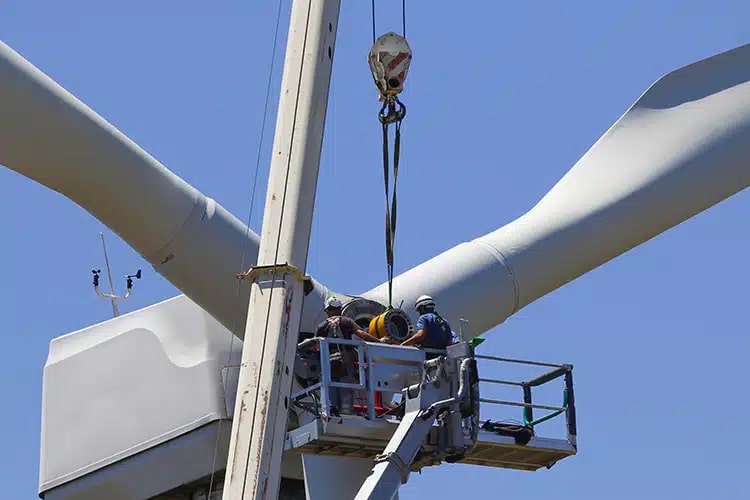
From the Pacific Gas and Electric Company groundwater pollution in Hinkley, California to the chromium spill at the Fairbanks Morse Engine facility in Beloit, Wisconsin. hexavalent chromium contamination due to inadequate process controls and oversight has extensive documentation. This is why it is paramount to work with reputable providers who adhere to quality and compliance standards to protect the environment.
But think, for a moment, if we flipped the script. Could the use of thin dense chrome coatings actually provide energy savings — a clear environmental benefit? Here, we’ll look at thin dense chrome as an energy-saver across a variety of applications, from manufacturing and transportation to renewable energy generation.
The energy cost of friction and wear
Typically, thin dense chrome plating requires lower plating times compared to hard chrome plating, resulting in lower energy consumption and reduced greenhouse gas emissions.
Now, let’s consider friction, one of the most common causes of metal failure and wear. Whether or not it occurs depends on a number of interrelated factors, including material properties, surface roughness, lubrication, temperature, pressure, and contamination, to name a few.
Friction has significant business, safety, and yes, environmental repercussions. Reducing friction through the use of thin dense chrome coatings can have significant energy-saving benefits across a variety of industries and applications. Let’s explore a few.
Reducing friction to improve efficiency
Nearly every industry, from manufacturing and transportation to renewable energy, utilizes machined components that are conducting heat due to friction, thus making the potential impact of even a small reduction in friction significant.
Manufacturing
Manufacturing processes often involve the use of various machinery and equipment with moving parts. Applying thin dense chrome coatings to gears, bearings, shafts, and other components enables smoother operation while minimizing energy losses and carbon emissions due to frictional resistance.
Similarly, In manufacturing processes that involve molding or forming operations, then dense chrome coatings can be applied to molds, dies, or tooling surfaces. The low friction properties of the coatings facilitate the easier release of the finished products from the molds or dies, reducing the energy required for demolding or part ejection.
Transportation
Automotive, rail, and aircraft components — everything from engine parts, piston rings, and bearings to valve trains and cylinder liners — can take advantage of thin dense chrome to reduce friction and improve fuel efficiency. This can result in significant energy savings on a global scale, as the transportation sector is a major contributor to greenhouse gas emissions.
In some cases, failure to mitigate excessive heat due to friction can have a direct and immediate impact on the environment, as seen in the Norfolk Southern freight train derailment in East Palestine, Ohio.
Mining, oil, and gas
The mining process is extremely energy-intensive. In fact, some estimates put the total global energy consumption of mining and mineral industries at up to 7% of the total global energy output — most of this consumption is due to friction and wear losses, according to AZoMining.com. “The friction and wear losses in the mining industry could be reduced by 15% in the short term of 10 years, as well as by 30% in the long term (20 years) by improving the design of moving parts and surfaces.” This includes utilizing high-performance thin dense chrome coatings.
Processing and material handling
Thin dense chrome coatings are appliable to surfaces involved in processing, packaging, and material handling, such as conveyors, chutes, or slides. By reducing friction between the materials and these surfaces, the coatings facilitate smoother movement and flow of the materials. This allows for more efficient material handling processes, reducing the energy needed to transport or transfer materials within the manufacturing facility.
Renewable energy
In renewable energy systems, certain components are subjected to wear due to friction, abrasion, or contact with other materials. Thin dense chrome coatings are particularly beneficial in wind turbines, where TDC coatings can be applied to gearbox components, shafts, and bearings. This can lead to increased energy output and reduced maintenance costs in renewable energy systems, contributing to a more sustainable energy future.
Finished wind turbine gearboxes.
Reducing friction to extend equipment lifespan
In all of the industries and applications we’ve discussed, by reducing wear and minimizing the need for frequent component replacements, thin dense chrome coatings help extend the lifespan of the equipment. This not only saves energy necessary for manufacturing new equipment but also reduces associated energy consumption with equipment maintenance and downtime — and of course, it also affects the bottom line.
Case in point: in the previous mining example, of the total global annual economic losses due to friction and wear, “40% is distributed to overcoming friction while the rest of the 60% of losses are distributed in production of replacement parts and spare equipment, maintenance work, and lost production.”
Reducing friction to lower emissions and deter pollution
Reducing friction by utilizing thin dense chrome also contributes to a reduction in pollution, including greenhouse gas emissions, air pollutants, waste generation, and noise pollution.
We’ve provided some examples of how mitigating friction can improve efficiency. Friction between moving parts consumes energy, which often comes from fossil fuel sources. When less energy is necessary to perform the same task, fewer emissions of pollutants associated with energy generation follow – namely, there is a reduction in carbon dioxide (CO2), sulfur dioxide (SO2), and nitrogen oxides (NOx).
Similarly, in transportation, by minimizing friction, less energy is lost as heat, and more energy is utilized for propulsion. This results in improved fuel efficiency, meaning that vehicles require less fuel to cover the same distance. Reduced fuel consumption directly leads to lower emissions of pollutants, including greenhouse gases, particulate matter, and toxic compounds, which contribute to air pollution and climate change.
Finally, friction between moving parts can generate noise pollution, especially in industrial and transportation settings. Noise pollution can have detrimental effects on ecosystems, wildlife behavior, and human health. Thin dense chrome coatings can reduce friction and noise, improving the working environment and potentially reducing the need for hearing protection.
Overall, the implementation of thin dense chrome coatings to reduce friction not only enhances performance and efficiency but surprisingly, also yields environmental advantages. Through energy conservation, improved fuel efficiency, extended equipment lifespan, and noise reduction, thin dense chrome coatings play a valuable role in fostering a more sustainable and environmentally friendly approach across various applications and industries.
Environmental excellence at Electrolizing®
Through our commitment to safety, quality, and the environment, we have earned the trust of many global OEMs as their supplier of choice. The Armoloy Innovation Center has staff metallurgists on site and provides metallurgical science services including friction testing.