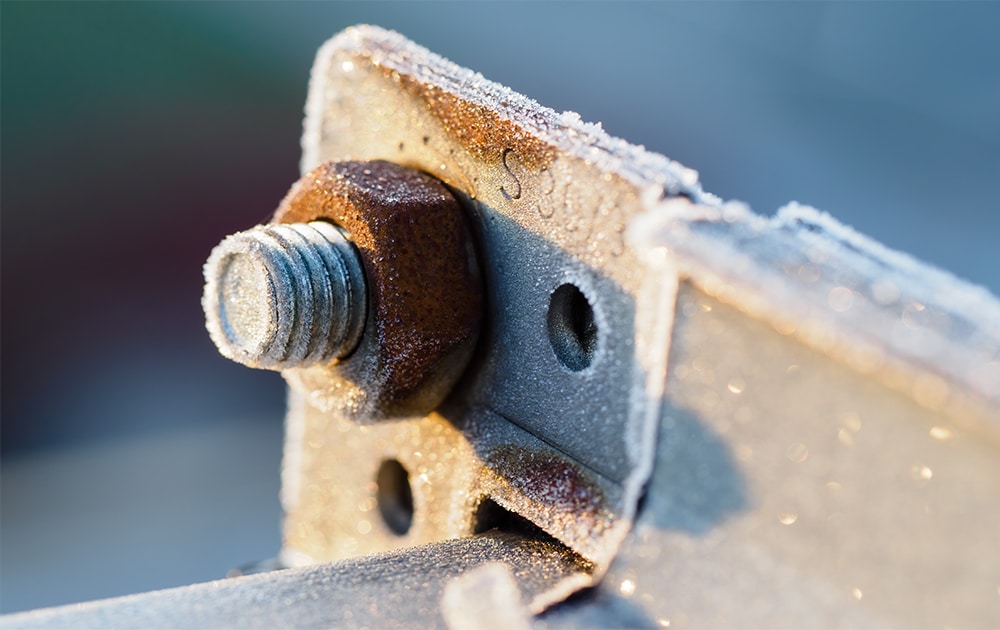
Galvanic corrosion, also known as bimetallic corrosion or dissimilar metal corrosion, is an electrochemical process that occurs when two different metals are in contact with each other in the presence of an electrolyte, such as saltwater or moisture.
Present across many sectors, galvanic corrosion poses a significant risk to the structural integrity and functionality of metal components. Where dissimilar metals are in proximity — pipelines, boats, bridges, and electrical connections — the electrolytic environment exacerbates the corrosive process.
One common scenario of corrosion is in marine environments, where ships and boats are constructed using various metals, such as steel hulls with bronze or stainless steel fittings. The seawater acts as the electrolyte, facilitating galvanic corrosion between these different metals, particularly in areas where they are in direct contact or proximity. Another prevalent scenario occurs in plumbing systems, where copper pipes are connected to brass or galvanized steel fittings. In the presence of water or moisture, galvanic corrosion can occur at these junctions, compromising the integrity of the plumbing network over time.
In this post, we’ll provide an overview of the key concepts involved in galvanic corrosion and how to mitigate the effects with preventative chromium coating solutions. You can jump to any section using the guide below:
What is Galvanic Corrosion: Key Concepts
Galvanic corrosion stems from the fundamental principle of electrochemical potential difference, where dissimilar metals in contact with an electrolyte undergo a spontaneous redox reaction. This reaction occurs due to the variation in the metals’ tendencies to lose or gain electrons, known as their electrochemical potentials. Understanding galvanic corrosion depends on two essential concepts: the galvanic series and the surface area effect.
Galvanic Series

Figure 1: The galvanic series for selected alloys in seawater.
The galvanic series is a list of metals in order of decreasing electrochemical potential, and it describes whether one metal is anodic or cathodic to another metal in a particular environment. That last part is important; these relationships are only true in the specific environment used for testing. The most common galvanic series to see in print is for seawater, but many others are available.
-
- When two metals with different electrochemical potentials come into contact, an electrical potential difference is established between them. The metal with a higher tendency to lose electrons (the more “active” metal) becomes the anode, undergoing oxidation and releasing electrons.
- Conversely, the metal with a lower tendency to lose electrons (the more “noble” or “passive” metal) becomes the cathode, accepting electrons and undergoing reduction. This flow of electrons constitutes an electrical current, leading to the corrosion of the anodic metal and the protection of the cathodic metal.
- Noble metals, such as gold and platinum, exhibit high corrosion resistance and typically serve as cathodes in corrosion scenarios. In contrast, less noble metals, such as aluminum, zinc, and magnesium, are more prone to corrosion and act as anodes.
We consider two metals compatible if their emf values fall within 0.25V of each other on the galvanic series. If their difference exceeds 0.25V, we expect the metal with the higher Anodic Index, the more anodic metal, to corrode.
While the galvanic series provides a foundational and general understanding of the galvanic potential of metals and alloys, the galvanic corrosion chart offers more specific, practical applications tailored to various engineering contexts. Below is a galvanic corrosion chart and guidelines on how to read it effectively to assess metal compatibility.
Galvanic Corrosion Chart
Metal | Galvanic Series Position | Potential (V) |
---|---|---|
Magnesium | Most Anodic (Most Active) | -1.75 |
Zinc | -1.10 | |
Aluminum Alloys | -0.90 to -1.00 | |
Cadmium | -0.75 | |
Mild Steel | -0.68 | |
Cast Iron | -0.60 | |
Chromium Steel (Active) | -0.56 | |
Lead | -0.55 | |
Tin | -0.49 | |
Nickel (Active) | -0.44 | |
Brass | -0.40 | |
Copper | -0.34 | |
Bronze | -0.30 | |
Chromium Steel (Passive) | -0.20 | |
Nickel (Passive) | -0.15 | |
Silver | -0.15 | |
Titanium | -0.10 | |
Gold | -0.05 | |
Platinum | Most Cathodic (Least Active) | 0.00 |
Galvanic Corrosion Chart Explanation
- Anodic (Active) Metals: Metals listed towards the top of the chart (most anodic) are more likely to corrode when in contact with metals listed lower in the chart.
- Cathodic (Noble) Metals: Metals listed towards the bottom of the chart (most cathodic) are less likely to corrode.
- Galvanic Potential: The potential difference between two metals determines the likelihood and rate of corrosion. A larger potential difference means a higher risk of corrosion for the anodic metal.
Galvanic Corrosion Chart Usage Instructions
- Identify Metals: Locate the two metals you are interested in from the chart.
- Compare Positions: Note their positions on the galvanic series.
- Determine Potential Difference: The metal higher up (more anodic) is at risk of corrosion when in electrical contact with the metal lower down (more cathodic).
- Preventive Measures: Use insulating materials, apply coatings, or choose metals closer in potential to minimize galvanic corrosion.
How Surface Area Affects Metal Corrosion
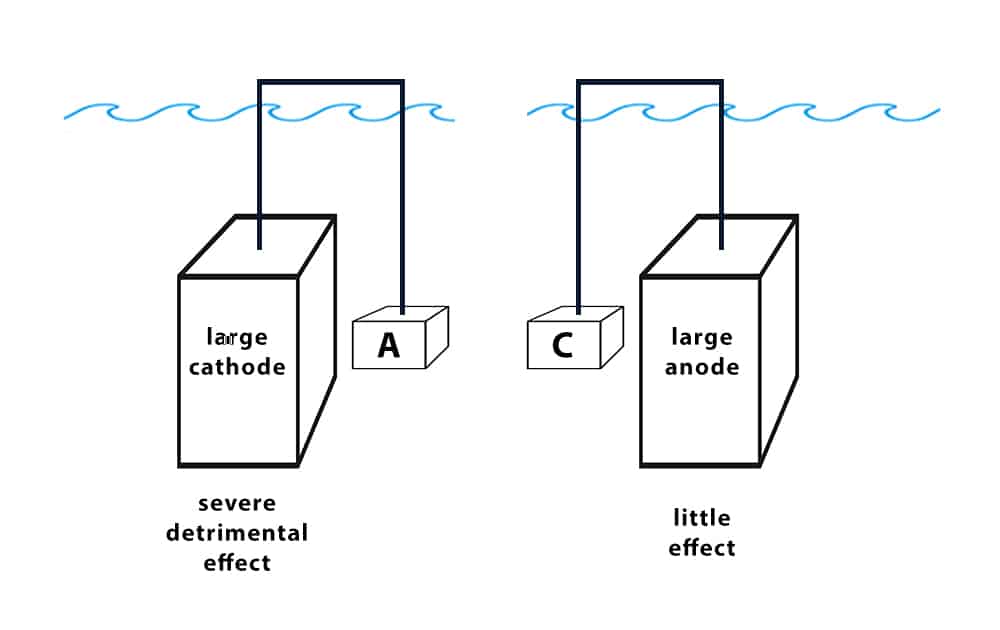
Figure 3: Illustration of how surface area affects galvanic reaction. A large cathode-to-anode ratio will result in accelerated corrosion.
The relative surface area of the anode to the cathode impacts galvanic corrosion rates. The surface area effect tells us that if the area of the anode is much smaller than that of the cathode, then corrosion of the anode will be much worse. If the area of the anode is much larger, corrosion will be less severe.
An unfavorable ratio of cathode area to anode area could make couples that we normally expect to work fine incompatible. This becomes especially important when we discuss metallic coatings for corrosion.
-
- Armoloy TDC works against corrosion by functioning as a barrier coating, preventing the environment (electrolyte) from contacting the base metal.
- Its ability to prevent corrosion depends on the coating being free from pinholes and other defects exposing the base metal.
A Visual Perspective
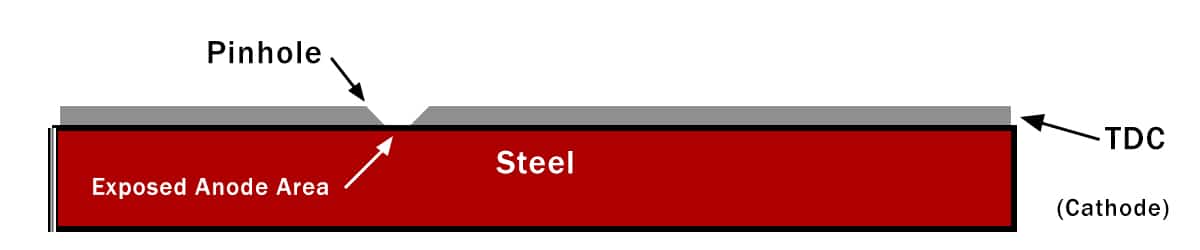
Figure 4: Illustration of how pinholes in the coating can create an unfavorable ratio of cathode area to anode area. Here, the area of exposed steel is very small while the area of exposed TDC is much larger.
Consider the case illustrated in Figure 2 (below), where Armoloy TDC is applied to a steel substrate. A pinhole creates a situation where we have a very large surface area of TDC and a very small surface area of steel exposed to the environment. Looking at the galvanic series in Figure 1, we see that TDC has an emf of 0.5V and steel an emf of 0.75V.
Under normal circumstances, these two are 0.25V apart and should have moderately good compatibility. With the unfavorable area ratio though, the exposed steel will quickly corrode. Conversely, the area effect works in favor when TDC is applied to metals appearing higher in the galvanic series like brass and bronze.
Additional Causes Galvanic Corrosion
-
- Conductivity: Metals with higher conductivity facilitate the flow of electrons in the galvanic cell, accelerating the corrosion process.
- Electrolyte composition: The composition of the electrolyte, including pH level, salinity, and presence of other corrosive agents, significantly affects galvanic corrosion rates.
- Temperature: Higher temperatures generally increase the rate of corrosion reactions, including galvanic corrosion.
- Environmental conditions: Humidity, atmospheric pollutants, and exposure to environmental chemicals can also influence galvanic corrosion rates.
Galvanic Corrosion Effect on Materials
This type of corrosion poses a significant threat to materials whenever two dissimilar metals come into contact with an electrolyte. For instance, pairing aluminum with stainless steel, stainless steel with carbon or alloy steel, and copper with carbon or alloy steel can lead to galvanic corrosion. In these combinations, the difference in electrochemical potentials between the metals initiates a corrosive process, accelerating the degradation of the less noble metal.
The impact of galvanic corrosion extends beyond mere material degradation. It can severely compromise the structural integrity, aesthetics, and functionality of components or structures.
-
- Structural Integrity: Galvanic corrosion can compromise the strength and stability of structural elements, leading to unexpected failures in critical infrastructures such as bridges, pipelines, and offshore platforms.
- Aesthetics: Galvanic corrosion can result in unsightly surface blemishes, discoloration, and pitting on metal surfaces, therefore affecting the visual appeal of architectural structures, automobiles, and consumer goods.
- Functionality: In functional applications, such as electrical connections or mechanical joints, galvanizing corrosion can impair performance and reliability.
Common Examples of Galvanic Corrosion
Galvanic corrosion has caused significant challenges across various industries, often resulting in material failures and, in some cases, catastrophic consequences. Below are some common examples of galvanic corrosion, along with historical instances and preventative measures where applicable:
Marine Environments
Saltwater is one of the most corrosive environments, creating ideal conditions for galvanic corrosion. Marine applications often involve dissimilar metals, such as aluminum hulls and stainless steel fittings, which can experience accelerated galvanic reactions due to the electrolyte-rich environment. This is a critical concern for the marine industry, as hulls, propellers, and submerged components are susceptible to metal corrosion in saltwater.
- Historical Example: The sinking of the U.S.S. Thresher in 1963 highlighted the vulnerabilities of submarines to dissimilar metal corrosion. Investigations revealed that contact corrosion occurred in piping systems where different metals interacted under high-pressure saltwater conditions.
- Preventative Measure: Coatings like Armoloy Thin Dense Chrome (TDC) create a protective barrier that prevents the electrolyte from contacting the base metal, reducing the risk of bimetallic corrosion and extending the lifespan of marine components.
Plumbing Systems
In residential and commercial construction, galvanic corrosion occurs frequently at the junctions of copper pipes and galvanized steel fittings. Water is the electrolyte, accelerating metal corrosion and leading to material degradation over time. This type of contact corrosion is a significant challenge in infrastructure projects, mainly where mixed materials are used.
- Historical Example: In the 1950s and 60s, multi-family housing developments reported widespread failures in plumbing networks due to bimetallic corrosion at copper-steel connections. These failures resulted in leaks and expensive repairs.
- Preventative Measure: Dielectric unions and protective coatings can mitigate galvanic action by separating dissimilar metals. Using a galvanic corrosion table during the design phase ensures better material selection to prevent corrosion.
Transportation Infrastructure
Bridges, railways, and other transportation infrastructure often feature connections between dissimilar metals, such as steel and aluminum. Coastal and humid environments exacerbate contact corrosion, particularly where these materials are exposed to moisture. The galvanic effect is amplified in such settings, especially when the anodic material has a smaller surface area.
- Historical Example: The collapse of the Silver Bridge in 1967, though primarily due to stress corrosion, highlighted the importance of considering galvanic corrosion risks in structural connections.
- Preventative Measure: Applying protective coatings like Armoloy TDC to fasteners and joints can reduce galvanic action and improve the durability of infrastructure. Engineers can also use the anodic index to ensure materials are compatible.
Medical Equipment
Medical devices and surgical tools often combine stainless steel, titanium, and other metals to meet specific functional requirements. However, galvanic corrosion poses a unique challenge for the medical industry, as devices are frequently exposed to saline solutions, blood, or moisture, creating an electrolyte-rich environment. Medical equipment failure due to bimetallic corrosion can severely affect patient safety.
- Historical Example: In the 1990s, corrosion at stainless steel-titanium connections in orthopedic implants caused failures that required revision surgeries. This highlighted the need for better materials and coatings to prevent metal corrosion in medical devices.
- Preventative Measure: Armoloy TDC coatings are biocompatible and highly effective in preventing galvanic reactions in medical equipment, ensuring safety and long-term functionality.
Automotive and Aerospace Applications
In the automotive and aerospace industries, galvanic corrosion presents significant challenges due to the use of diverse material combinations exposed to harsh environments. Aircraft and automobiles often pair aluminum with carbon fiber composites to reduce weight. These pairings create a high-risk scenario for galvanic action when moisture penetrates interfaces, initiating corrosion and weakening structural components.
- Historical Example: The Aloha Airlines Flight 243 incident in 1988 exposed vulnerabilities where dissimilar metal corrosion contributed to fuselage deterioration over time.
- Preventative Measure: High-performance coatings like Armoloy TDC create a durable barrier against electrolytes, mitigating the galvanic effect and extending the lifespan of critical aerospace and automotive components.
Monuments and Sculptures
Outdoor sculptures and monuments suffer from contact corrosion when stainless steel fasteners are used with copper or bronze. Atmospheric moisture and pollutants amplify the galvanic effect, causing discoloration and structural damage. This is a common challenge in construction and restoration projects.
- Historical Example: The Statue of Liberty underwent extensive renovations in the 1980s to address bimetallic corrosion between its copper skin and iron armature, which had deteriorated over decades.
- Preventative Measure: Using insulated fasteners and applying protective coatings can prevent galvanic corrosion, preserving the aesthetic and structural integrity of monuments for future generations.
How to Prevent Galvanic Corrosion
Several strategies can be implemented early in the engineering design process to mitigate the damaging effects of galvanic corrosion:
-
- Material Selection: Opt for metals close together in the galvanic series when possible.
- Cathodic Protection: Introduce an external anode thus making the metal act as a cathode.
- Coatings: Apply protective coatings to shield metal surfaces from the environment and prevent the electrolyte from making contact.
- Control Electrolyte Composition: Alter the composition or use inhibitors to reduce corrosion rates.
- Design Considerations: To decrease corrosion rates, ensure anodic areas are larger than cathodic areas.
- Regular Inspections: Detect early signs of corrosion and employ techniques for assessing corrosion severity.
Working with Armoloy
With a focus on precision, Armoloy coatings are engineered to withstand harsh environments and provide long-lasting protection against corrosion. By combining expertise with innovation, we deliver tailored solutions that extend product and component lifespan.