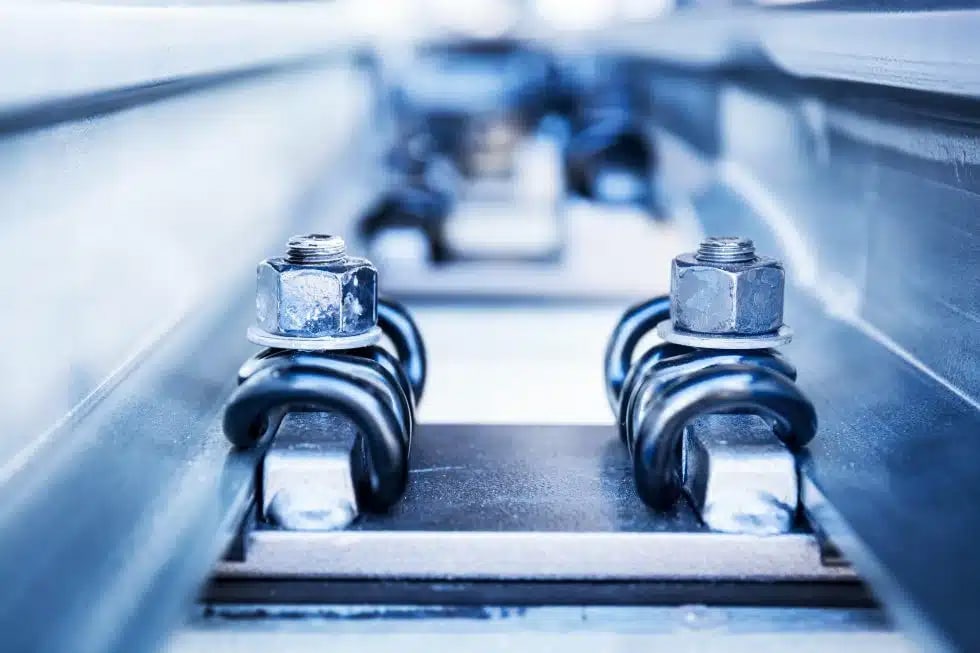
Material failure theory is defined as “an interdisciplinary field of materials science and solid mechanics which attempts to predict the conditions under which solid materials fail under the action of external loads.” Of particular importance to many product designers, manufacturers, and users is metal failure. One of the reasons for this focus is that there is so much riding on the performance of metal parts, tools, and devices—and large risks should those items fail.
Two common causes of metal failure are contact fatigue and abrasion. In fact, they are common enough that the two terms are sometimes, mistakenly, used interchangeably. However, they are two different forces that affect metal items in different ways, so it is important to understand what they are and how they can be counteracted to protect metal assets.
Metal Contact Fatigue and Abrasion Defined
Contact fatigue is a condition that occurs when “cyclic loading”—the repeated application of force—causes internal cracking that leads to surface pitting on metal items. It is often seen when curved surfaces are in contact under normal load conditions. It can be observed in everything from ball bearings and roller bearings to gears and valves.
The amount of damage produced by contact fatigue depends on factors such as the properties of the materials that are in contact with one another, the presence or absence of lubricants, and conditions on the surfaces of the two items. When damage occurs, the first sign tends to be the loss of smooth operation. For example, bearings often begin to produce noise that was not present before the surface pitting developed. If left unchecked, the damage can lead to catastrophic failure of bearings and all the consequences that stem from it.
Abrasion also damages the surface of metal items, but it occurs as a result of the wearing away of material, rather than internal cracking that manifests as surface damage. Any time that two materials come into contact with one another forcefully and repeatedly, abrasion can occur. The likelihood of abrasion is especially high when two metals of different hardness collide.
As with contact fatigue, the amount of damage produced by abrasion is affected by several factors. The most important may be the absence or loss of some type of buffering material between the two surfaces that are in contact with one another. And, also similar to contact fatigue, abrasion can result in catastrophic metal failure.
Addressing Contact Fatigue and Abrasion in Metal Parts and Devices
Many types of businesses can be affected by metal contact fatigue and abrasion. This includes those in industries like manufacturing, food processing, oil and gas, plastic injection molding, and medical and aerospace technology.
Metal failure can range from a minor inconvenience, like replacing a tool, to major revenue losses if a production line is halted for repairs. Regardless of where it occurs, its impact can be significant. In addition, in some instances, there is the risk of personal injury when a catastrophic failure occurs.
Fortunately, there are steps that businesses can take to reduce the instances and consequences of metal failure. These include:
- Performing regular inspections of parts and systems that are subject to contact fatigue, abrasion, and other damaging forces
- Maintaining measures designed to minimize the effects of these forces, such as keeping systems properly lubricated
- Protecting vulnerable surfaces with advanced metal coatings
The last in this list may be first in importance from the perspective that well-protected metal surfaces, while they still require inspection, typically need attention far less often than unprotected surfaces.
Advanced metal coatings such as thin dense chrome (TDC), diamond chrome (XADC), electroless nickel, and hybrid coatings can be applied to bearings, tools, and metal devices in extremely thin layers that, nevertheless, are highly resistant to damaging forces. That means that they can be added without, in most cases, significantly changing an item’s design specifications. This is important in scenarios where the need for a coating is identified after an item has been produced or is already in use.
A more effective strategy for preventing or minimizing contact fatigue and abrasion is incorporating a metal coating into their design. Coatings can achieve absolute atomic adhesion and reach areas like curves, holes, and recesses to provide maximum protection.
Identifying and Acting on Metal Coating Requirements
Ultimately, the first step toward protecting metal items is determining where a coating can provide needed shielding from damaging forces. This approach also helps lower replacement costs, minimize maintenance requirements, and prevent catastrophic metal failure.
From there, a coatings provider can help designers, manufacturers, or users develop a strategy for coating items efficiently and effectively.