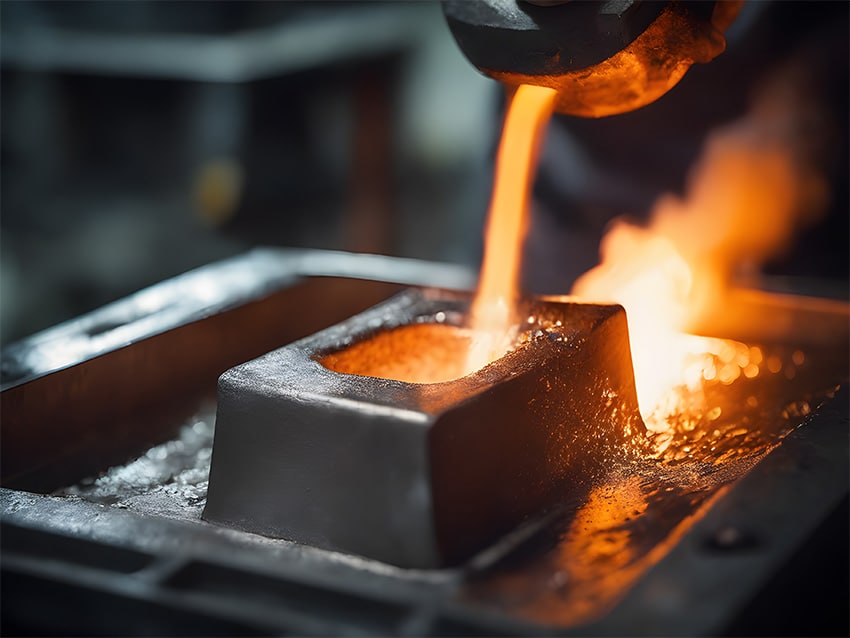
Abstract
The industrial sector increasingly seeks rapid-cycle, precision-molded, thin-walled components made from reinforced engineering thermoplastics. This growing demand puts a spotlight on the potential of high-strength copper alloys for copper mold production. Researchers have traditionally overlooked high-conductivity copper alloys due to doubts about their durability against wear from reinforced resins when used for copper molds. This study explores the effectiveness of various hard coatings – including different types of chrome coatings, electroless nickel, and titanium nitride – in safeguarding copper molds and alloys from erosive damage. Remarkably, certain combinations of these coatings with copper alloys exhibited wear resistance on par with that of the industry standard hardened H13 tool steel.
Methodology
This research encompassed an exhaustive testing of 20 unique combinations of base materials and coatings. This included three specific copper alloys, C18000, C17510, and C17200, evaluated both with and without protective coatings. The range of coatings tested comprised electroless nickel, titanium nitride (applied via high and low-temperature processes), industrial hard chrome, and two variations of Armoloy Thin Dense Chrome coatings. Comparisons were made with standard uncoated P20 and hardened H13 materials to establish a benchmark. The coatings varied in thickness, with electroless nickel at approximately .008mm (8µm) and electroplating at about .005mm (5µm).
Design & Measurement
The study’s methodology focused on several key variables. The depth of wear (measured at the resin impact point), the cycle count, and observable wear indications such as scratches and chips served as the dependent variables. Independent variables included the core substrate material and the coating applied. The study hypothesized that the most significant wear factors in the mold cavity were the glass fibers in the resin. Researchers collected data for the coated copper alloys through a meticulously planned screening experiment, utilizing both a custom-built gauge and a WYCO interference microscope for precise measurements.
Findings
The findings centered on two main areas: the comparative effectiveness of the hard coatings and their adhesion quality to the base substrates. Notably, Armoloy XADC® (diamond chrome) coatings showed exceptional performance, particularly on the softer copper mold alloys. A marked statistical difference was found between the highest-performing coated combinations and all others. Conversely, titanium nitride demonstrated a tendency to flake off rapidly from the C17200 alloy. It was observed that the high-temperature application of titanium nitride diminished the base alloy’s hardness. Electroless nickel, on the other hand, consistently provided a uniform coating, outperforming TiN and industrial hard chrome in terms of deposition uniformity and reducing the incidence of chipping at sharp edges.
Conclusions
The investigation concludes that certain chrome coatings were the top performers in terms of durability. Although the performance of electroless nickel was slightly lower than chrome coatings, it offered benefits such as consistent coverage and less chipping on sharp corners. Researchers found that using titanium nitride, particularly in its high-temperature application, shortened the lifespan of C17200 compared to uncoated samples. Overall, chrome-based coatings were highly effective in providing erosion resistance in copper molds, rivaling or surpassing hardened H13. The study emphasizes the critical role of choosing a proficient plating service provider, adept in handling various materials, to ensure the longevity and high performance of coated surfaces.
Table 1 – Average cycles to failure per plated an un-plated alloys
Graph 1 – Core pin life comparison of coatings and uncoated surfaces
Drawing of core pin geometry