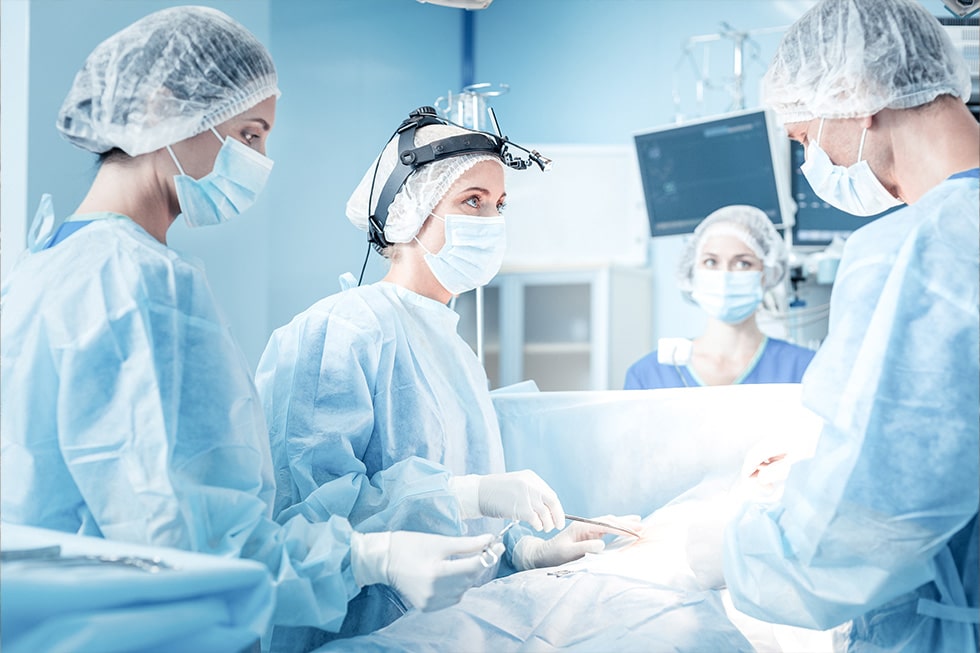
Choosing biocompatible materials for surgical instruments is of the highest importance in the medical and dental industries. To fully deliver on form and function, however, biocompatible coatings should also factor into the product equation.
Developed for the medical device industry, stainless steel surgical instruments with biocompatible coatings are easy to decontaminate after each procedure, and they also offer an aesthetically pleasing look and feel.
In this post, we’ll answer some of the most common questions regarding biocompatible coatings and explain why ME-92 biochrome coating is the top choice among healthcare professionals.
Question 1: Why are biocompatible materials important in a surgical setting?
Biocompatibility is a term that describes a material that is compatible with living tissue, meaning it will not cause allergic or other unwanted reactions during contact or implantation.
The human immune system works in such a way that when germs or a foreign agent enters our bodies, there is a natural response to the invader. In cases where non-biocompatible materials are used in surgery and dental work, patients can experience rashes, allergic responses, and sometimes, even life-threatening postoperative complications.
While stainless steel is often used in biomedical applications, exposure to chemicals or extreme temperatures will result in corrosion if surgical instruments are left untreated. The corrosion process degrades stainless steel surgical instruments, compromising their strength, appearance, and safety profile.
This is precisely why you should opt for the additional protection biocompatible coatings provide. High quality chromium coatings providers must meet stringent ISO 10993 and USP Class VI testing standards to be considered safe for surgical use.
Question 2: How durable are biocompatible materials?
Biocompatible materials are extremely durable, handling everything from radiation to cleaning.
In fact, ME-92 biochrome coating offers up to 80Rc surface hardness for a durable, non-reflective finish. Furthermore, biochrome increases wear resistance and surface hardness, maintains cutting edges, eliminates galling, fretting, spalling, and provides a hard, scratch resistant, non-stick, easy clean surface.
Question 3: How do biochrome coated instruments perform during surgery?
We all know the importance of light in the operating room. Precision is required, and visibility is a key prerequisite. However, uncoated stainless steel surgical instruments reflect high intensity light, causing extreme glare.
To combat this issue, apply a non-reflective biochrome coating to surgical devices. Not only does this reduce refraction and glare, but chromium coatings also ensure that surgical equipment functions as expected, every time.
Question 4: Are biocompatible materials prone to chipping?
Bare biocompatible materials without protective coatings are prone to peeling and chipping, risking dangerous debris in the tissue during surgery.
This is not the case when choosing to utilize biochrome coatings. Bonded directly to the base material, usually stainless steel, the chromium coating adheres completely—it will not chip, flake or peel. Also highly ductile, the coating will not separate from the base material, making it an ideal candidate for surgical and dental instruments.
Question 5: How do routine sterilization processes impact surgical instruments with biochrome coating?
One of the most important characteristics of biochrome coating on surgical instruments is surface protection. The instruments will maintain their surface integrity after repeated sterilization cycles.
For example, biochrome coated surgical instruments can endure various types of cleaning, including steam autoclave, boiling, bleaching, detergent scrubbing—and even gamma x-ray sterilization. They also have a non-stick surface, making it easier to prepare the surgical devices for the next procedure.
Paving the way for biochrome coatings
Three decades have passed since ME-92 became the first company to introduce the medical community to biochrome coatings. We still adhere to the same goal: offer functional coatings that enhance overall performance of surgical instruments, while exceeding our clients’ expectations of quality and affordability. Over the years, we’ve developed non-reflective finishes, and a coating for aluminum, which is lighter and less expensive than stainless steel, but still provides a high level of performance. For the next 30 years, ME-92 will continue to innovate for our clients.