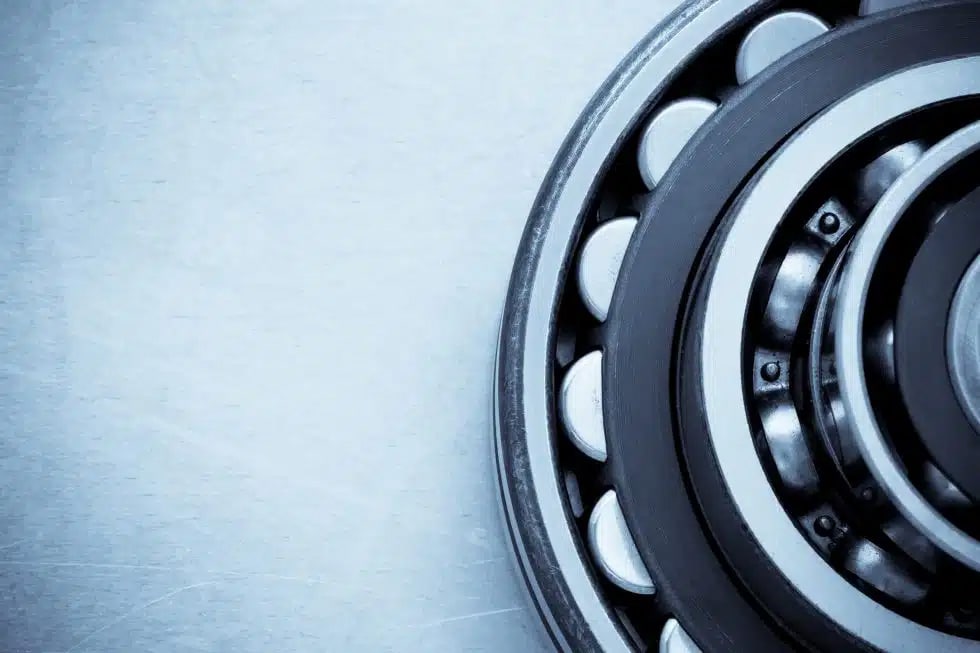
Companies that design or manufacture metal items like bearings, rollers, and gears are familiar with rolling contact fatigue (RCF). So are end-users of devices and equipment that use these items. Even if those users do not know RCF by name, they understand and experience its consequences.
RCF is a destructive force that affects curved surfaces. It produces cracks and removes material from those surfaces until they ultimately fail. And the force-producing that effect is not necessarily excessive. The repeated alternating application of normal pressure can cause RCF and item failure.
Fortunately, there is a simple, cost-effective step that businesses can take to reduce RCF in their products significantly. They can have a chromium coatings company apply an incredibly thin but highly protective layer of a material like thin dense chrome, diamond chrome, or others to metal components that are subject to that force.
Organizations that take that step benefit in many ways, including financially and operationally.
Financial Benefits of Addressing RCF With Chromium Coatings
Coating metal bearings, rollers, and other items with chromium is an investment. Some companies may be hesitant to “make the leap.” However, when they take the time to understand the payoff from that investment, they see that the benefits far outweigh the cost.
For example, metal parts coated with chromium have extended lifespans. That fact alone can significantly decrease a company’s long-term costs. If a particular uncoated asset fails after four years and the same item with a chromium coating lasts six years, that is a 50% decrease in replacement costs. And that, of course, makes procurement professionals very happy.
But lower costs are not the only financial benefits companies enjoy. Many also see an improvement in their reputation and a corresponding increase in sales. Word gets around when metal parts, devices, and equipment last longer. And soon, leads start coming in at an accelerated rate.
Operational Advantages of Chromium Coatings to Minimize RCF
Equipment and machines eventually experience decreased performance or complete failure. That is an unavoidable fact.
However, when those breakdowns occur frequently or unexpectedly, it is stressful for everyone affected. That includes the companies that designed and manufactured the equipment, the people who use it, and the individuals who maintain it. And, of course, equipment downtime impacts profitability. Consequently, it affects people all the way up the management ladder.
Companies that invest in coating key components in chromium spend less time and money reacting to problems. That means their people have lower stress levels, and the organization has higher revenues.
Getting Started Is Simple
The science behind the development and application of chromium coatings is complex. But for companies wanting to have their metal parts coated, getting started is simple. All it takes is a brief phone call or exchange of emails with Armoloy to get details on the coating process, logistics, timeline, cost, etc.
For organizations that decide to move forward with coating their metal assets, all that remains then is scheduling the work. In many cases, coatings are applied as part of the manufacturing process. However, companies can also arrange for items they are already using to go out of service temporarily and receive a coating.
Armoloy can even coat proof-of-concept pieces as part of a designer’s development and testing processes. In any event, the first step in preventing rolling contact fatigue is for a company to reach out and learn about its options.