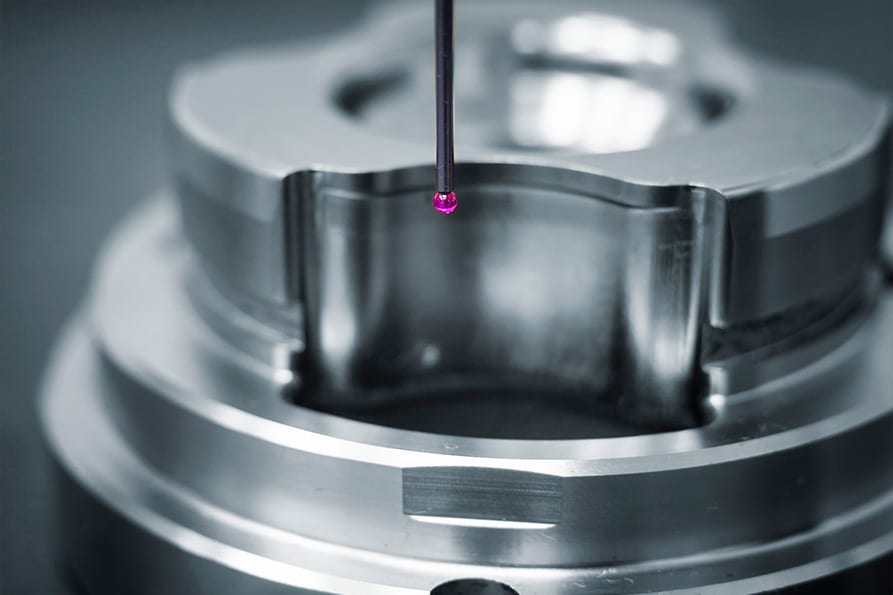
In an ideal world, product design, testing, and launch would go smoothly and as expected. Unfortunately, designers and manufacturers operate in the real world. And despite their best efforts, there are scenarios in which a design flaw no one could have anticipated becomes a very real and very costly problem.
In those situations, it is essential to work with a coatings provider that has several decades of experience and, as a result, can focus on finding the optimal solutions under intense pressure.
The Case of a Valve Shaft Design Flaw
Armoloy’s engagement with a valve manufacturer exemplifies the ability to participate in solving perplexing problems even as the customer nervously watches warranty-related costs shoot upward.
The valve in question was built to regulate the flow of spent combustion gasses. It had to operate reliably in an environment with large quantities of abrasive soot particles and temperatures exceeding 1,000 degrees Fahrenheit. The design included two “butterflies” mounted to a stainless-steel shaft, which rotated to approximately 90 degrees inside two highly wear-resistant alloy bushings.
The valve had been built, tested, and released to production. Only then did the company start to see a rapidly growing warranty expense. And with it, a rapid rise in everyone’s blood pressure.
Finding the Failure Point in a Design Flaw
As the company scrambled to identify and correct the problem, a metallurgical failure analysis was performed. It revealed that excessive wear was causing the shaft to bind. And worse, in some cases, the force on the stuck shaft actually broke it.
Facing “crunch time” in more ways than one, the company devised an elaborate bench test that involved high-flow burners to mimic the normal operating temperature, an integrated cooling system, and the ability to collect critical data about the failures.
Identifying the Ideal Solution Among Multiple Options
Using the bench test setup to look for fixes, the company experimented with alternative materials, surface coatings, and heat treatments. Ultimately, the shaft that performed best was one that had been coated in nitride and then chromium. That approach was selected and went into production. When it did, everyone breathed a sigh of relief.
The Case for Chromium as a Preventative Measure
An unfortunate reality in designing and manufacturing new items that face destructive forces or a design flaw is the limitations to the potential problems testing can reveal. For that reason, many companies choose to have Armoloy apply cost-effective chromium coatings as a preventative measure.
Coatings provide many benefits, from reduced wear to increased lifespan, so applying them is never a bad idea. And as the valve manufacturer discovered, the cost of assuming an uncoated part will function properly can be very high.
Not only did they incur the valve replacement cost and the time and expense of bench testing, they also potentially suffered reputational harm and lost business opportunities. Those are costs they will never be able to calculate. It is possible that avoiding those losses would have “paid for” chromium coatings many times over.
Gaining Insight in the Armoloy Innovation Center
Another way for companies to address potential problems from friction, corrosion, and other forces that can damage or destroy manufactured parts, components, and devices is for them to contact the Armoloy Innovation Center.
Doing so gives them access to 60+ years of experience and insights. They also benefit from the guidance of experts who know how to help innovative companies protect their products and ensure they do not develop costly material-related problems after production has begun.