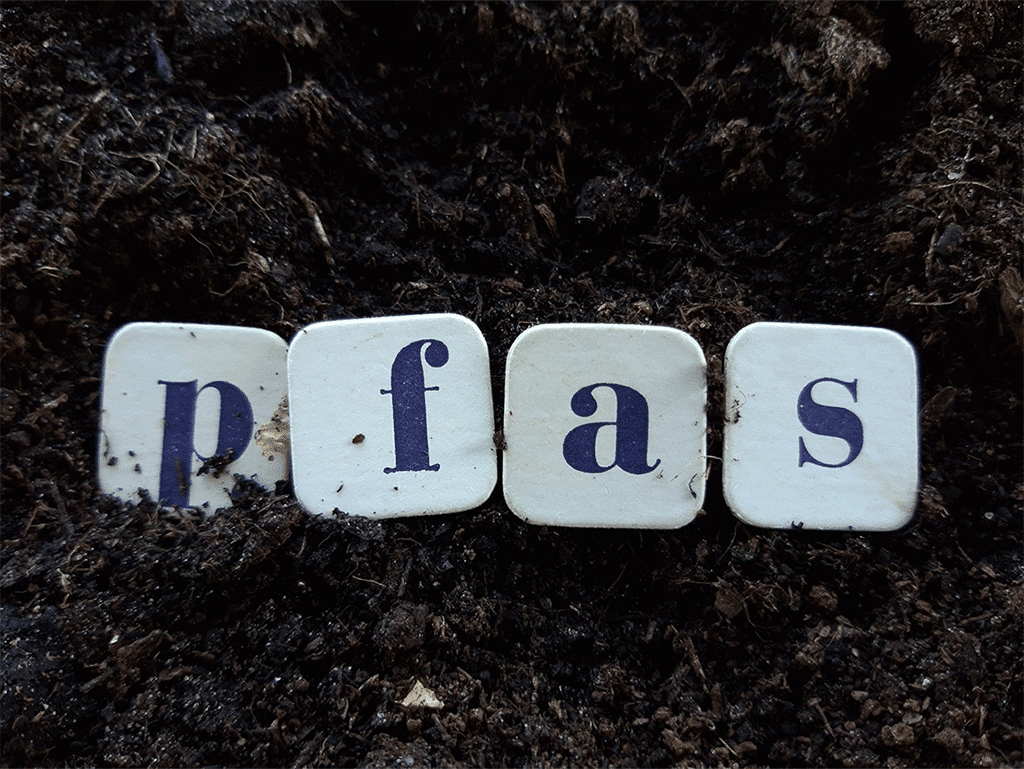
What is PFAS?
PFAS, or Per- and Polyfluoroalkyl Substances, are a large group of synthetic chemicals defined by their exceptionally strong carbon-fluorine bonds. Carbon-fluorine bonds make PFAS chemicals highly resistant to heat, water, oil, and strains. These unique properties have made PFAS integral to various industries and products.
In this guide on PFAS, we’ll discuss:
- PFAS Impact on Metal Finishing
- PFAS Impact on Wastewater
- Alternatives to PFAS
- Economic Impacts of PFAS Removal
- How Armoloy Addresses PFAS Concerns
Key industries and products that rely on PFAS include:
- Cookware: Nonstick coatings like those found on frying pans.
- Textiles: Waterproof and stain-resistant clothing and fabrics.
- Firefighting: Firefighting foams used for emergencies.
- Aerospace and Automotive: Critical industrial applications and manufacturing processes.
While PFAS are valued for their durability and performance, this same durability leads to environmental persistence, earning them the nickname “forever chemicals.”
The environmental and health implications of PFAS have garnered increasing concern. These chemicals have been found to accumulate in the environment and living organisms, including humans, leading to potential adverse health effects. Studies have linked PFAS exposure to a range of health issues, such as immune system effects, liver enzyme disruption, and in some cases, increased risks of certain cancers.
PFAS Impact on Metal Finishing
The issue of PFAS within the metal finishing industry has become significant and multifaceted, touching upon environmental, occupational health, and regulatory concerns. This complex scenario particularly intensified in the late 1990s. Regulatory bodies like the Environmental Protection Agency (EPA) and the Occupational Safety and Health Administration (OSHA) required the use of PFAS-containing fume suppressants as a measure to better protect workers from exposure to hexavalent chromium [Cr(VI)], a known carcinogen. And while most chrome platers today have long since phased out PFAS use, residual contamination is still present in many facilities.
Chrome plated component from a PFAS-free process
The Shift in Perspective
Initially, the recommendation for PFAS use was based on the priority of minimizing workers’ exposure to hexavalent chromium. However, as the understanding of PFAS’s environmental and health impacts deepened, scrutiny regarding exposure increased, particularly in wastewater. This has led to a challenging predicament for the metal finishing industry as they grapple with the dual objectives of protecting worker health and minimizing PFAS in the environment.
PFAS Impact on Wastewater
PFAS significantly impacts wastewater systems due to their persistent, bio accumulative, and toxic nature. When forever chemicals enter wastewater treatment plants (WWTPs), they present several challenges:
Persistence
PFAS resist conventional wastewater treatment processes due to their strong carbon-fluorine bonds. This resistance means that PFAS can pass through WWTPs largely unaltered, entering the aquatic environment and potentially contaminating surface water and groundwater.
Accumulation
Given their stability, forever chemicals accumulate in the environment. In wastewater contexts, sludge — the byproduct of wastewater treatment — can become a concentrated source of per- and polyfluoroalkyl substances. When this sludge is applied as fertilizer or disposed of in landfills, it can lead to further environmental dispersion and contamination of soil and water bodies.
Image of waste sludge from effluent treatment in contaminated water. Sludge that has been treated for forever chemicals and meets regulations is referred to as biosolids.
Detection and Removal Challenges
The wide variety of PFAS compounds (over 9,000 identified types) and their varying physicochemical properties complicate detection and removal. Conventional wastewater treatment plants are not designed to remove forever chemicals, requiring advanced and often expensive treatment technologies such as activated carbon adsorption, ion exchange, and high-pressure membranes (e.g., forward, reverse osmosis) for effective removal. Fortunately, in some scenarios, new PFAS-eliminating techniques are showing great potential for future cost-effective solutions.
Comparison of common PFAS removal techniques
Regulatory and Health Concerns
As awareness of PFAS health impacts grows, regulatory agencies are lowering acceptable limits in drinking water and the environment. Thus, increasing pressure on wastewater treatment systems in metal finishing facilities to remove these compounds. The presence of forever chemicals in wastewater can lead to drinking water contamination, posing health risks to communities.
Emerging Alternatives to Forever Chemicals
Forever chemicals are widely used in countless applications, from consumer goods like nonstick cookware and stain-resistant fabrics to industrial processes and firefighting foams. However, growing concerns about their environmental persistence and health risks have prompted industries and researchers to actively pursue safer and more sustainable alternatives.
Textiles and Apparel
In the textile industry, PFAS free alternatives are being developed to provide water and stain resistance without harmful chemicals. For instance, Evolved by Nature has introduced the Activated Silk™ L1 leather finishing system, which utilizes natural silk protein to create a durable, biodegradable finish, eliminating the need for per- and polyfluoroalkyl substances in leather products.
Cookware
Traditional nonstick cookware often relies on PFAS-based coatings like polytetrafluoroethylene (PTFE). Emerging alternatives include ceramic coatings derived from sand, as well as cookware made from stainless steel, cast iron, and titanium. These materials offer nonstick properties without the associated health risks of forever chemicals.
Nonstick frying pan with ceramic coating. Free of PFAS, PFOA, lead and cadmium
Food Packaging
In food packaging, efforts are underway to replace per- and polyfluoroalkyl chemicals with safer materials. Researchers and industries have identified uncoated alternatives, such as wax-coated wrappers and clay-coated plates, as viable options that reduce health hazards while maintaining functionality.
Firefighting Foams
Firefighting foams have traditionally contained PFAS for their effectiveness in suppressing fires. However, fluorine-free firefighting foams are being developed and adopted, offering comparable performance without the environmental persistence associated with forever chemicals.
Water and PFAS-free foam pump line for fire protection at a petroleum plant
Economic Impacts of PFAS Removal
Upgrading wastewater treatment systems to effectively remove forever chemicals involves significant capital and operational costs. The EPA estimates that implementing PFAS regulations will cost public water systems and regulatory agencies approximately $1.548 billion annually, encompassing expenses for monitoring, sourcing alternative water supplies, installing and maintaining treatment technologies, and managing treatment residuals.
The financial burden varies across communities. For example, the Houlton Mobile Home Park in Maine is undertaking a public water connection project exceeding $4 million due to elevated PFAS levels in well water. Larger water districts anticipate treatment costs ranging from $5 million to $10 million, underscoring the significant variability in economic impacts.
Beyond these direct costs, contamination of forever chemicals has far-reaching implications. Property values can decline in affected areas, and industries such as agriculture and tourism may face economic challenges due to contaminated resources. Furthermore, The Nordic Council of Ministers estimates that health costs related to PFAS exposure in the European Economic Area range between 52 billion and 84 billion annually, highlighting the public health burden of these substances.
This diagram of PFAS sources illustrates the far reaching implications of contamination in water sources.
Despite these expenses, the investment in PFAS removal yields substantial health benefits. The EPA projects that reducing PFAS in drinking water will prevent over 9,600 deaths and approximately 30,000 serious illnesses annually, including cancers and cardiovascular diseases.
What Chrome Platers Need to Know
The EPA has been actively engaging with the metal finishing industry in California and across the United States to address concerns about PFAS contamination in wastewater. Specifically, there has been a dialogue between the EPA and the metal finishing industry regarding the collection of information to inform upcoming regulations on PFAS effluent limits. In response to feedback from industry stakeholders, the EPA made adjustments to its proposed Information Collection Request (ICR). These adjustments included reducing the total number of questions, narrowing the scope of remaining questions, and revising the estimated burden for facilities, aiming to address concerns that the initial version of the questionnaire was too expansive and burdensome.
Furthermore, the EPA outlined a comprehensive plan to better understand the discharge of forever chemicals by chrome finishers. This included visiting chrome plating facilities to gather information on the types of wastewaters being generated, the performance of existing treatment technologies and practices, and conducting a wastewater sampling campaign. These site visits are part of the EPA’s broader effort to collect data for setting PFAS wastewater discharge limits. The EPA aimed to ensure that these visits and data collection efforts would not be overly burdensome to facilities. The EPA also emphasized coordination with facilities to arrange site visits. They noted that they would protect any sensitive data collected during this process.
How Armoloy Addresses PFAS Concerns
The Armoloy Corporation takes a proactive stance on addressing PFAS challenges, prioritizing sustainable practices and advanced technologies to ensure environmental stewardship and workplace safety without compromising the quality or performance of our plating processes. Our approach is rooted in protecting our workers, our community, and our customers’ peace of mind. Here’s how we do it:
A Preferred Alternative to PFAS in Chrome Mist Control
At Armoloy, our preferred approach to managing chrome mist is simple: we avoid PFAS usage altogether. Replacing the need for PFAS additives, Armoloy uses best-in-class fume scrubbers to ensure a safer and cleaner workspace. These systems capture and remove hexavalent chromium vapors, preventing them from entering the air and protecting workers and local communities from harmful exposure.
- High-Efficiency Air Filtration: Designed to trap fine particles, including hazardous chrome mist, these systems release clean, safe air back into the environment.
- Compliance with Regulatory Standards: By prioritizing air quality and eliminating reliance on forever chemicals, Armoloy meets and often exceeds OSHA and EPA requirements, demonstrating our commitment to safety and accountability.
An advanced four-stage chrome separator seen at Armoloy Illinois, exclusively developed by ScrubAir Systems Inc.
Dedicated to Total Waste Reduction
Armoloy’s implementation of a zero discharge, closed-loop facility system is also a significant step in eliminating wastewater. This system ensures that all wastewater generated in plating processes is treated, analyzed, and properly disposed of at a specialized facility. Here’s how it contributes to sustainability and environmental protection:
- Minimizes Environmental Impact: Recycling water reduces the risk of releasing contaminants, including PFAS, into local water bodies, preserving ecosystems and promoting sustainability.
- Reduces Demand for Freshwater: The closed-loop system decreases the facility’s reliance on external water sources, which is particularly beneficial in regions where water scarcity is a concern.
- Ensures Complete Control Over Wastewater Treatment: Treatment systems provide precise management of contaminants, including PFAS, ensuring their safe handling and disposal.
Addressing the challenges associated with PFAS requires a multifaceted approach, including investment in advanced treatment technologies, active engagement with regulatory developments, and a commitment to environmental and public health responsibilities. It also underscores the importance of industry collaboration, research into alternative substances and processes, and advocacy for reasonable regulatory frameworks that recognize the technical and economic realities of metal finishing operations.
Work with a Reputable Partner
Armoloy’s deep understanding of environmental and safety requirements gives us a competitive edge, making us a reliable partner for customers across industries. Choosing Armoloy means choosing peace of mind. Our customers can trust that their supplier is not cutting corners or risking regulatory scrutiny. By relying on sustainable technologies instead of forever chemicals, Armoloy safeguards its workers, communities, and customers alike.
Rest easy knowing that your surface finishing supplier is setting the standard in environmental responsibility. With Armoloy, compliance and quality go hand in hand.
Share on LinkedIn Share on Facebook