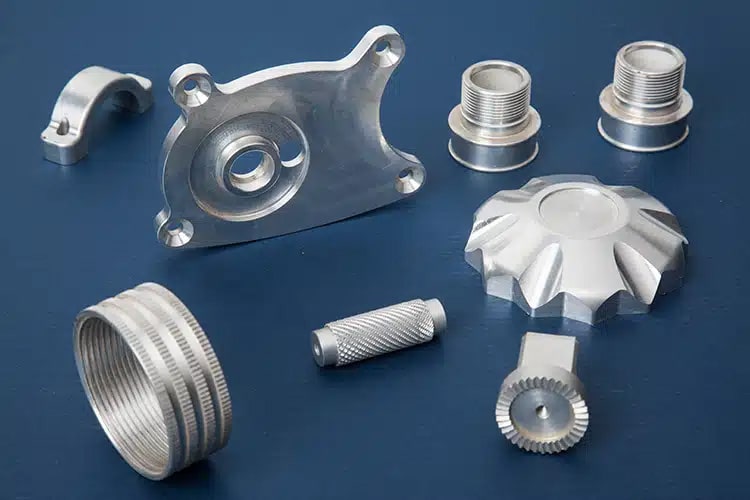
Anodizing is the go-to process for enhancing aluminum’s corrosion resistance — but it’s not the only option.
Whether you’re in aerospace, medical, or manufacturing, choosing the right surface treatment can dramatically impact part performance, longevity, and cost. In this guide, we break down how the anodizing process works, where it excels (and where it doesn’t), and how Armoloy’s AL-COAT® chromium coating stacks up as a high-performance alternative.
If you’re deciding between anodizing and another protective solution, this comparison will help you make the right call.
- Properties of Aluminum
- How the Anodizing Process Works
- Advantages of Anodizing
- Limitations of Anodizing
- AL-COAT® – The Anodizing Alternative
- Comparing AL-COAT® & Anodizing
The Properties of Aluminum – and Why They Matter for Surface Treatments
Aluminum is one of the most widely used metals in manufacturing due to its exceptional blend of lightness, strength, and corrosion resistance. But even with these inherent benefits, aluminum surfaces often require additional protection or enhancement through processes like anodizing or chromium coating.
Here’s a breakdown of aluminum’s key material properties — and why surface engineering plays a crucial role in getting the most out of them:
Lightweight but Strong
Aluminum’s low density makes it ideal for aerospace, robotics, and transportation, where minimizing weight without sacrificing performance is essential. However, its surface can be vulnerable to wear in high-friction environments. Protective coatings like anodizing and AL-COAT® help reinforce aluminum’s surface without significantly increasing part weight
Naturally Corrosion-Resistant – to a Point
Aluminum forms a thin oxide layer that protects against general corrosion, but this layer can break down in aggressive environments like saltwater, chemical washdowns, or sterilization cycles. Anodizing thickens the oxide layer, while AL-COAT® applies a dense, uniform chromium barrier that provides enhanced corrosion resistance — even in extreme or regulated conditions.
Ductile and Malleable
Aluminum is easy to shape and form, making it a favorite for custom or complex part geometries. But its softness can lead to surface deformation or wear under stress. Coatings must preserve aluminum’s flexibility while adding surface hardness. AL-COAT® achieves this with a low-stress
Excellent Electrical and Thermal Conductivity
Aluminum’s high conductivity is a plus in electrical components, heat sinks, and medical equipment. However, anodizing converts the surface into a non-conductive layer, which may not be suitable for all applications. AL-COAT®, depending on thickness and design, can retain some conductivity or be selectively masked to maintain electrical pathways.
Non-Sparking for Safety
Aluminum doesn’t produce sparks when struck, making it a smart choice for explosive or flammable environments like chemical processing or mining. Surface treatments should retain this safety feature. AL-COAT® maintains non-sparking properties while offering additional chemical resistance.
Fully Recyclable
Aluminum is 100% recyclable without quality loss, which is vital for sustainable design. Surface treatments like AL-COAT® are applied in thin, controlled layers and are RoHS- and REACH-compliant, ensuring environmental responsibility is maintained through the product lifecycle.
Bottom line: Aluminum is a highly capable base material — but the right coating can push its performance even further. Whether you’re optimizing for durability, biocompatibility, conductivity, or environmental resistance, your choice of surface treatment makes all the difference.
Aluminum and Anodizing: How the Process Works
Aluminum anodizing is one of the most common surface treatments used to enhance the performance and longevity of aluminum parts. Through an electrochemical process, the surface of the aluminum is converted into a thickened aluminum oxide layer that is both durable and corrosion resistant.
This oxide layer becomes an integral part of the metal — not a coating that can flake off — and it offers several benefits:
- Improved resistance to corrosion and environmental wear
- Greater surface hardness
- A porous structure than can absorb dyes for custom colors
- Better adhesion for paints or adhesives
Because anodizing maintains aluminum’s lightweight nature while improving surface durability, it is frequently used in consumer electronics, architectural components, medical instruments, and aerospace parts.
However, anodizing isn’t always ideal. It produces a porous layer that can still absorb contaminants or wear away under high friction or aggressive chemical exposure. It also creates a non-conductive surface, which may be a drawback in certain applications.
That’s where alternative aluminum coatings — like AL-COAT® — offer new opportunities to tailor surface properties for more demanding environments.
Advantages of Anodizing Aluminum
Anodizing aluminum offers several well-established advantages, making it a go-to surface treatment across industries like aerospace, medical, electronics, and architecture. Through a controlled electrochemical process, anodizing forms a durable aluminum oxide layer that enhances both appearance and performance.
Key Benefits of Anodizing:
Corrosion Protection
The anodized layer acts as a barrier against oxidation and moisture, helping parts resist corrosion in indoor, outdoor, or mildly corrosive environments.
Enhanced Surface Hardness
Anodizing increases the surface hardness of aluminum, improving its resistance to scratching, abrasion, and wear — particularly important in moving or contact-prone parts.
Color Customization
The porous structure of the anodized layer can be dyed in a wide range of colors. This makes it ideal for consumer goods, brand identification, or aesthetic finishes.
These machined parts have been anodized in an array of colors from standard silver to vibrant blue.
Dimensional Stability
Anodizing builds up the surface with minimal thickness change, making it an excellent option for tight-tolerance parts or assemblies.
Environmentally Friendly
Unlike many traditional coatings, anodizing does not use heavy metals or hazardous solvents, making it compliant with many environmental regulations.
Excellent Adhesion for Paints and Adhesives
The micro-porous nature of the anodized surface provides excellent bonding for subsequent coatings or adhesive applications.
Limitations of Anodizing
While anodizing is widely used and generally reliable, it’s not always the best fit for demanding environments or mission-critical parts. Its performance depends on the specific application — and in some scenarios, it can fall short.
Key Limitations
Limited Corrosion Resistance in Harsh Environments:
Although anodizing improves corrosion protection, it can degrade in environments with extreme pH, salt spray, or exposure to aggressive chemicals. This makes it less suitable for marine, sterilization, or chemical processing conditions without additional sealing.
Reduced Electrical Conductivity:
Anodized aluminum becomes non-conductive, which can pose problems in electronics, grounding, or EMI-sensitive applications. For parts that require conductivity, additional steps — like selective masking — are needed.
Brittle Oxide Layer:
The anodized surface is harder than raw aluminum but also more brittle. Under high mechanical stress, impact, or vibration, the oxide layer can crack, leading to premature wear or failure.
Moderate Wear Resistance:
Standard anodizing offers decent abrasion protection, but in high-friction or high-load applications, the porous oxide layer may erode over time. This limits its use in dynamic, sliding, or high-speed contact applications.
Appearance Degradation Over Time:
Anodized surfaces can fade or discolor with prolonged UV exposure or chemical contact, especially if dyes are used. This may be a concern in medical, aerospace, or branded components requiring long-term aesthetic performance.
Bottom line: For applications where maximum corrosion resistance, chemical inertness, or mechanical integrity is critical, a more robust coating like AL-COAT® may be a better long-term solution.
AL-COAT®: A Next-Generation Chromium Coating for Aluminum
For environments where anodizing reaches its limits, AL-COAT® offers a high-performance alternative. Engineered specifically for aluminum alloys, AL-COAT® is a thin, dense chromium (TDC) coating applied through a proprietary low-temperature process that preserves material integrity while dramatically improving surface performance.
Unlike anodizing, which alters the oxide layer on aluminum’s surface, AL-COAT® forms a uniform, metallurgically bonded chromium layer that delivers exceptional resistance to wear, corrosion, and chemical attack — without compromising dimensional tolerances.
What Sets AL-COAT® Apart:
Biocompatible and Medical-Grade:
AL-COAT is certified for use in medical and surgical applications, making it ideal for instruments, implants, and equipment used in sterile or regulated environments.
Removable and Machinable
Unlike anodizing, which permanently alters the surface through oxide conversion, AL-COAT behaves like a true coating layer. It can be removed through chemical stripping or standard machining, allowing for part refurbishment, dimensional rework, or coating replacement without damaging the substrate. This makes it ideal for molding tools, precision aluminum components, and applications that require lifecycle flexibility or adjustment after coating.
Good Corrosion Protection:
Its dense, non-porous surface resists corrosion in extreme environments — including saltwater, autoclave sterilization, and aggressive cleaning chemicals — where anodizing may break down.
Independent testing has shown that AL-COAT significantly improves the corrosion resistance of 6061-T6 aluminum, particularly in alkaline and chlorinated environments. It remains strongly adherent under harsh conditions, reducing maintenance cycles and part replacement. (See the comparison chart below for performance versus hard coat anodizing.)
Exceptional Wear Resistance:
AL-COAT outperforms anodizing in high-friction or abrasive applications such as sliding parts, robotic joints, and production tooling. The durable chromium layer resists surface degradation, extending part life and improving uptime.
Low-Temperature Application:
Unlike many coating processes, AL-COAT is applied at low temperatures that won’t distort aluminum substrates. This allows the preservation of tight dimensional tolerances and original part geometry.
Excellent Adhesion to Aluminum:
Engineered specifically for aluminum alloys, AL-COAT forms a uniform, tightly bonded chromium layer that won’t crack, peel, or flake — even under thermal or mechanical stress.
In short: AL-COAT bridges the gap between standard anodizing and advanced performance needs. When you require maximum wear resistance, reworkability, corrosion protection, and biocompatibility — without compromising tolerance or recyclability — AL-COAT is a proven surface treatment solution for aerospace, medical, food processing, and other demanding industries.
Anodizing vs. AL-COAT®: Which Aluminum Coating Is Right for You?
Both anodizing and AL-COAT® are effective aluminum surface treatments — but they serve different needs.
If your application requires basic corrosion resistance, color customization, and a cost-effective finish, anodizing is a solid choice.
But for parts exposed to extreme friction, harsh chemicals, autoclave sterilization, or dimensional sensitivity, AL-COAT® delivers an enhanced level of protection that anodizing simply can’t match.
Summary:
Property | Anodizing | AL-COAT® |
Corrosion Resistance | Good (moderate environments) | Excellent (extreme environments) |
Wear Resistance | Moderate | Exceptional |
Surface Hardness | Improved | High |
Electrical Conductivity | Non-conductive | Potential to retain |
Dimensional Impact | Minimal | Minimal |
Biocompatibility | Sometimes | Certified |
Aesthetic Options | High (colorable) | Low (3 finishes available) |
Cost | Lower | Higher (but longer lifespan) |
Bottom line: If you need a high-performance coating for mission-critical aluminum components — especially in medical, aerospace, or industrial applications — AL-COAT® may be the better investment.
Need Help Choosing?
Every application is different. Our team of coating specialists can help you evaluate your part requirements and determine whether anodizing, AL-COAT®, or another surface treatment is the best fit.
Contact us to start the conversation or request a sample part coated with AL-COAT®.
Share on LinkedIn Share on Facebook
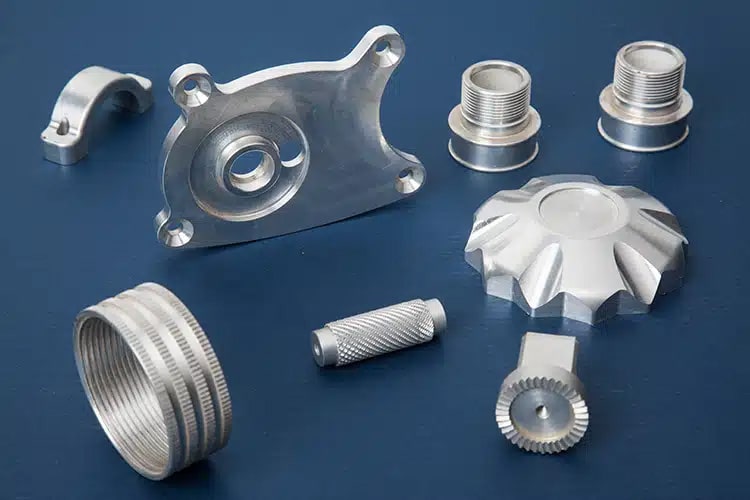